Thermal evaporation and electron beam (e-beam) evaporation are two widely used techniques in thin-film deposition, each with distinct mechanisms, advantages, and limitations. Thermal evaporation relies on resistive heating to vaporize materials, making it simpler and cost-effective for low-melting-point materials. In contrast, e-beam evaporation uses a focused electron beam to heat materials, enabling the deposition of high-melting-point materials with minimal contamination. While thermal evaporation is suitable for simpler applications, e-beam evaporation offers greater versatility and precision, particularly for refractory materials and high-temperature processes. Below, we explore the key differences between these methods in detail.
Key Points Explained:
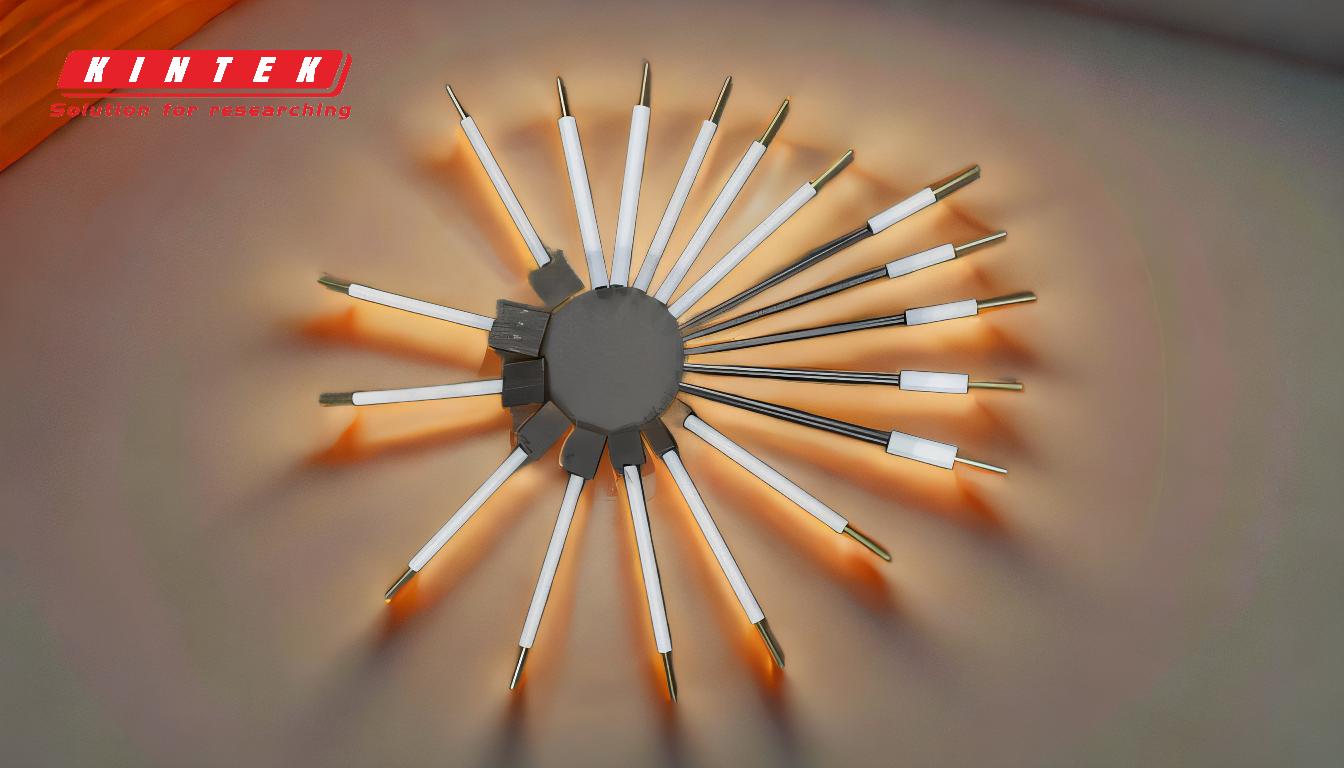
-
Mechanism of Evaporation:
- Thermal Evaporation: This method uses resistive heating to vaporize the target material. A crucible or filament is heated electrically, and the material is evaporated onto the substrate. It is straightforward and cost-effective but limited to materials with lower melting points.
