The efficiency of an aluminum melting furnace is influenced by several factors, including the type of furnace, its design, operational parameters, and maintenance practices. The efficiency can be measured in terms of thermal efficiency, energy conversion efficiency, and overall operational efficiency. For instance, an intermediate frequency aluminum melting furnace has a thermal efficiency of up to 75%, with specific losses such as frequency conversion loss (3%) and transmission loss (5%). Other factors like furnace capacity, energy type, and operational practices also play a significant role in determining the overall efficiency. Proper control of these factors ensures optimal performance, reduced operating costs, and minimized environmental impact.
Key Points Explained:
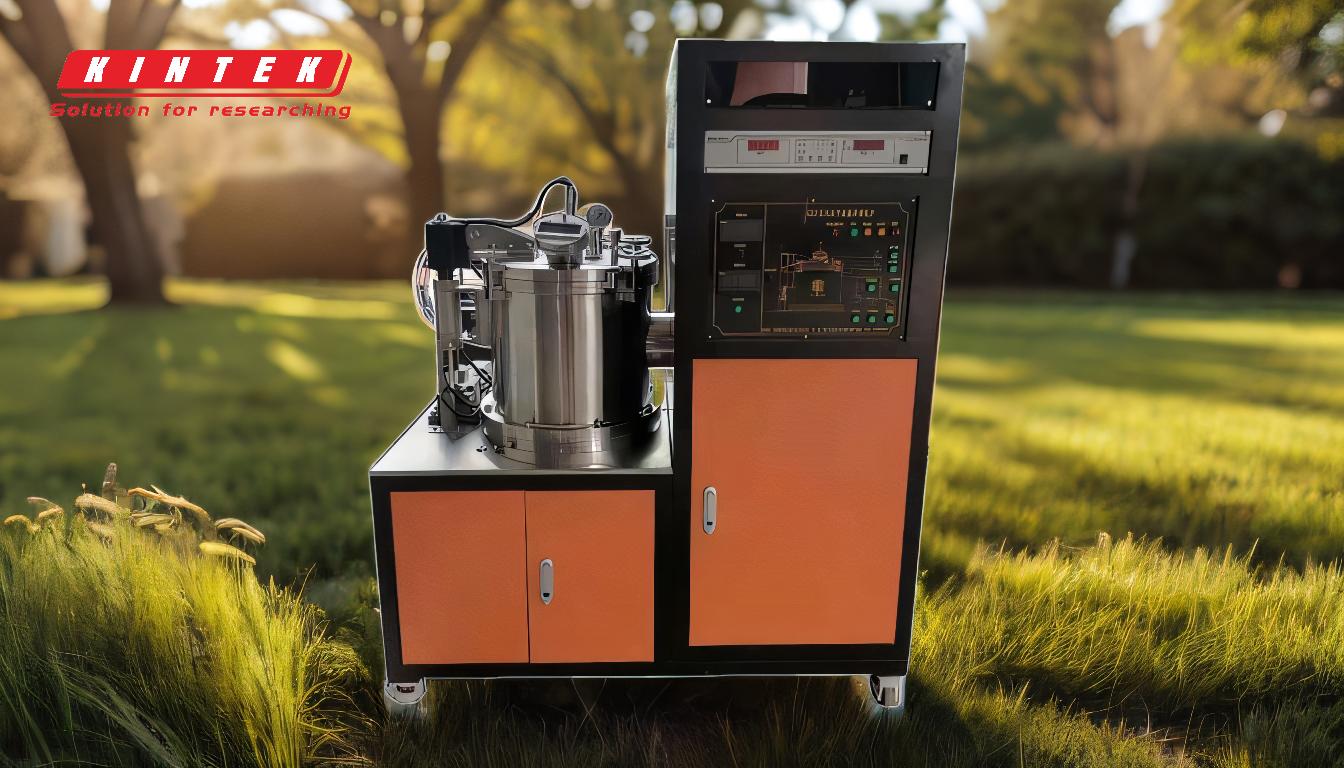
-
Thermal Efficiency of Aluminum Melting Furnaces:
- The thermal efficiency of a furnace refers to how effectively it converts the input energy into heat for melting aluminum. For example, an intermediate frequency aluminum melting furnace has a thermal efficiency of up to 75%. This means that 75% of the input energy is effectively used for melting, while the remaining 25% is lost due to factors like heat dissipation and incomplete combustion.
