The grinding process in ball milling is a critical mechanical operation used to reduce the size of particles, which can vary widely in their physical, mechanical, and chemical properties. This process is essential in industries dealing with materials like ores, minerals, and limestone. Ball milling involves the use of grinding balls within a rotating mill to achieve particle size reduction through mechanisms such as impact, compression, and attrition. The process can be conducted under different conditions, including dry grinding, wet grinding in suspension, or in an inert gas environment, depending on the material properties and desired outcomes.
Key Points Explained:
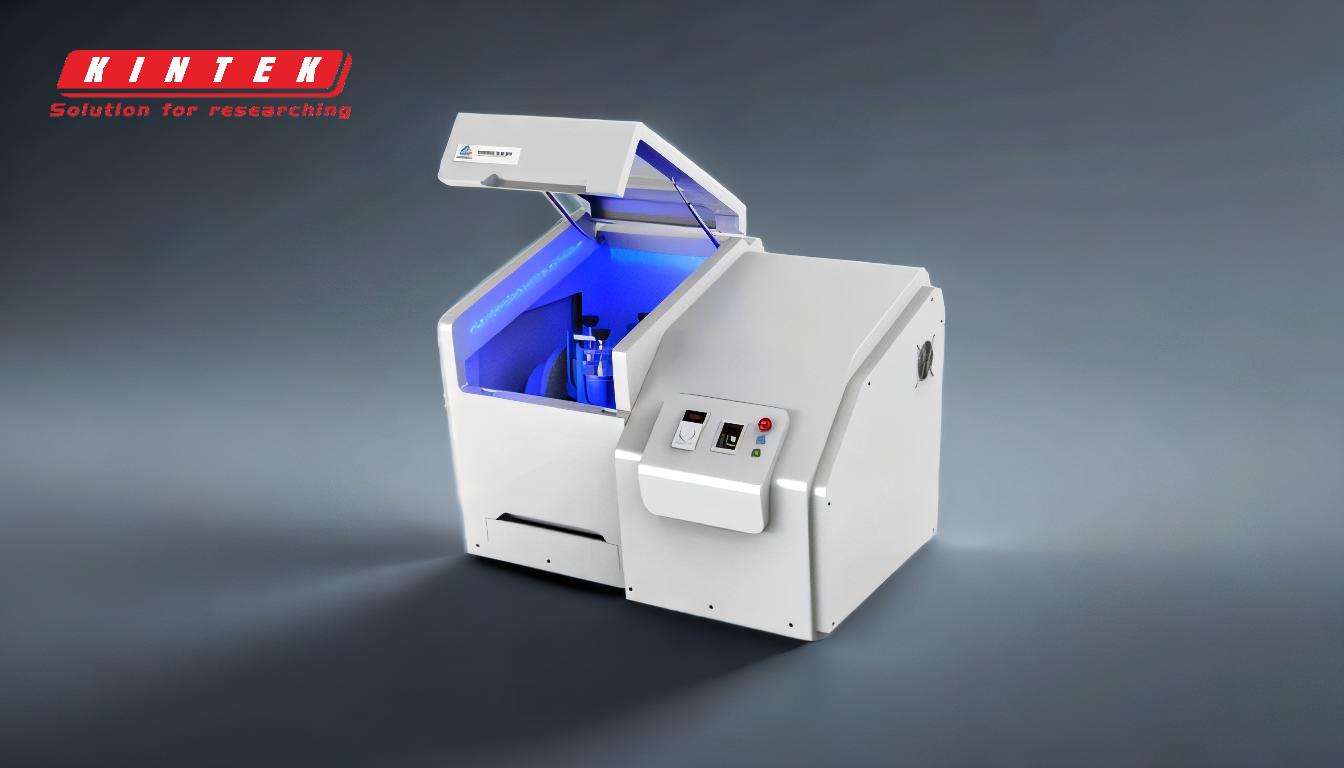
-
Purpose of Ball Milling:
- Particle Size Reduction: The primary goal of ball milling is to reduce the size of particles. This is crucial for various applications, including the preparation of fine powders, enhancing the reactivity of materials, and improving the homogeneity of mixtures.
- Diverse Material Applications: Ball milling is versatile and can be applied to a wide range of materials, from ores and minerals to more complex chemical compounds.
-
Mechanisms of Grinding:
- Impact: The high-energy impact of grinding balls against the material is a primary mechanism. This impact breaks down larger particles into smaller ones.
- Compression: As the grinding balls collide with the material, they also compress it, leading to further size reduction.
- Attrition: The rubbing action between the grinding balls and the material, as well as between the particles themselves, contributes to the grinding process.
-
Types of Ball Mills:
- Planetary Ball Mills: These mills are characterized by their high-energy impact due to the rotation of grinding bowls. They are particularly effective for fine grinding and can operate under different conditions (dry, in suspension, or in inert gas).
- Other Types: While planetary ball mills are highlighted, other types of ball mills, such as tumbling ball mills, also exist and operate on similar principles but with varying energy levels and operational conditions.
-
Process Conditions:
- Dry Grinding: This is the most common form of grinding, where the material is ground without any liquid medium. It is suitable for materials that are not sensitive to moisture.
- Wet Grinding: In this process, the material is ground in a liquid suspension, which can help in reducing dust and improving the efficiency of the grinding process.
- Inert Gas Grinding: For materials that are sensitive to oxidation or moisture, grinding in an inert gas environment is used to prevent unwanted chemical reactions.
-
Particle Dynamics:
- Flattening and Welding: During the grinding process, particles may undergo flattening and welding, which can lead to the formation of layered structures.
- Deformation and Nanoparticle Formation: The intense mechanical forces can cause deformation of these layered structures, and under certain conditions, lead to the formation of nanoparticles.
-
Applications and Outcomes:
- Material Processing: Ball milling is used in the processing of various materials, including the preparation of ceramic powders, metallic powders, and composite materials.
- Enhanced Properties: The grinding process can enhance the physical and chemical properties of materials, such as increasing surface area, improving reactivity, and achieving a more uniform particle size distribution.
By understanding these key points, one can appreciate the complexity and importance of the grinding process in ball milling, and how it is tailored to meet specific industrial and material requirements.
Summary Table:
Key Aspect | Details |
---|---|
Purpose | Particle size reduction, material reactivity enhancement, and homogenization. |
Mechanisms | Impact, compression, and attrition. |
Types of Ball Mills | Planetary ball mills (high-energy), tumbling ball mills, and others. |
Process Conditions | Dry grinding, wet grinding, inert gas grinding. |
Particle Dynamics | Flattening, welding, deformation, and nanoparticle formation. |
Applications | Ceramic powders, metallic powders, composites, and enhanced material properties. |
Discover how ball milling can optimize your material processing—contact us today for expert advice!