Sputtering and electron beam (e-beam) evaporation are both physical vapor deposition (PVD) techniques used to create thin films, but they differ significantly in their mechanisms, operational conditions, and resulting film properties. Sputtering involves using energized plasma atoms to dislodge atoms from a target material, which then deposit onto a substrate. It operates at lower temperatures, provides better adhesion and coverage for complex substrates, and produces films with smaller grain sizes. E-beam evaporation, on the other hand, uses a focused electron beam to vaporize high-temperature materials, resulting in a higher deposition rate but less uniformity and adhesion. These differences make each method suitable for specific applications depending on the desired film characteristics.
Key Points Explained:
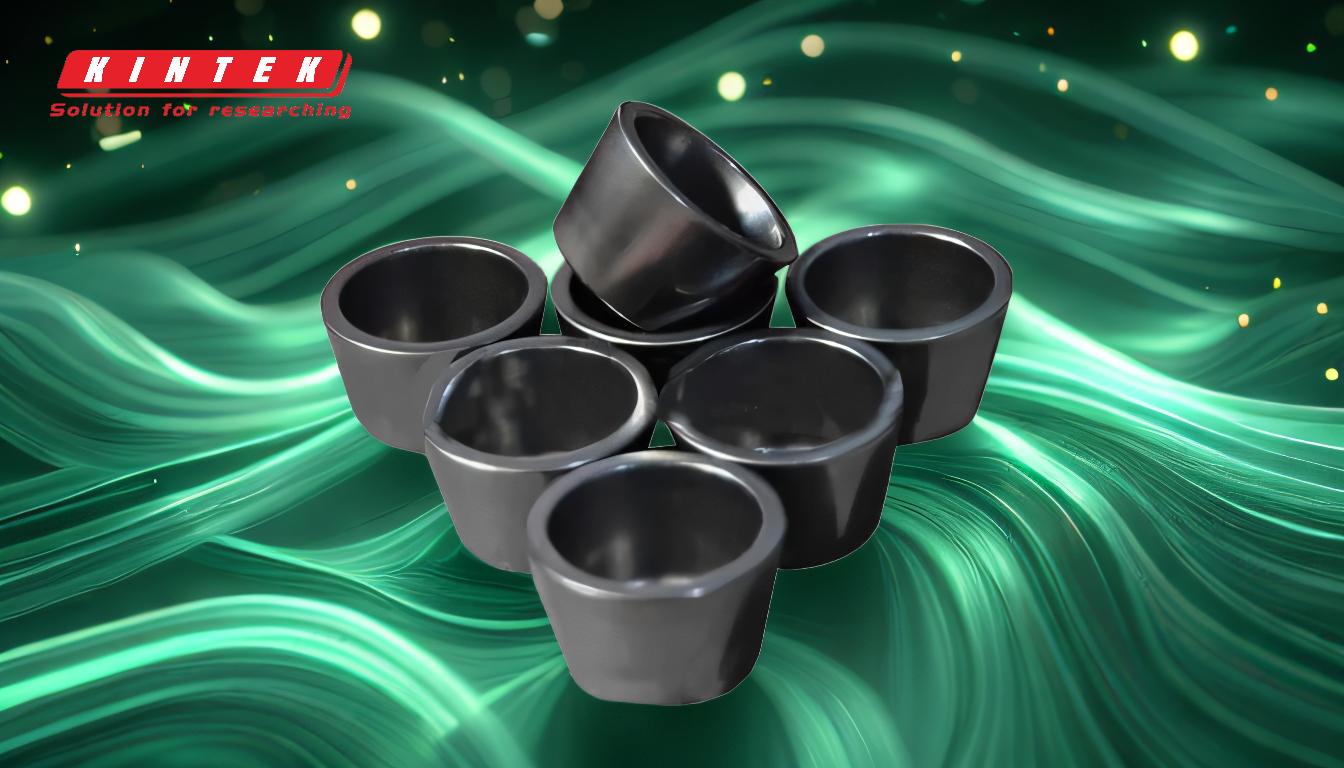
-
Mechanism of Deposition:
- Sputtering: Involves bombarding a target material with energized plasma atoms (typically argon ions) to dislodge atoms, which then deposit onto a substrate. This process does not rely on evaporation and occurs at lower temperatures.
- E-beam Evaporation: Uses a focused electron beam to heat and vaporize a target material, causing it to evaporate and deposit onto a substrate. This is a thermal evaporation process and requires higher temperatures.
-
Vacuum Requirements:
- Sputtering: Operates at relatively lower vacuum levels compared to e-beam evaporation.
- E-beam Evaporation: Requires a high vacuum environment to minimize contamination and ensure efficient vaporization.
-
Deposition Rate:
- Sputtering: Generally has a lower deposition rate, especially for dielectric materials, though it can be higher for pure metals.
- E-beam Evaporation: Offers a higher deposition rate, making it faster for many applications.
-
Adhesion and Coverage:
- Sputtering: Provides better adhesion and more uniform coverage, especially for complex or three-dimensional substrates.
- E-beam Evaporation: Tends to have lower adhesion and less uniform coverage, particularly on complex surfaces.
-
Film Properties:
- Sputtering: Produces films with smaller grain sizes, higher homogeneity, and higher energy of deposited species, leading to denser and more durable films.
- E-beam Evaporation: Results in films with larger grain sizes and less homogeneity, which can affect the mechanical and optical properties of the film.
-
Absorbed Gas and Purity:
- Sputtering: Typically involves higher levels of absorbed gas, which can affect film purity. However, it is capable of producing high-purity thin films with proper control.
- E-beam Evaporation: Absorbs less gas, contributing to higher purity films under optimal conditions.
-
Scalability and Automation:
- Sputtering: Highly scalable and can be easily automated for large-scale production.
- E-beam Evaporation: While it has a high deposition rate, it is less scalable and more challenging to automate compared to sputtering.
-
Applications:
- Sputtering: Ideal for applications requiring high-quality, uniform coatings on complex geometries, such as in semiconductors, optical coatings, and decorative finishes.
- E-beam Evaporation: Suitable for applications needing high deposition rates and high-purity films, such as in metallization for microelectronics and solar cells.
By understanding these differences, equipment and consumable purchasers can make informed decisions about which PVD method best suits their specific application needs, balancing factors like deposition rate, film quality, and scalability.
Summary Table:
Feature | Sputtering | E-beam Evaporation |
---|---|---|
Mechanism | Bombards target with energized plasma atoms | Uses electron beam to vaporize target material |
Temperature | Lower temperatures | Higher temperatures |
Deposition Rate | Lower for dielectrics, higher for metals | Higher |
Adhesion & Coverage | Better adhesion, uniform coverage for complex substrates | Lower adhesion, less uniform coverage |
Film Properties | Smaller grain sizes, higher homogeneity, denser films | Larger grain sizes, less homogeneity |
Purity | Higher absorbed gas, but can achieve high purity | Higher purity due to less absorbed gas |
Scalability | Highly scalable, easily automated | Less scalable, harder to automate |
Applications | Semiconductors, optical coatings, decorative finishes | Metallization, microelectronics, solar cells |
Need help deciding between sputtering and e-beam evaporation? Contact our experts today to find the best PVD solution for your needs!