The frequency of an induction furnace significantly impacts its performance, efficiency, and suitability for specific applications. Higher frequencies (up to 400 kHz or more) are ideal for smaller volumes of melts due to the skin depth effect, which ensures shallow penetration and concentrated heating. Lower frequencies (50–60 Hz) are better suited for larger volumes, as they provide deeper penetration and induce turbulence, aiding in uniform melting. The choice of frequency depends on factors such as the material being melted, furnace capacity, desired melting speed, and power configuration. Higher frequencies allow for greater power application and reduced turbulence, while lower frequencies enhance stirring and mixing. Understanding these effects is crucial for optimizing furnace performance and achieving efficient, high-quality melting.
Key Points Explained:
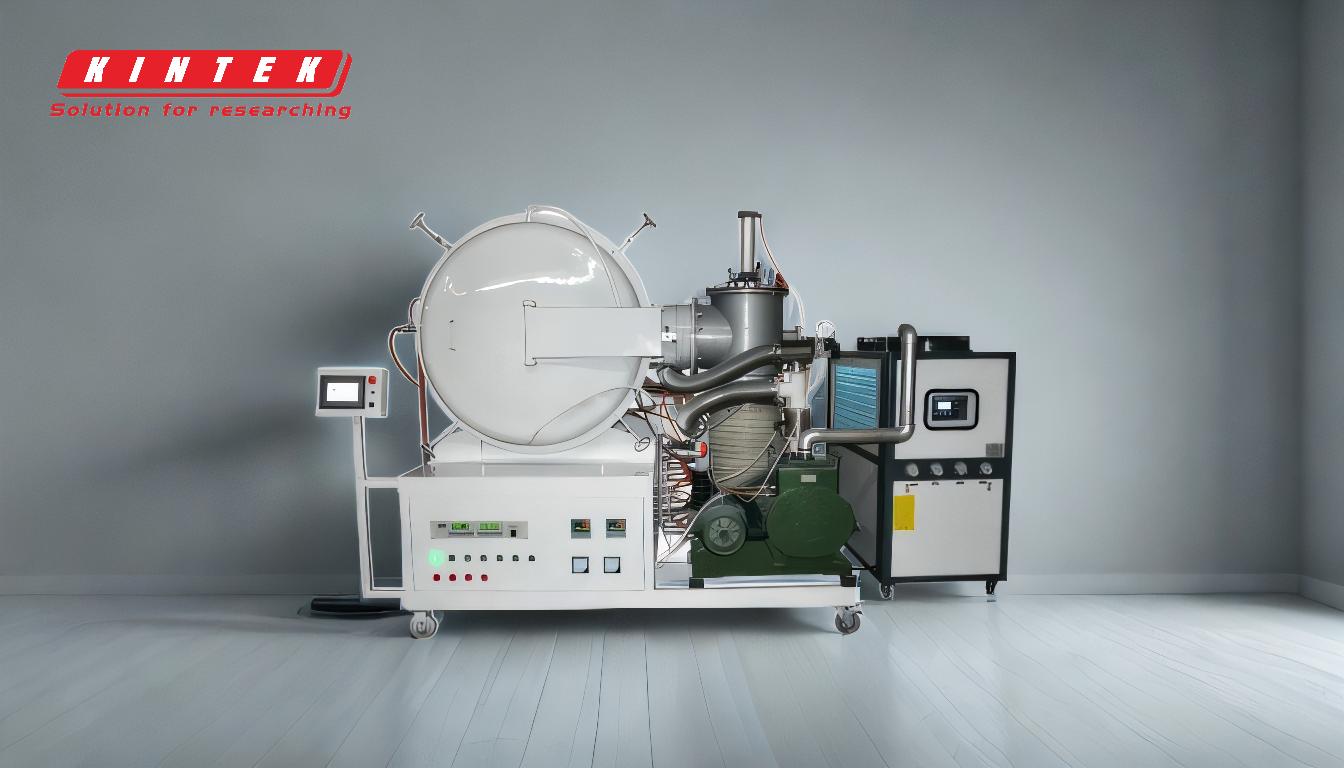
-
Frequency Range and Its Impact on Melting:
- Induction furnaces operate across a wide frequency range, from utility frequencies (50–60 Hz) to high frequencies (up to 400 kHz or higher).
- The frequency chosen depends on the material being melted, the furnace's capacity, and the required melting speed.
- For smaller volumes, higher frequencies are preferred because they result in shallower penetration (skin depth effect), which concentrates heat near the surface and ensures efficient melting.
- For larger volumes, lower frequencies are used as they provide deeper penetration and can induce stirring or turbulence, promoting uniform melting.
-
Skin Depth Effect:
- Skin depth refers to how deeply an alternating current can penetrate a conductor. Higher frequencies result in shallower penetration, while lower frequencies allow deeper penetration.
- This effect is critical in determining the efficiency of heat transfer and the uniformity of melting. For example, when melting small volumes, higher frequencies ensure that heat is concentrated where it is needed most, reducing energy waste.
-
Power Application and Turbulence:
- Higher operating frequencies enable greater power application to a furnace of a given capacity. This is particularly useful for achieving faster melting speeds in smaller furnaces.
- Lower frequencies, while less efficient for small volumes, generate turbulence in the molten metal. This turbulence helps mix the material, ensuring homogeneity and reducing the risk of hotspots or uneven melting.
-
Material-Specific Considerations:
- The type of material being melted influences the choice of frequency. For example, materials with higher electrical conductivity may benefit from higher frequencies to achieve efficient heating.
- The presence of impurities, slags, or oxidants in the material can also affect the melting process, and the frequency must be adjusted accordingly to optimize results.
-
Furnace Capacity and Melting Speed:
- Smaller furnaces or those designed for rapid melting typically operate at higher frequencies to maximize power density and efficiency.
- Larger furnaces, which require deeper penetration and stirring, operate at lower frequencies to ensure uniform heating and mixing.
-
Practical Implications for Equipment Selection:
- When selecting an induction furnace, it is essential to consider the frequency range and its alignment with the intended application. For instance, a high-frequency furnace is ideal for precision melting of small batches, while a low-frequency furnace is better suited for large-scale industrial melting.
- The choice of frequency also impacts the design of the power supply and the refractory materials used in the furnace. High-frequency furnaces may require more advanced power configurations and heat-resistant materials to handle the concentrated heat.
By understanding the effects of frequency on induction furnace performance, users can make informed decisions to optimize melting processes, improve energy efficiency, and achieve high-quality results.
Summary Table:
Aspect | High Frequency (Up to 400 kHz) | Low Frequency (50–60 Hz) |
---|---|---|
Penetration Depth | Shallow (skin depth effect) | Deeper |
Ideal for | Smaller volumes | Larger volumes |
Heat Concentration | Near the surface | Uniform throughout |
Turbulence | Reduced | Enhanced (induces stirring) |
Melting Speed | Faster | Slower |
Power Application | Greater | Lower |
Material Suitability | High-conductivity materials | Large-scale industrial melts |
Ready to optimize your induction furnace performance? Contact our experts today for tailored solutions!