Porcelain dental ware undergoes a critical firing process to achieve its desired strength, durability, and aesthetic properties. The firing temperature is a key factor in this process, as it determines the final characteristics of the dental porcelain. Typically, porcelain dental ware is fired at high temperatures, ranging from 900°C to 1400°C, depending on the type of porcelain and the specific application. The firing process involves multiple stages, including bisque firing and glaze firing, each requiring precise temperature control to ensure optimal results. Understanding the firing temperature is essential for dental technicians and professionals to produce high-quality dental restorations.
Key Points Explained:
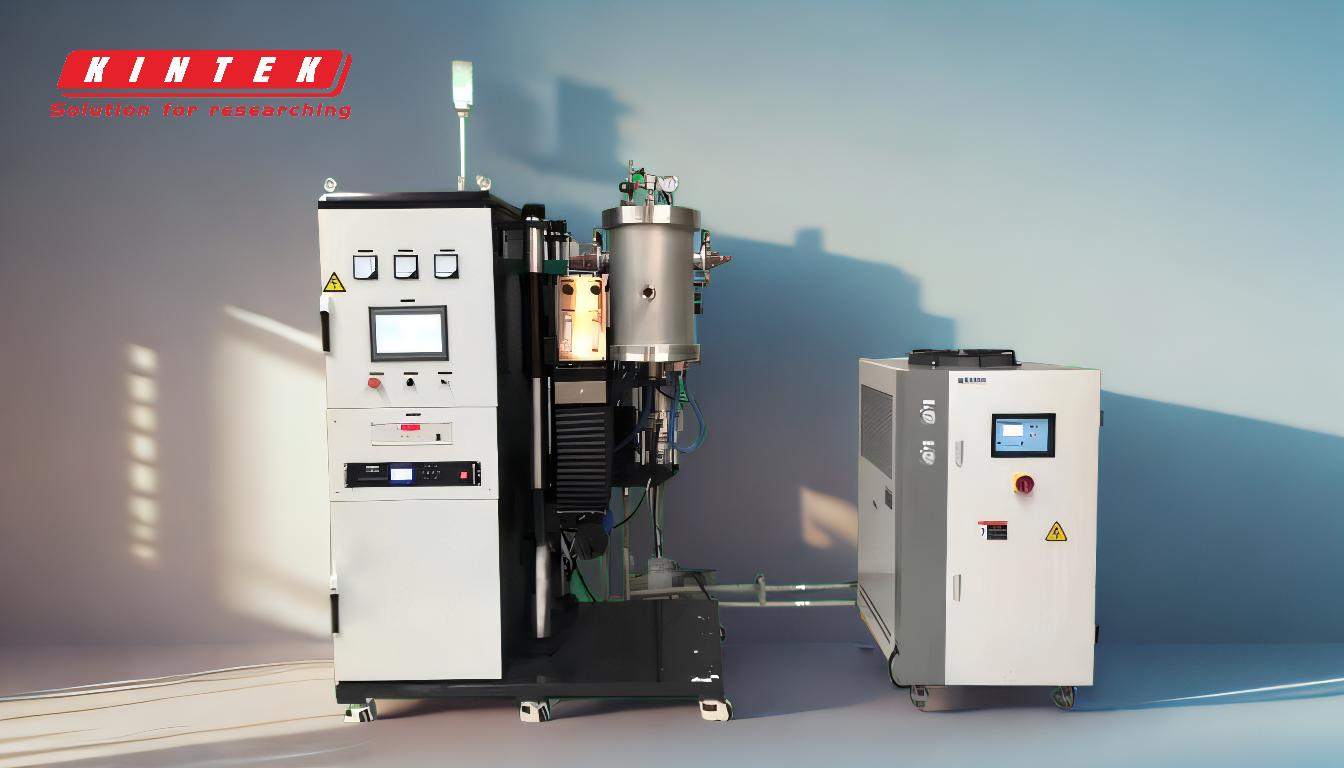
-
Firing Temperature Range for Porcelain Dental Ware:
- Porcelain dental ware is fired at temperatures typically ranging from 900°C to 1400°C. This range varies based on the type of porcelain used and the desired properties of the final product.
