Thermal evaporation and electron beam (e-beam) evaporation are both physical vapor deposition (PVD) techniques used to deposit thin films onto substrates. The primary difference lies in the method of heating the source material. Thermal evaporation uses electric resistance to heat a crucible, which melts and evaporates the material, making it suitable for lower-melting-point materials. In contrast, e-beam evaporation employs a high-energy electron beam to directly heat and vaporize the material, enabling it to handle high-melting-point materials like oxides. E-beam evaporation also offers denser coatings and higher deposition rates compared to thermal evaporation. Both methods are performed under vacuum conditions but differ in scalability, material compatibility, and film quality.
Key Points Explained:
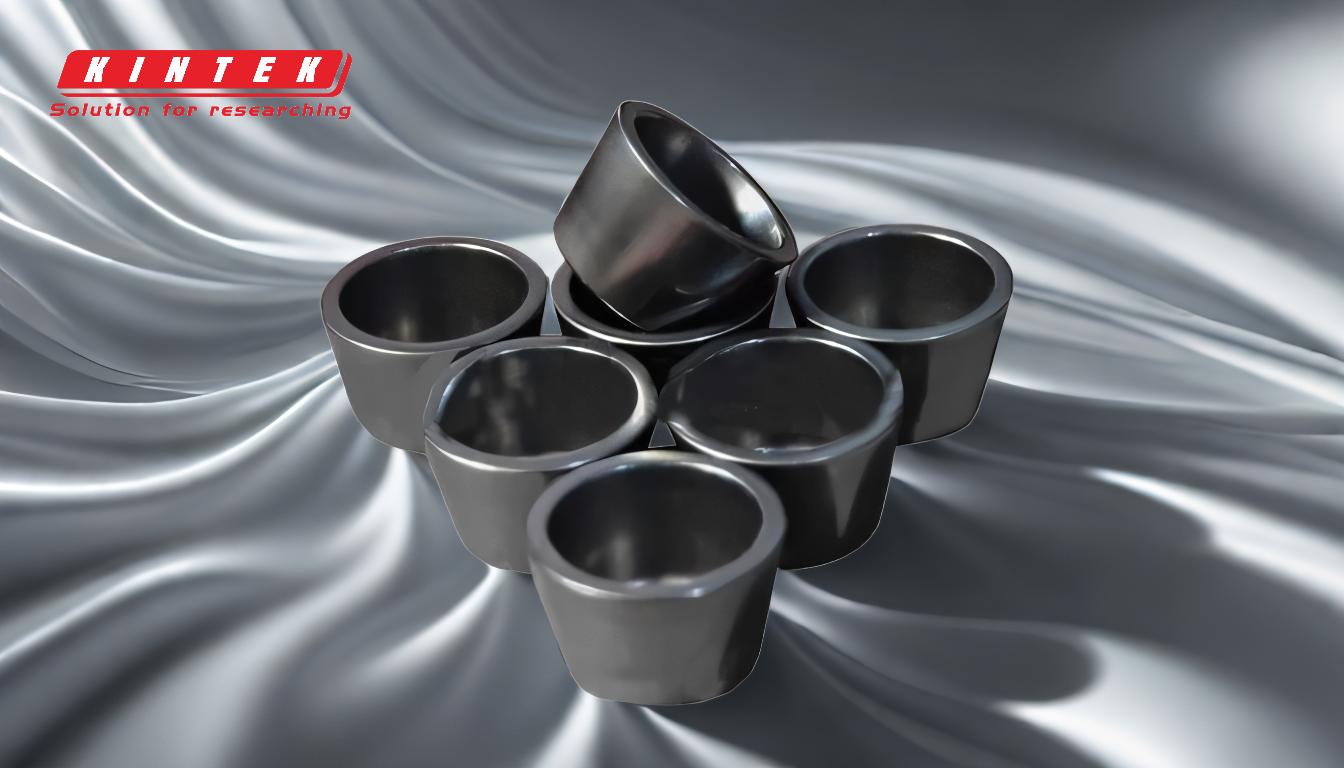
-
Heating Mechanism:
- Thermal Evaporation: Uses electric resistance to heat a crucible, which then melts and evaporates the source material. This method relies on indirect heating.
- E-Beam Evaporation: Utilizes a focused beam of high-energy electrons to directly heat and vaporize the source material. This direct heating method provides higher energy efficiency and precision.
-
Material Compatibility:
- Thermal Evaporation: Best suited for materials with lower melting points, such as aluminum, gold, and silver. It struggles with high-melting-point materials like oxides, which may not sublimate effectively.
- E-Beam Evaporation: Capable of handling high-melting-point materials, including refractory metals and oxides, due to the intense localized heating provided by the electron beam.
-
Film Quality and Deposition Rate:
- Thermal Evaporation: Produces thin films with relatively lower density and purity compared to e-beam evaporation. The deposition rate is generally slower.
- E-Beam Evaporation: Results in denser, higher-purity thin films due to the high-energy process. It also offers a higher deposition rate, making it more efficient for large-scale applications.
-
Scalability and Automation:
- Thermal Evaporation: Less scalable and harder to automate due to its reliance on crucible heating and material limitations.
- E-Beam Evaporation: More scalable and can be automated for industrial applications, especially when dealing with high-melting-point materials or requiring high deposition rates.
-
Operating Environment:
- Both methods operate under vacuum conditions to prevent contamination and ensure efficient material transfer. However, e-beam evaporation requires more sophisticated equipment to generate and control the electron beam.
-
Applications:
- Thermal Evaporation: Commonly used in applications requiring lower-melting-point materials, such as optical coatings, decorative finishes, and some electronic components.
- E-Beam Evaporation: Preferred for advanced applications like semiconductor fabrication, high-temperature superconductors, and wear-resistant coatings due to its ability to handle high-melting-point materials and produce high-quality films.
By understanding these key differences, equipment and consumable purchasers can make informed decisions based on the specific requirements of their applications, such as material type, desired film quality, and production scale.
Summary Table:
Aspect | Thermal Evaporation | E-Beam Evaporation |
---|---|---|
Heating Mechanism | Electric resistance heats a crucible, indirectly melting and evaporating the material. | High-energy electron beam directly heats and vaporizes the material. |
Material Compatibility | Best for lower-melting-point materials (e.g., aluminum, gold). | Handles high-melting-point materials (e.g., oxides, refractory metals). |
Film Quality | Lower density and purity. | Denser, higher-purity films. |
Deposition Rate | Slower deposition rate. | Faster deposition rate, suitable for large-scale applications. |
Scalability | Less scalable and harder to automate. | More scalable and easier to automate for industrial use. |
Applications | Optical coatings, decorative finishes, some electronics. | Semiconductor fabrication, high-temperature superconductors, wear-resistant coatings. |
Still unsure which PVD technique is right for your application? Contact our experts today for personalized guidance!