Thin film coating and thick film coating are two distinct methods of applying layers of material onto a substrate, differing primarily in the thickness of the layers and the techniques used for deposition. Thin film coatings typically range from a fraction of a nanometer to one micron in thickness and involve the deposition of individual atoms or molecules. In contrast, thick film coatings deal with the deposition of particles and result in significantly thicker layers. These differences in thickness and deposition methods lead to variations in applications, properties, and performance characteristics.
Key Points Explained:
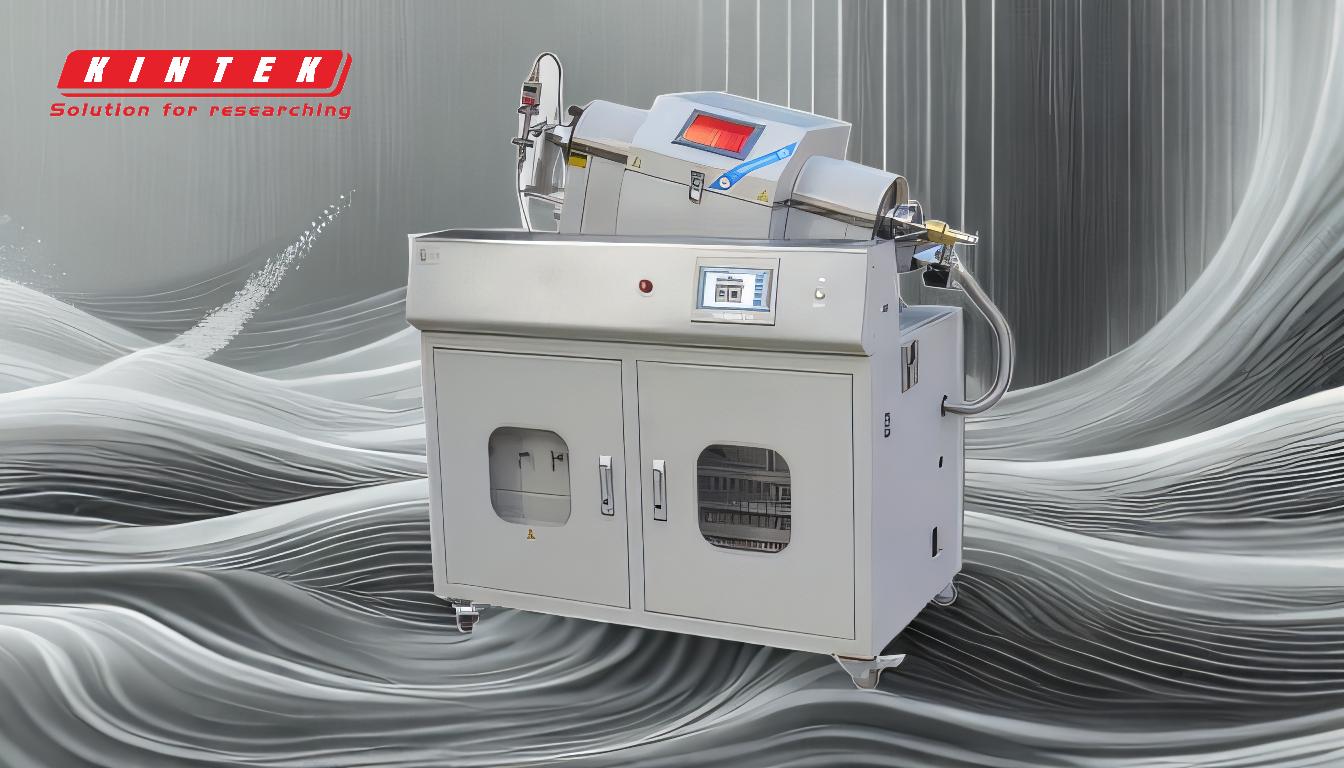
-
Thickness of the Coating:
- Thin Film Coating: The thickness of thin film coatings ranges from a fraction of a nanometer to one micron. This ultra-thin layer is achieved through precise deposition techniques that allow for the controlled placement of individual atoms or molecules onto the substrate.
- Thick Film Coating: Thick film coatings are much thicker, often ranging from several microns to millimeters. These coatings are formed by depositing particles, which can be done using methods like screen printing or spraying.
-
Deposition Techniques:
- Thin Film Coating: Common techniques for thin film deposition include Physical Vapor Deposition (PVD) and Chemical Vapor Deposition (CVD). These methods involve the transfer of material at the atomic or molecular level, allowing for precise control over the film's properties and thickness.
- Thick Film Coating: Thick film coatings are typically applied using techniques such as screen printing, dip coating, or spray coating. These methods involve the deposition of larger particles, resulting in thicker layers that are less uniform compared to thin films.
-
Applications:
- Thin Film Coating: Due to their precise thickness and uniformity, thin film coatings are used in applications where high performance and reliability are critical. Examples include optical coatings, semiconductor devices, and solar cells.
- Thick Film Coating: Thick film coatings are used in applications where durability and robustness are more important than precision. Examples include protective coatings, electronic components like resistors and capacitors, and certain types of sensors.
-
Material Properties:
- Thin Film Coating: Thin films often exhibit unique properties due to their nanoscale thickness, such as enhanced electrical conductivity, optical transparency, and mechanical strength. These properties can be tailored by controlling the deposition process.
- Thick Film Coating: Thick films are generally more robust and less prone to defects due to their thicker, more substantial layers. However, they may lack the precision and uniformity of thin films, which can limit their use in high-performance applications.
-
Performance Characteristics:
- Thin Film Coating: Thin films are known for their high precision and uniformity, making them ideal for applications requiring fine control over material properties. However, they may be more susceptible to damage from environmental factors due to their thinness.
- Thick Film Coating: Thick films offer greater durability and resistance to wear and tear, making them suitable for harsh environments. However, their lack of precision can be a drawback in applications where fine control over material properties is necessary.
In summary, the choice between thin film and thick film coating depends on the specific requirements of the application, including the desired thickness, material properties, and performance characteristics. Thin films are ideal for high-precision applications, while thick films are better suited for durable, robust coatings.
Summary Table:
Aspect | Thin Film Coating | Thick Film Coating |
---|---|---|
Thickness | Fraction of a nanometer to 1 micron | Several microns to millimeters |
Deposition Techniques | Physical Vapor Deposition (PVD), Chemical Vapor Deposition (CVD) | Screen printing, dip coating, spray coating |
Applications | Optical coatings, semiconductors, solar cells | Protective coatings, resistors, capacitors, sensors |
Material Properties | Enhanced conductivity, transparency, mechanical strength | Robust, durable, less uniform |
Performance | High precision, uniformity, susceptible to environmental damage | Durable, resistant to wear, less precise |
Need help choosing the right coating for your application? Contact our experts today!