The growth rate of Chemical Vapor Deposition (CVD) varies significantly depending on the specific type of CVD process, the materials being deposited, and the operational parameters such as temperature, pressure, and precursor flow rates. Generally, CVD growth rates can range from a few nanometers per minute to several micrometers per hour. For instance, in thermal CVD, growth rates are typically slower, often in the range of 1-10 nm/min, while in techniques like Plasma-Enhanced CVD (PECVD) or microwave plasma chemical vapor deposition, growth rates can be significantly higher due to the enhanced reactivity provided by the plasma. Understanding the factors that influence the growth rate is crucial for optimizing the CVD process for specific applications.
Key Points Explained:
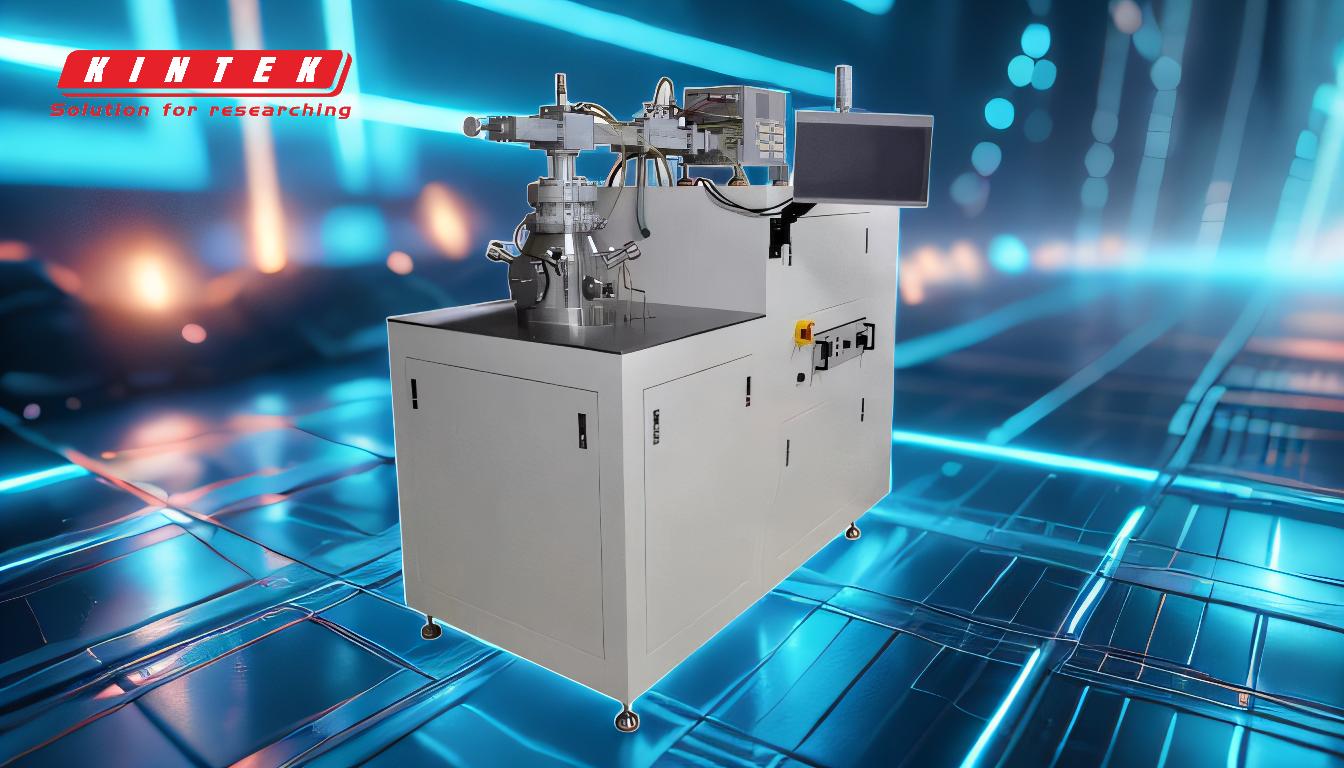
-
Definition of CVD Growth Rate:
- The growth rate in CVD refers to the speed at which a material is deposited onto a substrate. This rate is typically measured in nanometers per minute (nm/min) or micrometers per hour (µm/h). The growth rate is a critical parameter as it directly impacts the thickness and quality of the deposited film.
