Sputtering and Chemical Vapor Deposition (CVD) are two distinct thin-film deposition techniques used in various industries, each with unique processes, advantages, and applications. Sputtering is a physical vapor deposition (PVD) method that involves ejecting atoms from a solid target material using energetic ions, which then deposit onto a substrate. This process does not rely on heat, making it suitable for temperature-sensitive materials like plastics and organics. CVD, on the other hand, is a chemical process where gaseous precursors react on a substrate to form a solid thin film. It operates at higher temperatures and allows for uniform coating of complex geometries without requiring a line of sight. While sputtering is ideal for applications requiring precise control over film properties, CVD excels in creating high-quality, uniform films for semiconductor and optical applications.
Key Points Explained:
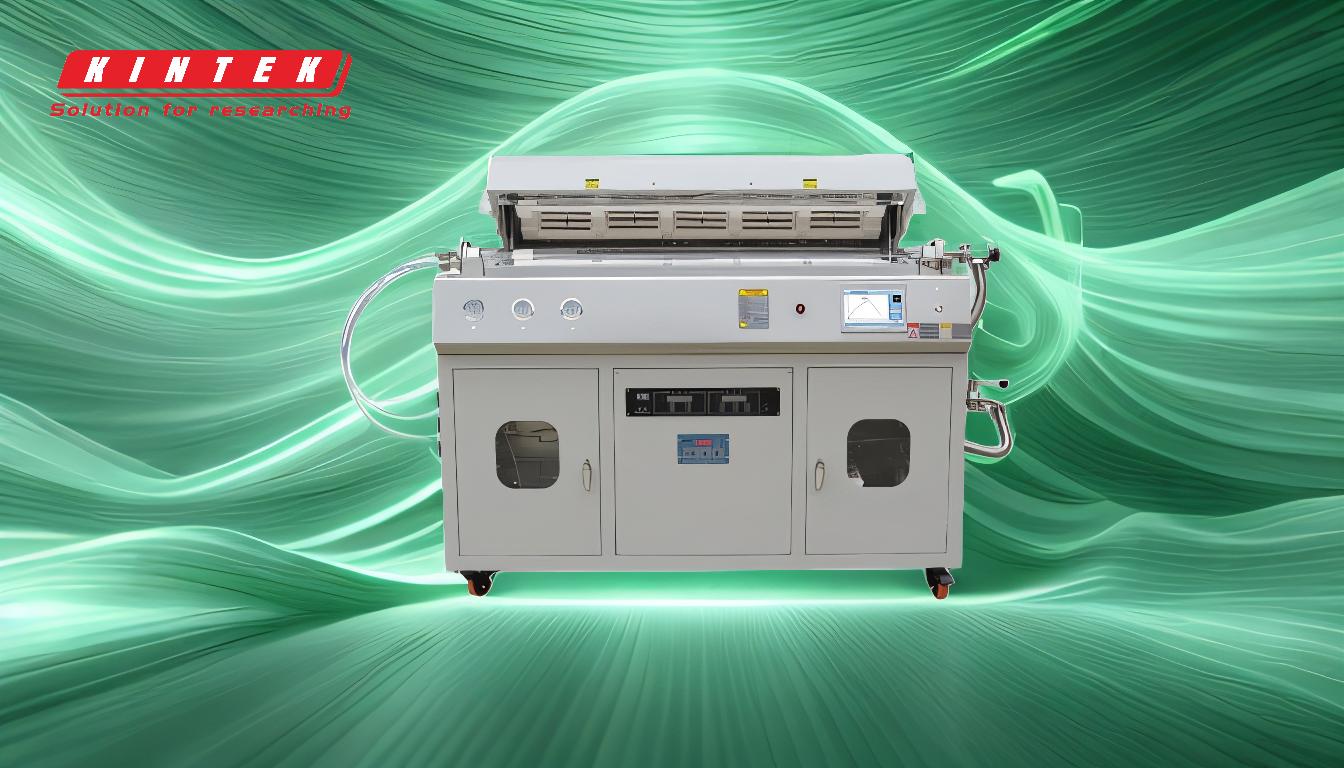
-
Process Mechanism:
- Sputtering: A physical process where energetic ions bombard a target material, dislodging atoms that then deposit onto a substrate. This method does not rely on heat, making it suitable for temperature-sensitive materials.
- CVD: A chemical process involving gaseous precursors that react on the substrate surface to form a solid thin film. This process typically requires higher temperatures and involves chemical reactions.
-
Temperature Requirements:
- Sputtering: Operates at lower temperatures, making it ideal for coating materials like plastics, organics, and glass.
- CVD: Requires higher temperatures, which can limit its use with temperature-sensitive materials but enables the formation of high-quality, uniform films.
-
Deposition Rates:
- Sputtering: Generally has lower deposition rates compared to thermal evaporation but offers precise control over film properties.
- CVD: Can achieve higher deposition rates, especially in processes like thermal CVD, but may involve longer run times due to the chemical reactions involved.
-
Line of Sight and Uniformity:
- Sputtering: Requires a line of sight between the target and substrate, which can limit its ability to coat complex geometries uniformly.
- CVD: Does not require a line of sight, allowing for uniform coating of complex shapes and multiple parts simultaneously.
-
Applications:
- Sputtering: Commonly used for optical coatings, decorative finishes, and functional layers in electronics.
- CVD: Widely used in semiconductor manufacturing, such as creating polycrystalline silicon films for integrated circuits, and in producing high-performance coatings for optical and mechanical applications.
-
Material Utilization and Efficiency:
- Sputtering: Offers high material utilization efficiency, especially in techniques like electron-beam physical vapor deposition (EBPVD).
- CVD: While efficient, it may produce corrosive byproducts and leave impurities in the film, requiring careful handling and post-processing.
-
Advantages and Limitations:
-
Sputtering:
- Advantages: Low-temperature process, precise control over film properties, suitable for temperature-sensitive materials.
- Limitations: Lower deposition rates, requires a line of sight, limited to simpler geometries.
-
CVD:
- Advantages: Uniform coating of complex shapes, high-quality films, no line-of-sight requirement.
- Limitations: Higher temperatures, potential for corrosive byproducts, longer processing times.
-
Sputtering:
By understanding these key differences, equipment and consumable purchasers can make informed decisions about which deposition method best suits their specific application needs.
Summary Table:
Aspect | Sputtering | CVD |
---|---|---|
Process Mechanism | Physical vapor deposition, no heat required | Chemical process, higher temperatures needed |
Temperature | Lower, suitable for sensitive materials | Higher, limits use with sensitive materials |
Deposition Rates | Lower, precise control over film properties | Higher, but longer run times |
Line of Sight | Required, limits complex geometries | Not required, uniform coating of complex shapes |
Applications | Optical coatings, electronics, decorative | Semiconductors, optical, mechanical coatings |
Material Efficiency | High utilization, especially in EBPVD | Efficient but may produce corrosive byproducts |
Advantages | Low-temperature, precise control | Uniform coating, high-quality films |
Limitations | Lower rates, line-of-sight required | Higher temps, potential impurities |
Need help choosing the right thin-film deposition method? Contact our experts today for personalized guidance!