The evaporation technique for nanoparticles, particularly in the context of carbon nanomaterials, involves methods such as laser ablation, arc-discharge, and chemical vapor deposition (CVD). These techniques are widely used for synthesizing nanoparticles with precise control over size, shape, and composition. Laser ablation uses high-energy laser pulses to vaporize a target material, which then condenses into nanoparticles. Arc-discharge involves creating an electric arc between two electrodes in a gaseous environment, leading to the formation of nanoparticles. CVD, on the other hand, relies on the chemical reaction of gaseous precursors to deposit nanoparticles onto a substrate. Each method has its advantages and is chosen based on the desired properties of the nanoparticles.
Key Points Explained:
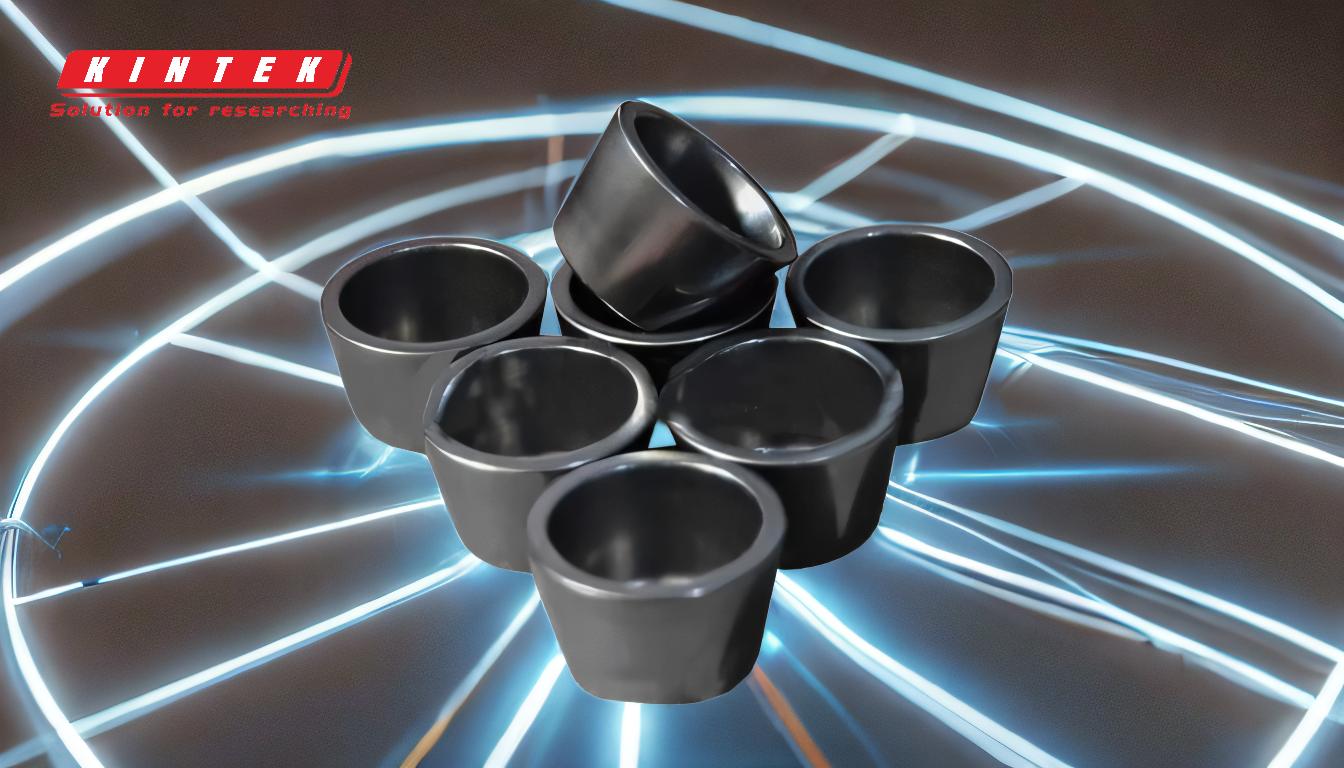
-
Laser Ablation:
- Process: A high-energy laser beam is directed at a target material, causing it to vaporize. The vaporized material then condenses into nanoparticles in a controlled environment.
- Advantages: Allows for precise control over particle size and composition. It is a clean process with minimal contamination.
- Applications: Commonly used for synthesizing metal and semiconductor nanoparticles.
-
Arc-Discharge:
- Process: An electric arc is generated between two electrodes in a gaseous environment (often inert gases like argon or helium). The high temperature of the arc vaporizes the electrode material, which then condenses into nanoparticles.
- Advantages: Produces high-quality nanoparticles with good crystallinity. Suitable for synthesizing carbon-based nanomaterials like fullerenes and carbon nanotubes.
- Applications: Widely used in the production of carbon nanotubes and other carbon-based nanomaterials.
-
Chemical Vapor Deposition (CVD):
- Process: Gaseous precursors are introduced into a reaction chamber, where they undergo a chemical reaction to form nanoparticles. The nanoparticles are then deposited onto a substrate.
- Advantages: Offers excellent control over the size, shape, and composition of nanoparticles. Can be scaled up for industrial production.
- Applications: Used for synthesizing a wide range of nanomaterials, including graphene, carbon nanotubes, and metal oxide nanoparticles.
-
Comparison of Techniques:
- Laser Ablation vs. Arc-Discharge: Laser ablation is more precise and cleaner, but arc-discharge is more cost-effective for large-scale production.
- CVD vs. Other Techniques: CVD provides better control over the deposition process and is more versatile, but it requires more complex equipment and higher operational costs.
-
Selection Criteria:
- Material Type: Different materials may require different synthesis techniques. For example, carbon nanotubes are often synthesized using arc-discharge or CVD.
- Desired Properties: The choice of technique depends on the desired properties of the nanoparticles, such as size, shape, and crystallinity.
- Scale of Production: For large-scale production, techniques like CVD and arc-discharge are more suitable, while laser ablation is better for small-scale, high-precision applications.
By understanding these key points, a purchaser can make informed decisions about which evaporation technique to use based on the specific requirements of their application.
Summary Table:
Technique | Process | Advantages | Applications |
---|---|---|---|
Laser Ablation | High-energy laser vaporizes target material, condensing into nanoparticles. | Precise control over size and composition; clean process with minimal contamination. | Metal and semiconductor nanoparticles. |
Arc-Discharge | Electric arc vaporizes electrode material in a gaseous environment. | High-quality nanoparticles with good crystallinity; cost-effective for large scale. | Carbon nanotubes and fullerenes. |
CVD | Gaseous precursors react to form nanoparticles deposited on a substrate. | Excellent control over size, shape, and composition; scalable for industrial use. | Graphene, carbon nanotubes, and metal oxide nanoparticles. |
Need help selecting the right nanoparticle synthesis technique? Contact our experts today for personalized advice!