-
Factors Influencing CVD Growth Rate:
- Temperature: Higher temperatures generally increase the growth rate by enhancing the reaction kinetics. However, excessively high temperatures can lead to undesirable effects such as film cracking or delamination.
- Pressure: The pressure within the CVD chamber can affect the growth rate. Lower pressures often result in faster growth rates due to increased mean free path of the gas molecules, leading to more efficient reactions.
- Precursor Flow Rate: The rate at which precursor gases are introduced into the chamber can significantly influence the growth rate. Optimal flow rates ensure a steady supply of reactants, which is essential for consistent film growth.
- Substrate Material and Surface Condition: The type of substrate and its surface condition can also affect the growth rate. For example, a highly polished substrate may promote faster and more uniform deposition compared to a rough or contaminated surface.
-
Comparison of Growth Rates Across Different CVD Techniques:
- Thermal CVD: Typically has slower growth rates, often in the range of 1-10 nm/min. This is due to the reliance on thermal energy alone to drive the chemical reactions.
- Plasma-Enhanced CVD (PECVD): Offers higher growth rates, often exceeding 100 nm/min, due to the additional energy provided by the plasma, which enhances the reactivity of the precursor gases.
- Microwave Plasma Chemical Vapor Deposition: This technique can achieve even higher growth rates, sometimes up to several micrometers per hour, due to the intense plasma generated by microwave energy, which significantly increases the reaction rates.
-
Applications and Implications of Growth Rate:
- Semiconductor Manufacturing: In the semiconductor industry, precise control over the growth rate is essential for fabricating thin films with specific electrical properties. Faster growth rates can reduce production time but may compromise film quality.
- Optical Coatings: For optical applications, such as anti-reflective coatings, the growth rate must be carefully controlled to achieve the desired optical properties. Faster growth rates can lead to defects that scatter light, reducing the coating's effectiveness.
- Protective Coatings: In applications requiring protective coatings, such as wear-resistant layers, higher growth rates can be beneficial as they allow for thicker coatings to be deposited in a shorter time, enhancing the durability of the coated components.
-
Optimization of Growth Rate:
- Process Parameter Tuning: Adjusting parameters such as temperature, pressure, and precursor flow rates can optimize the growth rate for specific applications. This often involves a trade-off between growth rate and film quality.
- Use of Catalysts: In some cases, the use of catalysts can significantly increase the growth rate by lowering the activation energy required for the chemical reactions.
- Advanced Techniques: Techniques such as Atomic Layer Deposition (ALD) offer precise control over growth rates, allowing for the deposition of ultra-thin films with atomic-level precision, albeit at slower growth rates compared to traditional CVD.
In summary, the growth rate of CVD is a complex parameter influenced by various factors, and it varies widely depending on the specific CVD technique and application. Understanding and optimizing these factors is crucial for achieving the desired film properties and production efficiency.
Summary Table:
Aspect | Details |
---|---|
Growth Rate Range | 1-10 nm/min (Thermal CVD) to several µm/hour (Microwave Plasma CVD) |
Key Influencing Factors | Temperature, Pressure, Precursor Flow Rate, Substrate Material |
CVD Techniques | Thermal CVD, Plasma-Enhanced CVD (PECVD), Microwave Plasma CVD |
Applications | Semiconductor Manufacturing, Optical Coatings, Protective Coatings |
Optimization Strategies | Parameter Tuning, Use of Catalysts, Advanced Techniques (e.g., ALD) |
Need help optimizing your CVD process? Contact our experts today!