The dry bag process of isostatic pressing is a specialized powder compaction method used primarily in industries such as cemented carbide, ceramics, and magnetic materials. This process involves loading powders, such as WC–Co, into a flexible rubber mold that is pre-inserted into a pressure vessel. Unlike the wet bag process, the dry bag method keeps the mold permanently inside the pressure vessel, eliminating the need for separate immersion and removal steps. This integration allows for automation, faster production rates, and improved efficiency. The process typically takes 5–10 minutes per cycle and produces green compacts ready for further processing. Safety features like pneumatic/hydraulic controls, blasting valves, and real-time monitoring ensure operational safety and precision.
Key Points Explained:
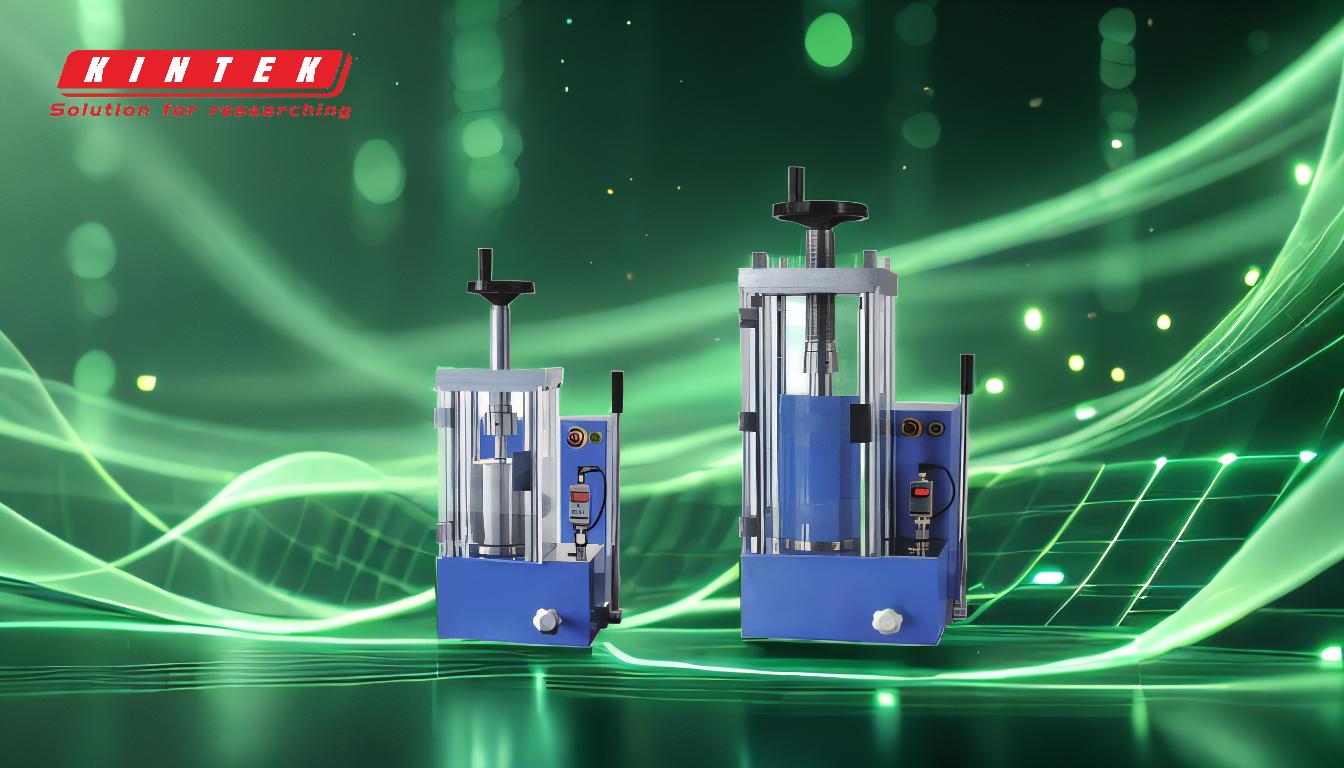
-
Process Overview:
- The dry bag isostatic pressing process involves loading powders, such as WC–Co, into a flexible rubber mold that is pre-inserted into the pressure vessel. This mold remains inside the vessel throughout the process, unlike the wet bag method where the mold is removed after each cycle.
- The powder is either manually or automatically loaded into the mold, which is then sealed and pressurized using a liquid medium. The pressure is applied uniformly, compacting the powder into a solid green compact.
- After compaction, the green compact is removed from the mold and can undergo further processing. This process is highly efficient, with each cycle taking approximately 5–10 minutes.
-
Automation and Efficiency:
- One of the key advantages of the dry bag process is its suitability for automation. The integrated rubber tooling eliminates the need for separate immersion and removal steps, significantly speeding up production rates.
- The process is ideal for industries requiring high-volume production, such as cemented carbide, ceramics, and magnetic materials. The ability to automate loading, pressing, and unloading reduces labor costs and improves consistency.
-
Equipment Features:
- The cold isostatic pressing machine used in the dry bag process is equipped with advanced features to ensure safety and efficiency. These include pneumatic/hydraulic control modes, a safety blasting valve, a manual relief valve, a mechanical pressure gauge, and a high-pressure sensor.
- The machine operates in both automatic and manual modes, with pressing parameters easily set via a touchscreen interface. Password protection ensures that only authorized personnel can adjust settings, enhancing operational security.
-
Safety Mechanisms:
- Safety is a critical aspect of the dry bag isostatic pressing process. The machine includes multiple safety features, such as a safety blasting valve and a manual relief valve, to prevent over-pressurization.
- Real-time monitoring of high-pressure components ensures that any stress or deformation is detected immediately, allowing for timely interventions. This minimizes the risk of accidents and ensures the longevity of the equipment.
-
Forming Agent and Material Compatibility:
- The forming agent used in the dry bag process is typically paraffin, which aids in the compaction of powders and the formation of green compacts.
- The process is compatible with a wide range of materials, including cemented carbides, ceramics, and magnetic materials. This versatility makes it a preferred method for industries requiring precise and uniform compaction.
-
Comparison with Wet Bag Process:
- Unlike the wet bag process, where the mold is removed and immersed in a liquid medium for each cycle, the dry bag process keeps the mold permanently inside the pressure vessel. This eliminates the need for repeated immersion and removal, reducing cycle times and improving efficiency.
- The dry bag process is more suitable for automated production lines, while the wet bag process is often used for custom or low-volume production.
-
Applications:
- The dry bag isostatic pressing process is widely used in industries that require high-density, uniform compacts. Examples include the production of cemented carbide tools, ceramic components, and magnetic materials.
- The ability to produce consistent and high-quality green compacts makes this process essential for applications where material performance and reliability are critical.
By leveraging the dry bag process of isostatic pressing, manufacturers can achieve high levels of automation, efficiency, and safety, making it a valuable technique for modern industrial applications.
Summary Table:
Aspect | Details |
---|---|
Process Overview | Load powders into a rubber mold inside a pressure vessel; no mold removal. |
Cycle Time | 5–10 minutes per cycle. |
Automation | Integrated mold design enables high-speed, automated production. |
Key Applications | Cemented carbide, ceramics, and magnetic materials. |
Safety Features | Pneumatic/hydraulic controls, blasting valves, and real-time monitoring. |
Forming Agent | Paraffin for uniform compaction. |
Comparison to Wet Bag | Faster, more efficient, and better suited for automation. |
Discover how the dry bag isostatic pressing process can revolutionize your production—contact us today for expert guidance!