Electron beam (e-beam) evaporation is a highly efficient physical vapor deposition (PVD) technique used to produce thin, high-purity coatings on substrates. The process involves generating an electron beam that heats and evaporates a source material, which then condenses onto a substrate to form a thin film. This method is particularly suitable for materials with high melting points, such as gold, and is widely used in industries requiring precise and high-quality coatings. The process occurs in a vacuum chamber to ensure purity and control over the deposition. Key components include an electron beam gun, crucibles, and quartz crystal microbalances to regulate deposition rates and thickness.
Key Points Explained:
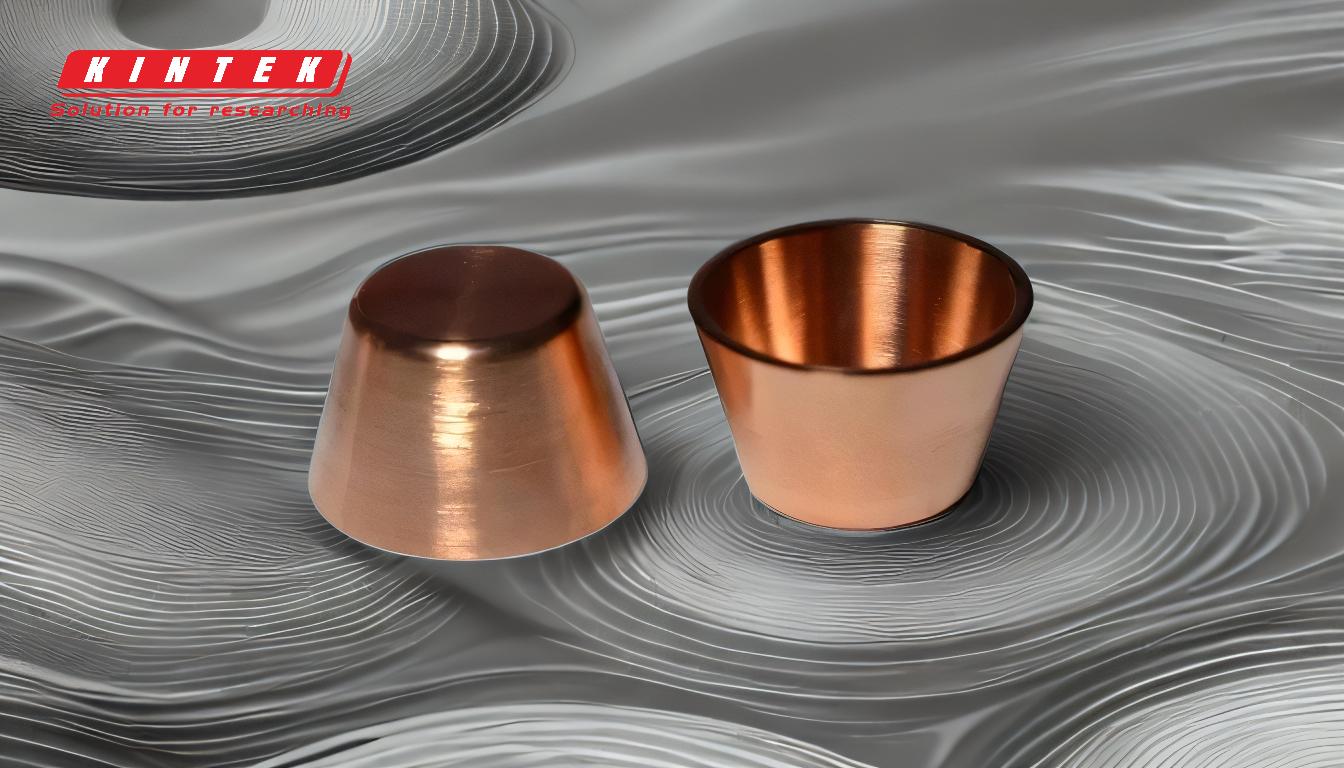
-
Electron Beam Generation:
- The process begins with the generation of an electron beam. A tungsten filament is heated by passing an electric current through it, causing joule heating and electron emission.
- These emitted electrons are accelerated by a high-voltage electric field and directed as a focused beam using magnetic fields.
-
Targeting the Source Material:
- The electron beam is directed towards a crucible containing the source material. The intense energy from the electron beam heats the material, causing it to melt and evaporate.
- The crucible is often water-cooled to prevent contamination and to handle materials with high melting points.
-
Evaporation and Deposition:
- The evaporated material forms a vapor that flows upwards in the vacuum chamber. The substrate, positioned above the crucible, captures these vaporized particles.
- The particles condense on the substrate, forming a thin, high-purity coating. The thickness of the coating typically ranges from 5 to 250 nanometers.
-
Vacuum Environment:
- The entire process occurs in a vacuum chamber to minimize contamination and ensure the purity of the deposited film. The vacuum environment also allows for better control over the deposition process.
-
Control and Regulation:
- Quartz crystal microbalances are used to monitor and regulate the deposition rate and thickness of the coating. This ensures precise control over the final product.
- Multiple crucibles can be used to enable co-deposition and the creation of multi-layer coatings.
-
Applications and Advantages:
- E-beam evaporation is suitable for depositing thin films of metals and alloys, producing films with high purity and good adhesion to the substrate.
- It is particularly advantageous for materials with high melting points and is used in industries requiring high precision and quality, such as electronics, optics, and aerospace.
-
Reactive Deposition:
- Reactive gases like oxygen or nitrogen can be introduced into the vacuum chamber to deposit non-metallic films, such as oxides or nitrides, expanding the range of materials that can be deposited using this method.
-
System Components:
- Key components of an e-beam evaporation system include the electron beam gun, crucibles, vacuum chamber, and quartz crystal microbalances. These components work together to ensure a controlled and efficient deposition process.
By understanding these key points, one can appreciate the precision and versatility of the e-beam evaporation method, making it a valuable technique for producing high-quality thin films in various industrial applications.
Summary Table:
Key Aspect | Details |
---|---|
Process | Electron beam heats and evaporates source material, forming thin films. |
Key Components | Electron beam gun, crucibles, vacuum chamber, quartz crystal microbalances. |
Environment | Vacuum chamber ensures purity and control. |
Applications | Electronics, optics, aerospace, and high-melting-point materials like gold. |
Advantages | High-purity coatings, precise control, and versatility. |
Reactive Deposition | Enables deposition of oxides and nitrides using reactive gases. |
Learn how e-beam evaporation can enhance your thin film processes—contact our experts today!