Mixing mills, also known as rolling mills, are specialized equipment used in the rubber manufacturing industry to create rubber compounds. Their primary function is to mix a rubber base material with various additives such as fillers, softeners, processing aids, and colorants. This process ensures that the additives are uniformly distributed within the rubber, resulting in a consistent and high-quality final product. The mixing mill operates using two parallel rolls that rotate in opposite directions, with one roll typically moving faster than the other to generate shearing forces. This friction and shearing action facilitate the mixing process, allowing the rubber and additives to blend thoroughly. The final mixture is then shaped and vulcanized to achieve the desired properties for its intended application.
Key Points Explained:
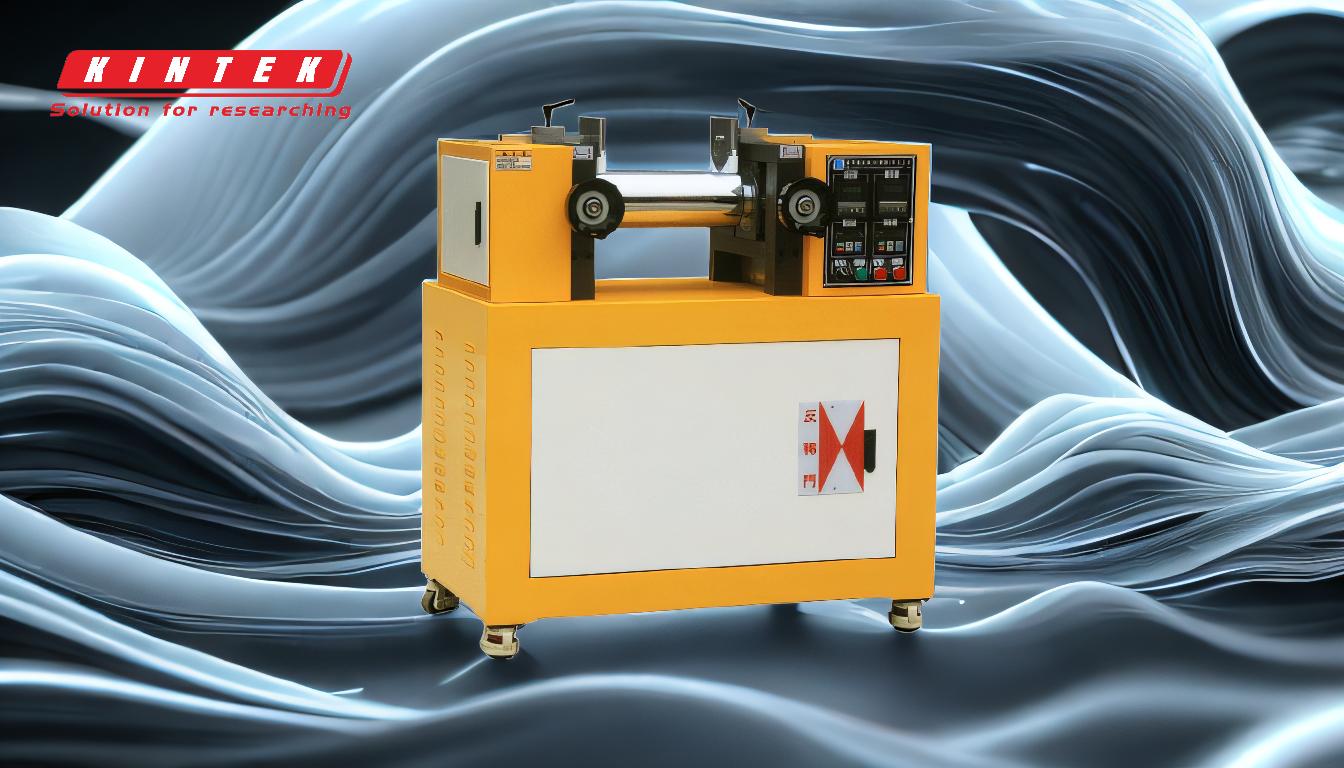
-
Primary Function of Mixing Mills:
- Mixing mills are designed to blend a rubber base material with various additives, including fillers, softeners, processing aids, and colorants. This ensures that the additives are evenly distributed throughout the rubber, which is essential for achieving consistent material properties in the final product.
-
Mechanism of Operation:
- The mixing mill consists of two parallel rolls that rotate in opposite directions. One roll typically rotates faster than the other, creating friction and shearing forces in the nip (the gap between the rolls). These forces are crucial for effectively mixing the rubber and additives.
-
Process of Mixing:
- The process begins by inserting an untreated rubber block into the roll nip. The rubber is pulled into the nip and wraps around the front roll. Additives are then introduced into the nip, and the rubber is repeatedly separated transversely and wound up to ensure thorough mixing. This process is repeated until the additives are fully incorporated into the rubber.
-
Adjustability and Control:
- The width of the roll nip can be adjusted to control the thickness of the rubber layer. Additionally, the speed of the rolls can be set to a specific ratio, with either the front or rear roll rotating faster depending on the mixture requirements. This adjustability allows for precise control over the mixing process.
-
Heat Management:
- During the mixing process, significant heat is generated due to the friction between the rolls and the rubber. To manage this heat, the rolls are often equipped with cooling water circulator systems. This prevents overheating and ensures that the rubber maintains its desired properties during mixing.
-
Final Processing:
- Once the rubber and additives are thoroughly mixed, the final rubber mixture is shaped and vulcanized. Vulcanization is a chemical process that involves heating the rubber with sulfur or other curatives to improve its strength, elasticity, and durability. This step often requires the use of a rubber vulcanizer.
By understanding these key points, a purchaser of mixing mills can appreciate the critical role this equipment plays in the rubber manufacturing process. The ability to uniformly mix additives into rubber and control the mixing process precisely ensures the production of high-quality rubber compounds tailored to specific applications.
Summary Table:
Key Feature | Description |
---|---|
Primary Function | Blends rubber base material with additives for uniform distribution. |
Mechanism of Operation | Uses two parallel rolls rotating in opposite directions to generate shearing forces. |
Process of Mixing | Rubber is repeatedly separated and wound up to ensure thorough mixing. |
Adjustability and Control | Roll nip width and speed ratio can be adjusted for precise mixing control. |
Heat Management | Water cooling systems prevent overheating during the mixing process. |
Final Processing | Mixed rubber is shaped and vulcanized to enhance strength and durability. |
Ready to enhance your rubber manufacturing process? Contact us today to learn more about mixing mills!