- Lower temperatures (around 900°C to 1100°C) are often used for low-fusing porcelains, which are easier to work with and suitable for certain dental applications.
- Higher temperatures (up to 1400°C) are used for high-fusing porcelains, which provide greater strength and durability, making them ideal for dental crowns and bridges.
-
Stages of Firing:
- Bisque Firing: This is the initial firing stage, where the porcelain is heated to a lower temperature (around 900°C to 1000°C) to remove moisture and organic binders. This stage prepares the porcelain for glazing.
- Glaze Firing: After the application of glaze, the porcelain is fired again at a higher temperature (up to 1400°C) to bond the glaze to the surface and achieve the final strength and aesthetic properties.
-
Importance of Temperature Control:
- Precise temperature control is crucial during the firing process to avoid defects such as cracking, warping, or incomplete vitrification.
- Modern dental furnaces are equipped with advanced temperature control systems to ensure consistent and accurate firing temperatures.
-
Types of Porcelain and Their Firing Temperatures:
- Low-Fusing Porcelain: Fired at temperatures between 900°C and 1100°C. These porcelains are often used for veneers and inlays due to their ease of manipulation and lower risk of thermal shock.
- Medium-Fusing Porcelain: Fired at temperatures between 1100°C and 1300°C. These are commonly used for dental crowns and bridges, offering a balance between strength and aesthetics.
- High-Fusing Porcelain: Fired at temperatures up to 1400°C. These porcelains are used for high-strength applications, such as full-coverage crowns and bridges, where durability is paramount.
-
Factors Influencing Firing Temperature:
- Material Composition: The specific composition of the porcelain, including the type of feldspar, silica, and other additives, influences the required firing temperature.
- Desired Properties: The intended use of the dental restoration (e.g., veneer, crown, bridge) determines the optimal firing temperature to achieve the necessary strength and aesthetic qualities.
- Furnace Type: The type of dental furnace used (e.g., conventional, vacuum, or pressable) can affect the firing temperature and process.
-
Impact of Firing Temperature on Final Properties:
- Strength and Durability: Higher firing temperatures generally result in stronger and more durable porcelain, making it suitable for load-bearing restorations.
- Aesthetic Quality: The firing temperature affects the translucency, color, and surface texture of the porcelain, which are critical for achieving a natural appearance in dental restorations.
- Thermal Expansion: Proper firing ensures that the porcelain has the correct thermal expansion properties, reducing the risk of cracking or debonding under temperature changes in the oral environment.
-
Modern Advances in Firing Technology:
- Digital Control Systems: Modern dental furnaces are equipped with digital controls that allow for precise programming of firing cycles, ensuring consistent results.
- Vacuum Firing: Some furnaces use vacuum technology to reduce porosity and improve the density and strength of the fired porcelain.
- Rapid Cooling: Advanced furnaces offer rapid cooling options, which can enhance the mechanical properties of the porcelain by reducing internal stresses.
Understanding the firing temperature of porcelain dental ware is essential for dental professionals to produce high-quality restorations that meet both functional and aesthetic requirements. By carefully controlling the firing process, technicians can ensure that the final product is strong, durable, and visually appealing.
Summary Table:
Aspect | Details |
---|---|
Firing Temperature Range | 900°C to 1400°C, depending on porcelain type and application. |
Low-Fusing Porcelain | 900°C to 1100°C, ideal for veneers and inlays. |
Medium-Fusing Porcelain | 1100°C to 1300°C, used for crowns and bridges. |
High-Fusing Porcelain | Up to 1400°C, suitable for high-strength applications like full-coverage crowns. |
Firing Stages | Bisque Firing (900°C to 1000°C) and Glaze Firing (up to 1400°C). |
Key Factors | Material composition, desired properties, and furnace type. |
Modern Advances | Digital controls, vacuum firing, and rapid cooling enhance results. |
Need expert advice on firing porcelain dental ware? Contact us today for tailored solutions!