The efficiency of pyrolysis, a thermal decomposition process that converts organic materials into useful products like gases, liquids, and solids, depends on several factors. These include the composition of the feedstock, reactor design, operational parameters (temperature, pressure, residence time), and the moisture content of the biomass. Proper control of these factors is essential to maximize the conversion of organic materials into energy-dense products and improve overall process efficiency. Additionally, optimizing particle size, heating rate, and reactor conditions can further enhance pyrolysis efficiency.
Key Points Explained:
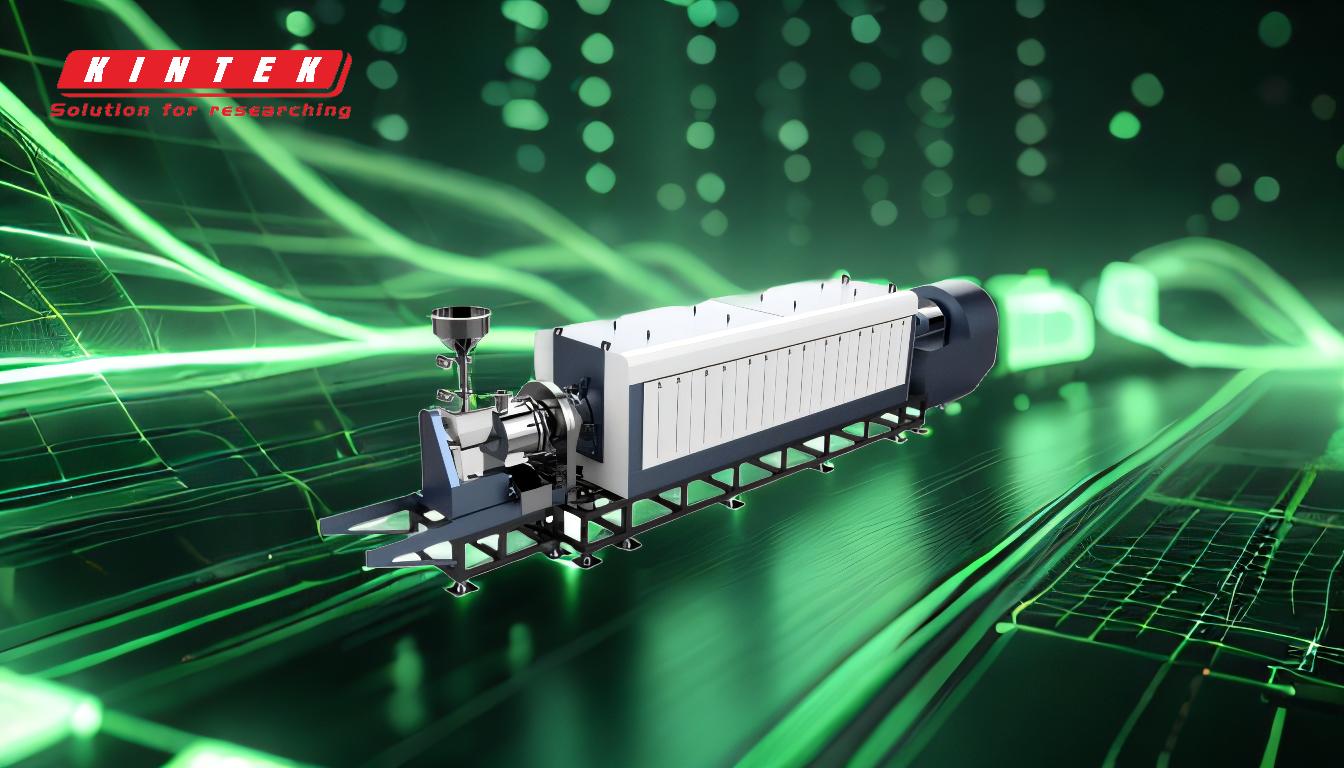
-
Factors Influencing Pyrolysis Efficiency
- Feedstock Composition: The type and composition of the waste or biomass significantly affect pyrolysis efficiency. Organic fractions degrade differently, and their conversion into gases, liquids, or solids depends on their chemical structure.
