Plasma nitriding and Nitrocarburizing are both thermochemical surface hardening processes used to enhance the mechanical properties of metal parts, such as hardness, wear resistance, and fatigue life. However, they differ in their mechanisms, the elements introduced into the metal, and the resulting surface characteristics. Plasma nitriding involves the diffusion of nitrogen into the metal surface using a plasma environment, while Nitrocarburizing introduces both nitrogen and carbon into the surface layer. These differences lead to unique advantages and applications for each process.
Key Points Explained:
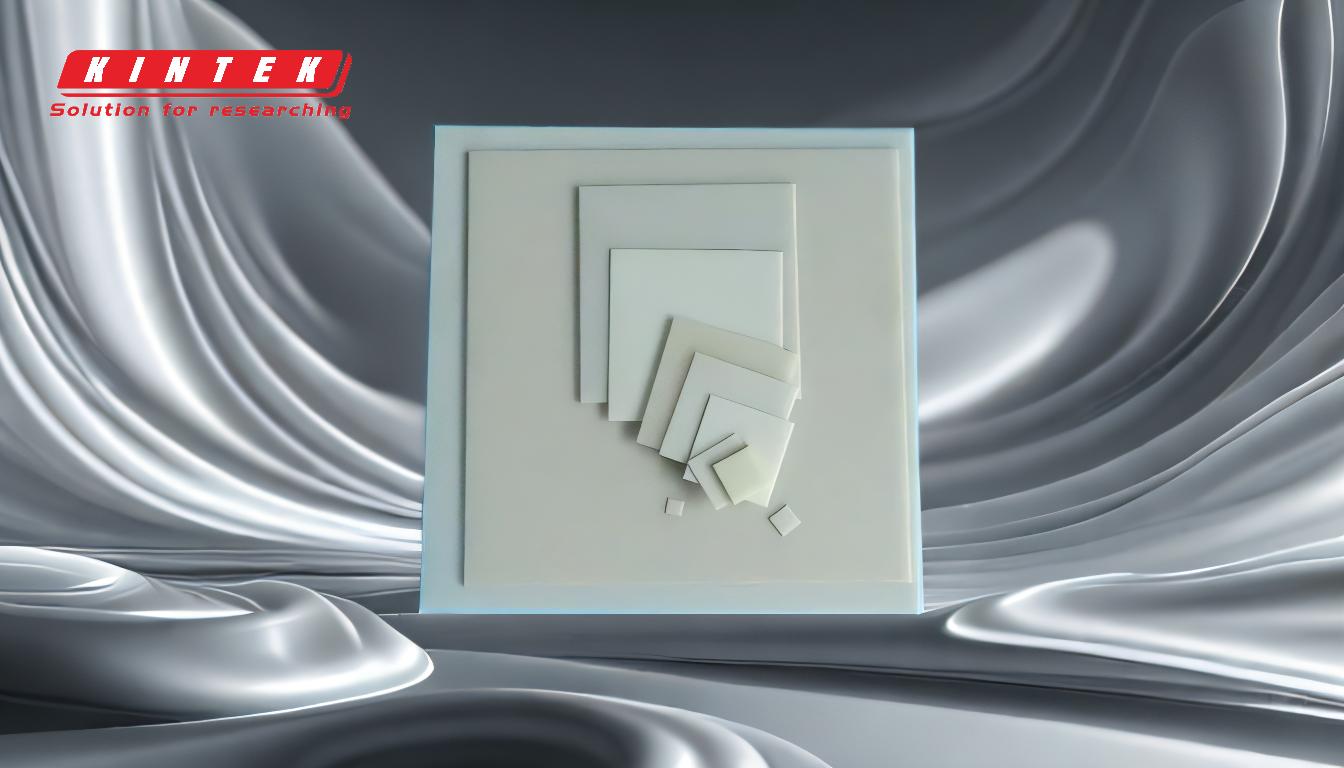
-
Mechanism of the Processes:
- Plasma Nitriding: This process utilizes a plasma environment to ionize nitrogen gas, which then diffuses into the metal surface. The plasma is generated by applying a high voltage between the workpiece (cathode) and the chamber walls (anode). The ionized nitrogen atoms are accelerated toward the workpiece, creating a hard nitride layer on the surface.
- Nitrocarburizing: This process involves introducing both nitrogen and carbon into the metal surface simultaneously. It is typically performed in a gaseous atmosphere containing ammonia (for nitrogen) and a carbon-rich gas (such as carbon dioxide or methane). The combined diffusion of nitrogen and carbon creates a compound layer and a diffusion zone beneath it.
-
Elements Introduced:
- Plasma Nitriding: Only nitrogen is introduced into the metal surface, forming nitrides that enhance hardness and wear resistance.
- Nitrocarburizing: Both nitrogen and carbon are introduced, resulting in a compound layer rich in carbonitrides and nitrides, which provides improved wear resistance and reduced friction.
-
Temperature and Process Control:
- Plasma Nitriding: Operates at sub-critical temperatures (typically between 350°C and 600°C), which minimizes distortion and allows for precise control of the nitride layer thickness.
- Nitrocarburizing: Also operates at sub-critical temperatures (usually between 500°C and 600°C), but the presence of carbon requires careful control of the gas composition to achieve the desired surface properties.
-
Surface Characteristics:
- Plasma Nitriding: Produces a hard, wear-resistant surface with minimal distortion. The process is particularly effective for complex geometries and thin-walled components due to its ability to uniformly treat intricate shapes.
- Nitrocarburizing: Creates a compound layer with excellent wear resistance and reduced friction, making it suitable for applications requiring improved sliding properties. The process also enhances corrosion resistance due to the formation of a dense compound layer.
-
Applications:
- Plasma Nitriding: Commonly used for high-precision components, such as gears, dies, and molds, where hardness and wear resistance are critical. It is also favored for materials like stainless steel and titanium, which benefit from the formation of a hard nitride layer.
- Nitrocarburizing: Ideal for components subjected to sliding wear, such as crankshafts, camshafts, and hydraulic cylinders. The process is also used for parts requiring improved fatigue strength and corrosion resistance.
-
Advantages and Limitations:
- Plasma Nitriding: Offers precise control over the nitride layer, excellent surface hardness, and minimal distortion. However, it requires specialized equipment and is more expensive than some other surface hardening methods.
- Nitrocarburizing: Provides a combination of hardness, wear resistance, and corrosion resistance. It is more cost-effective for certain applications but may not achieve the same level of hardness as plasma nitriding.
By understanding these key differences, equipment and consumable purchasers can make informed decisions about which process best suits their specific needs, whether they prioritize hardness, wear resistance, or cost-effectiveness.
Summary Table:
Aspect | Plasma Nitriding | Nitrocarburizing |
---|---|---|
Mechanism | Uses plasma to diffuse nitrogen into the metal surface. | Introduces both nitrogen and carbon into the metal surface. |
Elements Introduced | Nitrogen only. | Nitrogen and carbon. |
Temperature Range | 350°C to 600°C. | 500°C to 600°C. |
Surface Characteristics | Hard, wear-resistant surface with minimal distortion. | Compound layer with wear resistance, reduced friction, and corrosion resistance. |
Applications | High-precision components like gears, dies, and molds. | Components subjected to sliding wear, such as crankshafts and camshafts. |
Advantages | Precise control, excellent hardness, minimal distortion. | Cost-effective, improved wear resistance, and corrosion resistance. |
Limitations | Requires specialized equipment, higher cost. | May not achieve the same hardness as plasma nitriding. |
Need help choosing the right surface hardening process for your metal components? Contact our experts today for tailored advice!