- Thermal efficiency is influenced by the design of the furnace, the type of insulation used, and the combustion process. For reverberatory furnaces, the air content in the fuel combustion significantly impacts thermal efficiency. Too much air leads to heat loss through exhaust smoke, while too little air causes incomplete combustion and reduced efficiency.
-
Energy Conversion Efficiency:
- Energy conversion efficiency is particularly relevant for electric melting furnaces, where electrical energy is converted into heat energy. The efficiency of this conversion depends on factors such as the quality of insulation materials, furnace design, and control systems. Higher energy efficiency reduces operating costs and minimizes environmental impact.
- For intermediate frequency aluminum melting furnaces, the energy conversion efficiency is 62%, with additional losses such as frequency conversion loss (3%) and transmission loss (5%). These losses are inherent to the system and can be minimized through proper design and maintenance.
-
Operational Factors Affecting Efficiency:
- Furnace Capacity: The capacity of the furnace plays a crucial role in determining its efficiency. Smaller furnaces (5-10 tons) are suitable for small enterprises, while larger furnaces (25+ tons) are more cost-effective for industrial use. Larger furnaces generally have better energy utilization due to economies of scale.
- Energy Type: The type of energy used (natural gas, fuel oil, diesel, or electricity) also affects efficiency. Each energy source has its own efficiency profile, and the choice depends on the specific requirements of the operation.
- Production Delivery Requirements: The production delivery requirements, such as the minimum batch size, can impact efficiency. For example, a minimum batch size of 20 tons is often required, with all metal from the same heat to ensure consistency and efficiency.
-
Maintenance and Service Convenience:
- Regular maintenance is crucial for maintaining the efficiency of an aluminum melting furnace. Dross buildup, which is a byproduct of the melting process, can reduce furnace efficiency and requires periodic cleaning. Service convenience, including ease of access for maintenance, is an important consideration when selecting a furnace.
- Proper operation and maintenance practices, such as controlling the furnace temperature, residence time, and pressure, are essential for optimal performance and safety.
-
Design and Insulation:
- The design of the furnace, including its insulation, plays a significant role in its efficiency. High-quality insulation materials reduce heat loss and improve thermal efficiency. The furnace design should also facilitate effective heat transfer and minimize energy losses.
- Control systems that regulate temperature, pressure, and combustion processes are essential for maintaining high efficiency. Advanced control systems can optimize the melting process and reduce energy consumption.
-
Environmental Impact:
- Higher efficiency not only reduces operating costs but also minimizes the environmental impact of the melting process. Efficient furnaces produce fewer emissions and consume less energy, contributing to a more sustainable operation.
- The choice of energy source also affects the environmental impact. For example, electric furnaces may have a lower carbon footprint compared to those using fossil fuels, depending on the source of the electricity.
In conclusion, the efficiency of an aluminum melting furnace is determined by a combination of factors, including thermal efficiency, energy conversion efficiency, operational practices, and maintenance. Proper control of these factors ensures optimal performance, reduced operating costs, and minimized environmental impact. When selecting a furnace, it is important to consider these factors to achieve the desired efficiency and production goals.
Summary Table:
Factor | Impact on Efficiency |
---|---|
Thermal Efficiency | Up to 75% for intermediate frequency furnaces; influenced by design and insulation. |
Energy Conversion | 62% efficiency with 3% frequency conversion loss and 5% transmission loss. |
Furnace Capacity | Larger furnaces (25+ tons) offer better energy utilization and cost-effectiveness. |
Energy Type | Natural gas, fuel oil, diesel, or electricity affect efficiency based on application. |
Maintenance Practices | Regular cleaning and proper operation ensure sustained efficiency and safety. |
Design & Insulation | High-quality insulation and advanced control systems optimize heat transfer and reduce losses. |
Environmental Impact | Efficient furnaces reduce emissions and energy consumption, supporting sustainability. |
Optimize your aluminum melting furnace efficiency—contact our experts today for tailored solutions!