Pyrolysis is a thermal decomposition process that breaks down organic materials in the absence of oxygen, producing various products such as bio-oil, biochar, and syngas. Thermal pyrolysis and catalytic pyrolysis are two distinct approaches within this process. Thermal pyrolysis relies solely on heat to drive the decomposition, while catalytic pyrolysis incorporates catalysts to enhance reaction rates, lower required temperatures, and improve product yields or quality. The choice between these methods depends on the desired end products, feedstock type, and process efficiency. Catalytic pyrolysis is particularly advantageous for producing higher-quality bio-oils and gases, as the catalysts facilitate more controlled and selective reactions.
Key Points Explained:
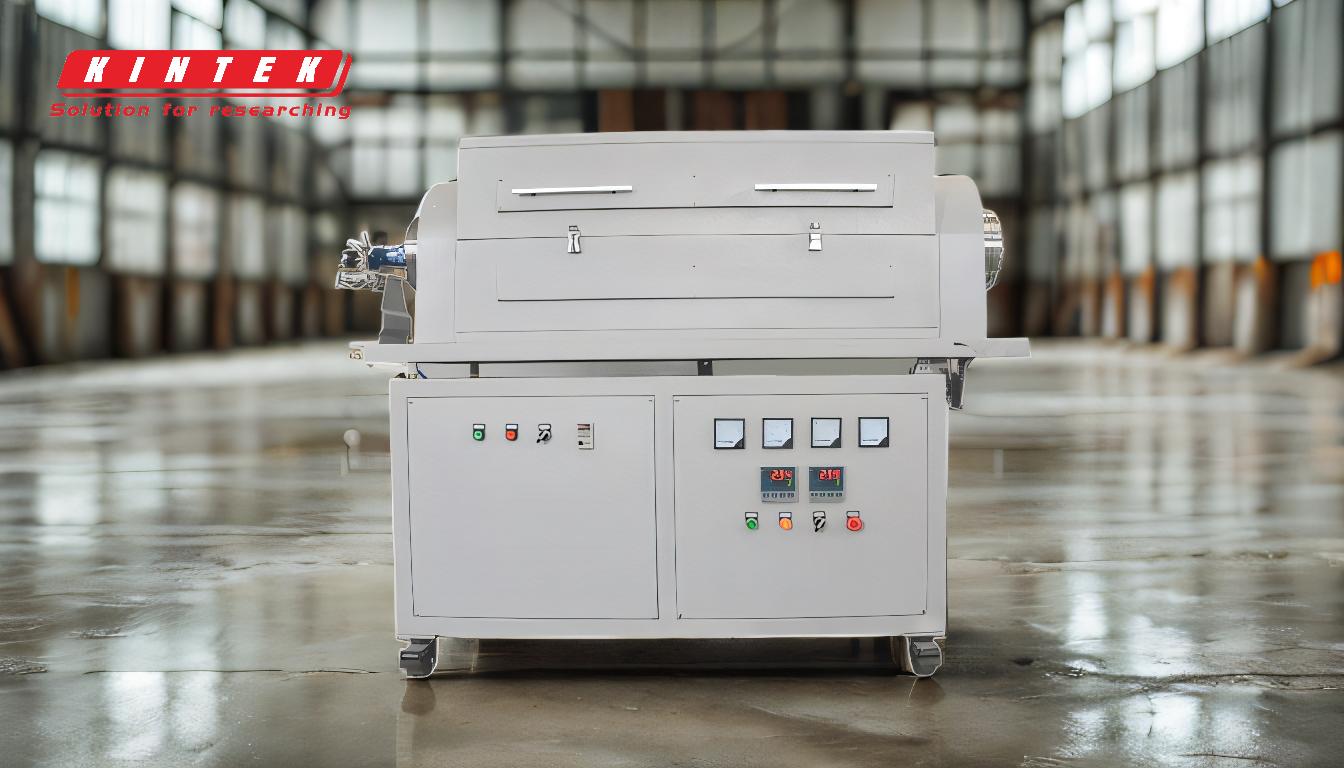
-
Definition and Mechanism:
- Thermal Pyrolysis: This process uses heat alone to decompose organic materials. The feedstock is exposed to high temperatures (typically 400–800°C) in an oxygen-free environment, leading to the breakdown of complex molecules into simpler compounds like bio-oil, biochar, and syngas.
