The effect of temperature on pyrolysis products is significant and determines the type and distribution of the resulting materials. Pyrolysis, a thermal decomposition process, yields different products based on the temperature and heating rate. At low temperatures (less than 450°C) with slow heating rates, the primary product is biochar, a carbon-rich solid. At high temperatures (greater than 800°C) with rapid heating rates, the process mainly produces gases, such as syngas. At intermediate temperatures with relatively high heating rates, the dominant product is bio-oil, a liquid mixture of organic compounds. These variations are critical for optimizing pyrolysis processes to achieve desired outputs for specific applications.
Key Points Explained:
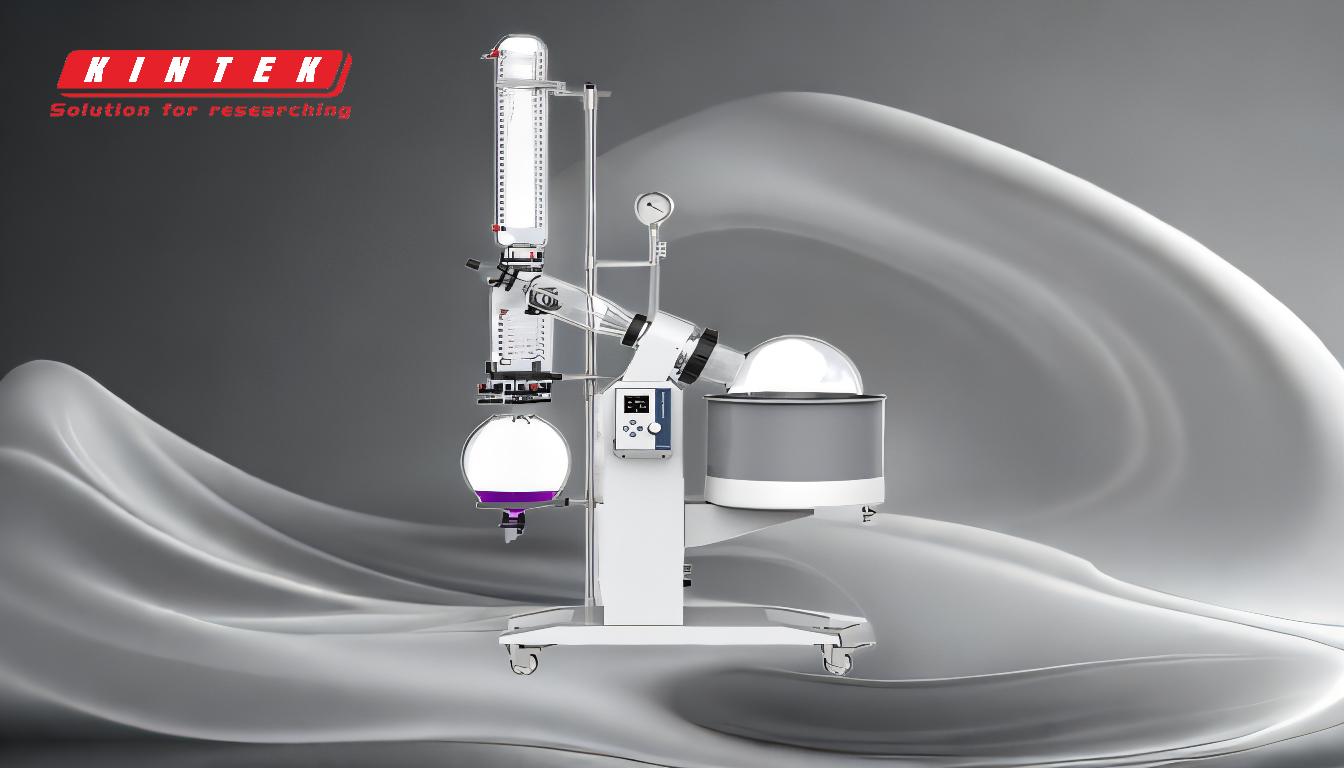
-
Temperature and Heating Rate Influence Product Distribution:
- The temperature and heating rate during pyrolysis are the primary factors determining the type of product formed. Lower temperatures favor solid products like biochar, while higher temperatures favor gaseous products. Intermediate temperatures yield liquid bio-oil.
-
Low-Temperature Pyrolysis (Less Than 450°C):
- Main Product: Biochar.
- Characteristics: Biochar is a carbon-rich solid residue formed under slow heating rates. It is stable, porous, and used in applications like soil amendment, carbon sequestration, and filtration.
- Mechanism: At low temperatures, the biomass undergoes incomplete decomposition, retaining much of its carbon content as a solid residue.
-
High-Temperature Pyrolysis (Greater Than 800°C):
- Main Product: Gases (e.g., syngas).
- Characteristics: Gases produced include hydrogen, methane, carbon monoxide, and carbon dioxide. These are valuable as fuels or chemical feedstocks.
- Mechanism: Rapid heating at high temperatures causes complete breakdown of biomass into smaller molecules, predominantly gaseous compounds.
-
Intermediate-Temperature Pyrolysis:
- Main Product: Bio-oil.
- Characteristics: Bio-oil is a complex liquid mixture of organic compounds, including acids, alcohols, and phenols. It can be used as a fuel or refined into chemicals.
- Mechanism: At intermediate temperatures, biomass decomposes into liquid-phase compounds due to moderate thermal cracking.
-
Applications and Implications:
- Biochar: Used in agriculture for soil improvement, carbon storage, and water filtration.
- Bio-oil: Can be upgraded to transportation fuels or used directly in industrial boilers.
- Gases: Utilized for energy generation or as raw materials in chemical synthesis.
-
Optimization for Desired Products:
- To maximize the yield of a specific product (biochar, bio-oil, or gases), the pyrolysis process must be carefully controlled. Temperature, heating rate, and residence time are key variables that can be adjusted to achieve the desired outcome.
-
Environmental and Economic Considerations:
- The choice of pyrolysis conditions affects not only the product type but also the environmental and economic viability of the process. For example, biochar production is often favored for its carbon sequestration benefits, while bio-oil and gas production are prioritized for energy recovery.
By understanding the relationship between temperature, heating rate, and pyrolysis products, stakeholders can tailor the process to meet specific industrial or environmental goals. This knowledge is particularly valuable for purchasers of pyrolysis equipment and consumables, as it allows them to select systems optimized for their desired outputs.
Summary Table:
Temperature Range | Main Product | Characteristics | Applications |
---|---|---|---|
Low (< 450°C) | Biochar | Carbon-rich, stable, porous | Soil amendment, carbon sequestration, filtration |
Intermediate | Bio-oil | Liquid mixture of organic compounds (acids, alcohols, phenols) | Fuel, chemical refining |
High (> 800°C) | Gases (e.g., syngas) | Hydrogen, methane, carbon monoxide, carbon dioxide | Energy generation, chemical feedstock |
Discover how to optimize pyrolysis for your specific needs—contact our experts today!