Diamond-like carbon (DLC) coatings are known for their exceptional hardness, which is one of their most notable properties. The hardness of DLC coatings typically ranges between 1500 HV (Vickers hardness) and 4500 HV, with some specialized DLC coatings reaching up to 9000 HV. This high hardness is due to the presence of Sp3 (diamond-like) carbon bonds, which provide a structure similar to that of diamond. The hardness of DLC coatings can vary depending on factors such as the deposition process, substrate properties, and the specific composition of the coating. These coatings are widely used in applications requiring wear resistance, low friction, and durability, such as in automotive components, cutting tools, and medical devices.
Key Points Explained:
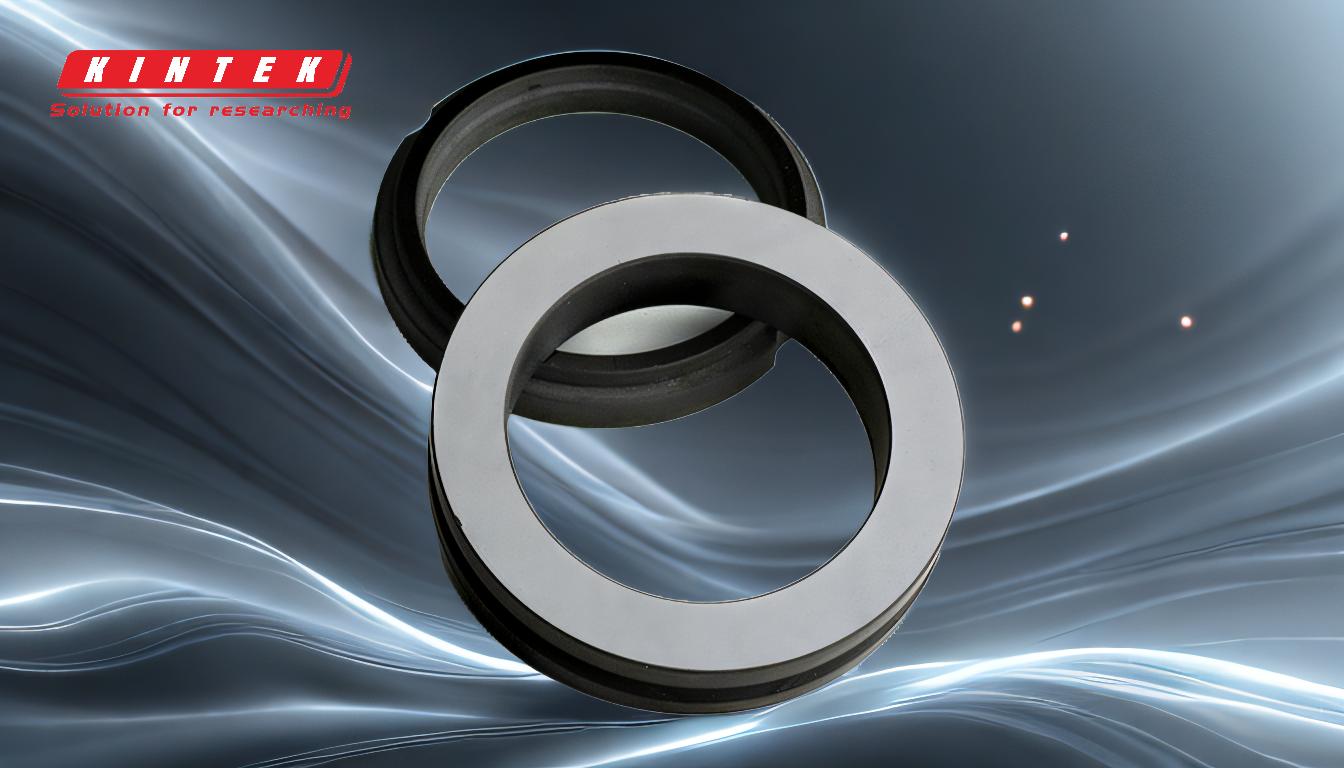
-
Hardness Range of DLC Coatings:
- DLC coatings typically exhibit a hardness range of 1500 HV to 4500 HV, with some advanced coatings reaching up to 9000 HV.
- This hardness is comparable to that of diamond, making DLC coatings highly resistant to wear and abrasion.
-
Factors Influencing Hardness:
- Deposition Process: The method used to deposit the DLC coating (e.g., PVD, CVD) significantly affects its hardness. For example, PVD coatings can vary in hardness based on the operator's skill and the specific parameters used during deposition.
- Substrate Properties: The hardness of the DLC coating can also be influenced by the properties of the substrate material, such as its surface roughness and composition.
- Coating Composition: The ratio of Sp3 (diamond-like) to Sp2 (graphite-like) carbon bonds in the coating plays a crucial role in determining its hardness. Higher Sp3 content generally results in greater hardness.
-
Applications of High-Hardness DLC Coatings:
- Wear Protection: Due to their high hardness, DLC coatings are widely used in applications requiring wear resistance, such as in automotive engine components, cutting tools, and industrial machinery.
- Low Friction: The combination of high hardness and low coefficient of friction makes DLC coatings ideal for reducing wear and improving the lifespan of moving parts.
- Corrosion Resistance: DLC coatings are also used in environments where resistance to chemical corrosion is essential, such as in medical implants and optical sensors.
-
Comparison with Other Coatings:
- Diamond Coatings: While diamond coatings also exhibit high hardness and excellent thermal conductivity, DLC coatings offer additional advantages such as better adhesion to various substrates and the ability to be deposited at lower temperatures.
- Other PVD Coatings: Compared to other PVD coatings, DLC coatings generally have a higher hardness and better performance in terms of wear resistance and friction reduction.
-
Tailoring DLC Coating Properties:
- The hardness and other properties of DLC coatings can be tailored by adjusting deposition parameters such as gas phase composition, temperature, and pressure. This allows for customization of the coating to meet specific application requirements.
- For example, increasing the Sp3 content in the coating can enhance hardness, while optimizing the deposition process can improve adhesion and reduce surface roughness.
-
Benefits Beyond Hardness:
- Chemical Inertness: DLC coatings are chemically inert, making them suitable for use in corrosive environments.
- Biocompatibility: The biocompatibility of DLC coatings makes them ideal for medical applications, such as coatings for surgical instruments and implants.
- Optical Properties: DLC coatings are also used in optical applications due to their ability to precisely control thickness and refractive index, making them suitable for antireflective coatings and optical sensors.
In summary, the hardness of DLC coatings is one of their most significant attributes, making them highly valuable in a wide range of industrial and commercial applications. The ability to tailor their properties through careful control of the deposition process further enhances their versatility and effectiveness.
Summary Table:
Aspect | Details |
---|---|
Hardness Range | 1500–4500 HV (up to 9000 HV for specialized coatings) |
Key Factors | Deposition process, substrate properties, Sp3/Sp2 carbon bond ratio |
Applications | Automotive components, cutting tools, medical devices, optical sensors |
Benefits Beyond Hardness | Chemical inertness, biocompatibility, optical properties |
Comparison | Higher hardness and better wear resistance than other PVD coatings |
Ready to enhance your products with DLC coatings? Contact us today for expert advice!