- Catalytic Pyrolysis: In this method, catalysts are introduced to the pyrolysis process. These catalysts can be mixed directly with the feedstock (in-situ) or placed in a separate reactor bed (ex-situ). The catalysts lower the activation energy required for reactions, enabling faster decomposition at lower temperatures and improving the selectivity of the end products.
-
Temperature and Reaction Conditions:
- Thermal Pyrolysis: Operates at higher temperatures, often requiring more energy input. The absence of catalysts means the reaction rates are slower, and the process is less selective, leading to a broader range of products.
- Catalytic Pyrolysis: Typically operates at lower temperatures due to the catalytic effect, which accelerates the reaction. The presence of catalysts also allows for more precise control over the reaction pathways, resulting in higher yields of desired products like bio-oil with reduced oxygen content.
-
Product Yields and Quality:
- Thermal Pyrolysis: Produces a mix of bio-oil, biochar, and syngas. The bio-oil often contains higher levels of oxygenated compounds, making it less stable and lower in energy density. Biochar yield is higher in slow thermal pyrolysis.
- Catalytic Pyrolysis: Enhances the production of high-quality bio-oil with lower oxygen content, making it more suitable for use as a fuel. The process also increases the yield of gases like hydrogen and methane, which are valuable for energy applications. The biochar yield is generally lower compared to thermal pyrolysis.
-
Catalyst Types and Roles:
- Catalysts used in catalytic pyrolysis include zeolites, metal oxides, and alkali metals. These catalysts help in cracking larger hydrocarbon molecules, removing oxygen, and promoting the formation of aromatic compounds. The choice of catalyst depends on the feedstock and desired product profile.
-
Process Complexity and Cost:
- Thermal Pyrolysis: Simpler in design and operation, with lower initial costs. However, it may require more energy and produce lower-quality products, which can increase downstream processing costs.
- Catalytic Pyrolysis: More complex due to the need for catalyst handling, regeneration, and potential deactivation. While the initial setup is costlier, the improved product quality and yields can offset these costs over time.
-
Applications and Suitability:
- Thermal Pyrolysis: Suitable for applications where biochar is the primary product, such as soil amendment or carbon sequestration. It is also used in waste management for converting organic waste into energy.
- Catalytic Pyrolysis: Ideal for applications requiring high-quality bio-oil or syngas, such as renewable fuel production or chemical feedstock generation. It is particularly beneficial for upgrading low-value feedstocks into higher-value products.
-
Environmental and Economic Considerations:
- Thermal Pyrolysis: While it is energy-intensive, it is a well-established technology with relatively low operational risks. The environmental impact depends on the feedstock and the efficiency of the process.
- Catalytic Pyrolysis: Offers environmental benefits by reducing the carbon footprint of the process and producing cleaner fuels. However, the use of catalysts introduces additional environmental considerations, such as catalyst disposal and potential contamination.
In summary, thermal pyrolysis is a straightforward, heat-driven process suitable for producing biochar and syngas, while catalytic pyrolysis leverages catalysts to enhance reaction efficiency, improve product quality, and lower operational temperatures. The choice between the two depends on the specific goals of the pyrolysis process, such as maximizing bio-oil yield or producing high-quality fuels.
Summary Table:
Aspect | Thermal Pyrolysis | Catalytic Pyrolysis |
---|---|---|
Mechanism | Relies solely on heat for decomposition. | Uses catalysts to enhance reaction rates and lower temperatures. |
Temperature | Higher (400–800°C), more energy-intensive. | Lower due to catalytic effect, reducing energy input. |
Product Yields | Mix of bio-oil, biochar, and syngas; bio-oil has higher oxygen content. | Higher-quality bio-oil with lower oxygen content; increased gas yields. |
Catalyst Use | No catalysts used. | Catalysts like zeolites, metal oxides, and alkali metals improve selectivity. |
Process Complexity | Simpler design, lower initial cost. | More complex due to catalyst handling and regeneration. |
Applications | Suitable for biochar production and waste management. | Ideal for high-quality bio-oil and syngas production. |
Environmental Impact | Energy-intensive but low operational risks. | Reduces carbon footprint but involves catalyst disposal considerations. |
Discover the best pyrolysis method for your needs—contact our experts today for tailored solutions!