The deposition rate significantly impacts the properties and performance of thin films. It influences factors such as film thickness, uniformity, adhesion, and structural properties, which are critical for the functionality and reliability of thin films in various applications. A higher deposition rate can lead to faster production but may compromise film quality, while a lower deposition rate can enhance film properties but increase production time. Balancing the deposition rate with other parameters like substrate preparation, temperature, and vacuum conditions is essential for optimizing thin film performance.
Key Points Explained:
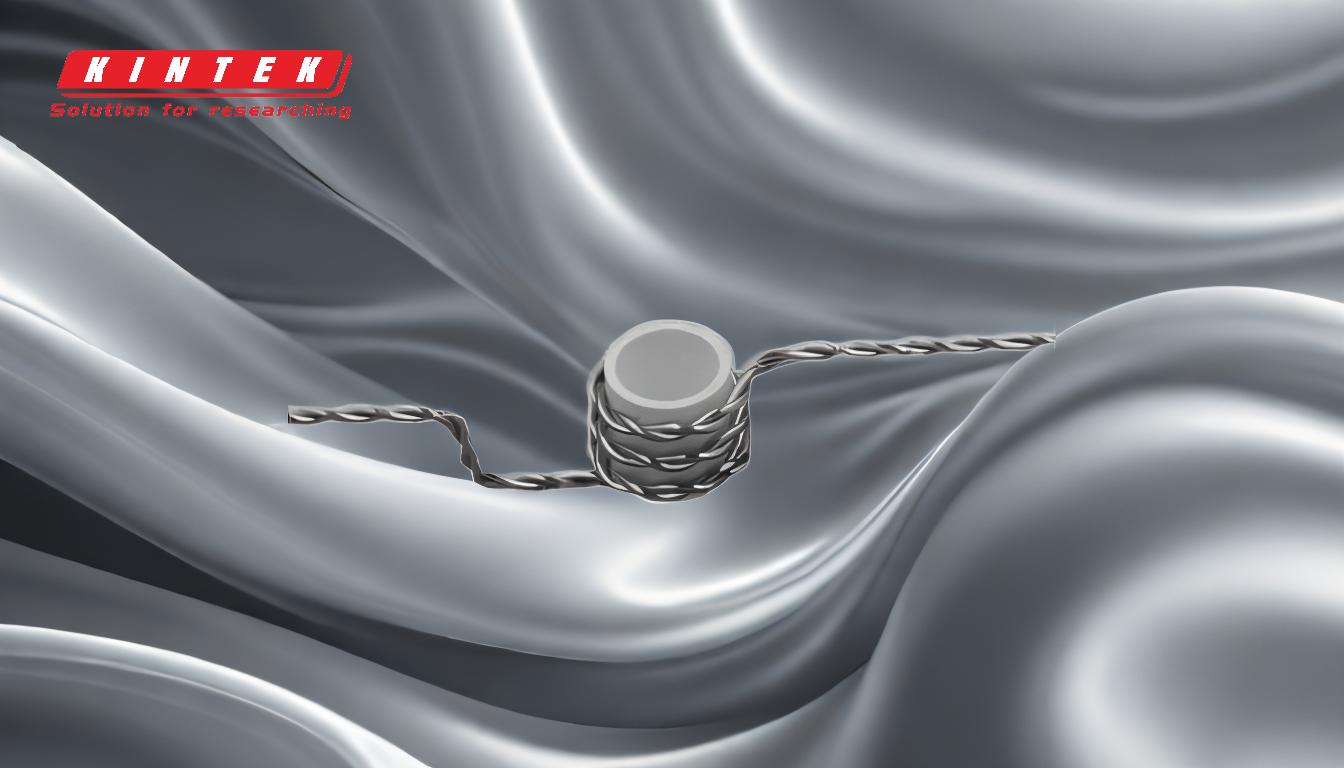
-
Deposition Rate and Film Thickness:
- The deposition rate directly affects the thickness of the thin film. A higher deposition rate results in a thicker film in a shorter time, which can be beneficial for applications requiring rapid production. However, excessively high rates may lead to non-uniform thickness and poor film quality.
- Conversely, a lower deposition rate allows for more controlled growth, resulting in uniform and high-quality films. This is particularly important for applications requiring precise thickness, such as optical coatings or semiconductor devices.
-
Impact on Film Uniformity and Adhesion:
- Deposition rate influences the uniformity of the thin film. High deposition rates can cause uneven film growth, leading to defects such as pinholes or voids. These defects can compromise the film's performance and durability.
- Proper adhesion between the thin film and the substrate is crucial for long-term reliability. The deposition rate affects the interfacial bonding, with slower rates often providing better adhesion due to more controlled growth and reduced stress at the interface.
-
Structural Properties and Defects:
- The rate of deposition affects the microstructure of the thin film. High deposition rates can lead to amorphous or poorly crystalline structures, while slower rates promote the formation of well-defined crystalline structures. This is particularly important for applications requiring specific electrical, optical, or mechanical properties.
- Defects such as grain boundaries, dislocations, and voids are more likely to form at higher deposition rates. These defects can degrade the film's performance, making it essential to balance the deposition rate with other parameters like substrate temperature and vacuum conditions.
-
Deposition Techniques and Rate Control:
- The choice of deposition technique (physical or chemical) influences the achievable deposition rate. Physical vapor deposition (PVD) methods, such as sputtering or evaporation, typically offer higher deposition rates compared to chemical vapor deposition (CVD), which provides better control over film properties.
- Advanced techniques, such as plasma-enhanced CVD or atomic layer deposition (ALD), allow for precise control over the deposition rate, enabling the production of high-quality thin films with tailored properties.
-
Application-Specific Considerations:
- The optimal deposition rate varies depending on the application. For example, flexible solar cells and OLEDs require thin films with specific electrical and optical properties, which may necessitate lower deposition rates to achieve the desired film quality.
- In contrast, industrial coatings or protective layers may prioritize higher deposition rates to meet production demands, even if some compromises in film quality are acceptable.
In summary, the deposition rate is a critical parameter in thin film fabrication, influencing thickness, uniformity, adhesion, and structural properties. Balancing the deposition rate with other process parameters is essential to achieve the desired film performance for specific applications. Advances in deposition techniques and process control continue to expand the possibilities for thin film technology in materials science and nanotechnology.
Summary Table:
Aspect | High Deposition Rate | Low Deposition Rate |
---|---|---|
Film Thickness | Thicker films in less time; may lack uniformity | Uniform, high-quality films with precise control |
Uniformity & Adhesion | Risk of defects like pinholes; weaker adhesion | Better adhesion and reduced stress at interface |
Structural Properties | Amorphous or poorly crystalline structures | Well-defined crystalline structures |
Defects | More grain boundaries, dislocations, and voids | Fewer defects, enhanced performance |
Applications | Industrial coatings, rapid production | Optical coatings, semiconductors, OLEDs |
Need help optimizing your thin film deposition process? Contact our experts today for tailored solutions!