Thermal evaporation and e-beam evaporation are both physical vapor deposition (PVD) techniques used to deposit thin films onto substrates. The primary difference lies in the method of vaporizing the source material. Thermal evaporation uses heat generated by an electric current to melt and evaporate the material, making it suitable for low-melting-point materials. In contrast, e-beam evaporation employs a high-energy electron beam to directly heat and vaporize the material, enabling it to handle high-melting-point materials like oxides. E-beam evaporation offers advantages such as denser coatings, higher deposition rates, and lower impurity risks compared to thermal evaporation. Both methods have distinct applications based on material properties and desired film characteristics.
Key Points Explained:
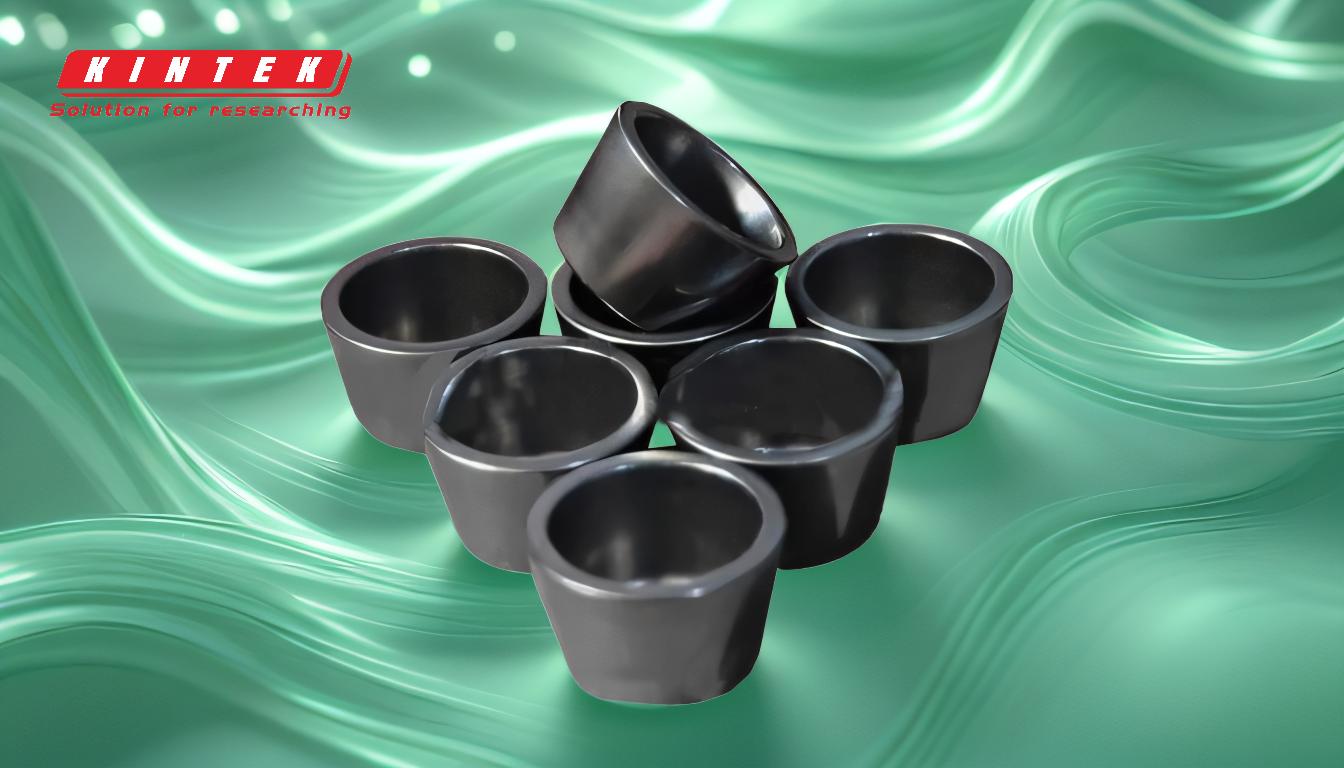
-
Vaporization Method:
- Thermal Evaporation: Uses an electric current to heat a crucible, which melts and evaporates the source material. This method relies on resistive heating and is effective for materials with lower melting points.
- E-beam Evaporation: Utilizes a focused beam of high-energy electrons to directly heat and vaporize the source material. This approach is particularly effective for materials with high melting points, such as oxides, which may not sublimate under thermal evaporation.
-
Material Suitability:
- Thermal Evaporation: Best suited for materials with relatively low melting temperatures, such as aluminum, gold, and silver. It is less effective for high-melting-point materials.
- E-beam Evaporation: Capable of handling high-melting-point materials, including refractory metals and oxides, due to the intense localized heating provided by the electron beam.
-
Deposition Rate:
- Thermal Evaporation: Generally has a lower deposition rate compared to e-beam evaporation, as the heating process is less intense and localized.
- E-beam Evaporation: Offers a higher deposition rate due to the concentrated energy of the electron beam, which rapidly heats and vaporizes the material.
-
Film Quality:
- Thermal Evaporation: Produces films with larger grain sizes and may have lower density, which can affect the mechanical and optical properties of the coating.
- E-beam Evaporation: Results in denser and more homogeneous thin films with smaller grain sizes, leading to improved mechanical strength and better optical properties.
-
Impurity Control:
- Thermal Evaporation: May introduce impurities from the crucible or heating elements, especially if the material reacts with the crucible at high temperatures.
- E-beam Evaporation: Reduces the risk of impurities since the electron beam directly heats the material, minimizing contact with crucibles or other components that could introduce contaminants.
-
Energy Transfer:
- Thermal Evaporation: Relies on thermal conduction to transfer heat from the crucible to the material, which can be less efficient and more prone to uneven heating.
- E-beam Evaporation: Transfers high kinetic energy directly to the material, ensuring efficient and localized heating, which is particularly beneficial for materials that require precise temperature control.
-
Applications:
- Thermal Evaporation: Commonly used in applications where cost and simplicity are prioritized, such as decorative coatings, simple optical films, and certain electronic applications.
- E-beam Evaporation: Preferred for high-performance applications requiring dense, high-quality films, such as advanced optics, semiconductor devices, and coatings for high-temperature environments.
By understanding these key differences, equipment and consumable purchasers can make informed decisions about which method best suits their specific material and application requirements.
Summary Table:
Aspect | Thermal Evaporation | E-beam Evaporation |
---|---|---|
Vaporization Method | Uses electric current for resistive heating of a crucible. | Uses a high-energy electron beam for direct heating. |
Material Suitability | Best for low-melting-point materials (e.g., aluminum, gold, silver). | Ideal for high-melting-point materials (e.g., oxides, refractory metals). |
Deposition Rate | Lower deposition rate due to less intense heating. | Higher deposition rate due to concentrated electron beam energy. |
Film Quality | Larger grain sizes, lower density. | Denser, more homogeneous films with smaller grain sizes. |
Impurity Control | Higher risk of impurities from crucibles or heating elements. | Lower impurity risk due to direct material heating. |
Energy Transfer | Relies on thermal conduction, less efficient. | Direct high-energy transfer for precise and localized heating. |
Applications | Decorative coatings, simple optical films, basic electronics. | Advanced optics, semiconductors, high-temperature coatings. |
Need help selecting the right PVD technique for your application? Contact our experts today for tailored advice!