- Moisture Content: High moisture content in biomass reduces efficiency as energy is wasted in evaporating water instead of degrading organic material. Dry feedstock is preferred for higher efficiency.
- Particle Size: Smaller particle sizes increase the surface area for heat transfer, leading to faster and more uniform pyrolysis reactions.
-
Operational Parameters
- Temperature: Pyrolysis efficiency is highly dependent on temperature. Optimal temperatures vary depending on the feedstock but generally range between 400°C and 800°C. Higher temperatures can improve gas yield but may reduce liquid or solid product yields.
- Residence Time: The time the material spends in the reactor affects the degree of decomposition. Longer residence times allow for more complete conversion but may reduce throughput.
- Pressure: Operating at appropriate pressures ensures efficient heat transfer and product formation. Elevated pressures can enhance certain reactions, but excessive pressure may lead to operational challenges.
-
Reactor Design and Optimization
- Reactor Type: Different reactor designs (e.g., fluidized bed, fixed bed, rotary kiln) have varying efficiencies. The choice of reactor depends on the feedstock and desired end products.
- Heating Rate: A controlled and optimized heating rate ensures efficient decomposition of the feedstock. Rapid heating can lead to higher yields of liquid products, while slower heating favors gas or char production.
- Energy Recovery: Efficient energy recovery systems can improve overall process efficiency by utilizing heat from the pyrolysis process for other operations.
-
Improving Pyrolysis Efficiency
- Optimizing Feedstock Preparation: Pre-treatment methods like drying, shredding, and sorting can enhance feedstock quality and improve pyrolysis efficiency.
- Advanced Control Systems: Implementing automated control systems for temperature, pressure, and residence time ensures consistent and optimal conditions.
- Catalytic Pyrolysis: Using catalysts can lower the required reaction temperatures and improve the yield of specific products, such as bio-oil or syngas.
-
Challenges and Considerations
- Feedstock Variability: Inconsistent feedstock composition can lead to unpredictable pyrolysis outcomes, requiring adaptive operational strategies.
- Energy Input: The energy required to heat the reactor and maintain optimal conditions must be balanced against the energy output from the pyrolysis products.
- Environmental Impact: Efficient pyrolysis minimizes emissions and waste, but improper operation can lead to the release of harmful byproducts.
-
Applications and Benefits
- Energy Production: Pyrolysis converts waste and biomass into energy-dense products like bio-oil, syngas, and biochar, which can be used for electricity generation or as fuel.
- Waste Management: Pyrolysis reduces the volume of waste and converts it into valuable resources, contributing to a circular economy.
- Carbon Sequestration: Biochar produced during pyrolysis can be used to improve soil health and sequester carbon, reducing greenhouse gas emissions.
By understanding and optimizing these factors, the efficiency of pyrolysis can be significantly improved, making it a viable and sustainable solution for waste management and energy production.
Summary Table:
Factor | Impact on Pyrolysis Efficiency |
---|---|
Feedstock Composition | Determines conversion into gases, liquids, or solids based on chemical structure. |
Moisture Content | High moisture reduces efficiency; dry feedstock is preferred. |
Particle Size | Smaller particles increase surface area, improving heat transfer and reaction uniformity. |
Temperature | Optimal range: 400°C–800°C; higher temps favor gas yield, lower temps favor liquids/solids. |
Residence Time | Longer times ensure complete decomposition but may reduce throughput. |
Reactor Type | Choice depends on feedstock and desired products (e.g., fluidized bed, fixed bed, rotary kiln). |
Heating Rate | Controlled rates ensure efficient decomposition; rapid heating favors liquids, slow favors gases. |
Catalytic Pyrolysis | Catalysts lower reaction temps and improve yields of specific products like bio-oil or syngas. |
Optimize your pyrolysis process for maximum efficiency—contact our experts today!