- Electron Beam Evaporation: In this method, a focused electron beam is directed at the target material, generating intense localized heat. This allows the evaporation of materials with extremely high melting points, such as refractory metals, which are beyond the capabilities of thermal evaporation.
-
Material Compatibility:
- Thermal Evaporation: Best suited for materials with relatively low melting points, such as aluminum, gold, and silver. It struggles with high-melting-point materials due to the limitations of resistive heating.
- Electron Beam Evaporation: Highly versatile, capable of evaporating virtually any material, including those with high melting points like tungsten, titanium, and ceramics. This makes it ideal for specialized applications requiring refractory materials.
-
Contamination Levels:
- Thermal Evaporation: May introduce contamination from the crucible or filament, especially at high temperatures. This can affect the purity of the deposited film.
- Electron Beam Evaporation: Produces films with very low contamination levels because the electron beam heats only the target material, minimizing interaction with other components in the system.
-
Deposition Rate and Efficiency:
- Thermal Evaporation: Generally offers a high deposition rate for compatible materials, making it efficient for large-scale production. However, the rate decreases for materials requiring higher temperatures.
- Electron Beam Evaporation: Provides a high deposition rate even for high-melting-point materials, ensuring efficient and precise film formation.
-
Film Quality and Properties:
- Thermal Evaporation: Films may have larger grain sizes and less homogeneity compared to e-beam evaporation. This can impact the mechanical and optical properties of the film.
- Electron Beam Evaporation: Produces films with smaller grain sizes and better homogeneity, resulting in superior mechanical strength, optical clarity, and overall film quality.
-
Operational Complexity and Cost:
- Thermal Evaporation: Simpler and less expensive to set up and operate, making it a popular choice for basic applications. However, it lacks the versatility of e-beam evaporation.
- Electron Beam Evaporation: More complex and costly due to the need for precise electron beam control and high-vacuum environments. However, its ability to handle a wide range of materials justifies the investment for advanced applications.
-
Applications:
- Thermal Evaporation: Commonly used in applications like optical coatings, solar cells, and simple metal depositions where material compatibility and cost are primary concerns.
- Electron Beam Evaporation: Preferred for advanced applications such as semiconductor manufacturing, aerospace coatings, and research requiring high-purity, high-performance films.
In summary, while thermal evaporation is a simpler and more cost-effective method for depositing low-melting-point materials, electron beam evaporation offers unmatched versatility and precision for high-melting-point and refractory materials. The choice between the two depends on the specific requirements of the application, including material properties, film quality, and operational constraints.
Summary Table:
Aspect | Thermal Evaporation | Electron Beam Evaporation |
---|---|---|
Mechanism | Uses resistive heating to vaporize materials. | Uses a focused electron beam to heat materials. |
Material Compatibility | Best for low-melting-point materials (e.g., aluminum, gold). | Capable of evaporating high-melting-point materials (e.g., tungsten, titanium, ceramics). |
Contamination Levels | Higher risk due to crucible or filament interaction. | Minimal contamination; electron beam heats only the target material. |
Deposition Rate | High for compatible materials; decreases for high-melting-point materials. | High for all materials, including high-melting-point ones. |
Film Quality | Larger grain sizes, less homogeneity. | Smaller grain sizes, better homogeneity, and superior mechanical/optical properties. |
Operational Complexity | Simpler and cost-effective. | More complex and expensive due to precise electron beam control and high-vacuum requirements. |
Applications | Optical coatings, solar cells, simple metal depositions. | Semiconductor manufacturing, aerospace coatings, high-purity research applications. |
Need help choosing the right evaporation method for your application? Contact our experts today!