The history of the Chemical Vapor Deposition (CVD) process is deeply intertwined with advancements in materials science and industrial applications. While the provided references focus on short path vacuum distillation, the principles of vacuum systems and precise control over processes are relevant to understanding the evolution of CVD. CVD emerged as a critical technique for depositing thin films and coatings, particularly in semiconductor manufacturing, where the need for high-purity materials and controlled environments is paramount. The development of CVD was driven by the demand for efficient, scalable, and precise methods to create advanced materials, often leveraging vacuum technology to achieve optimal results.
Key Points Explained:
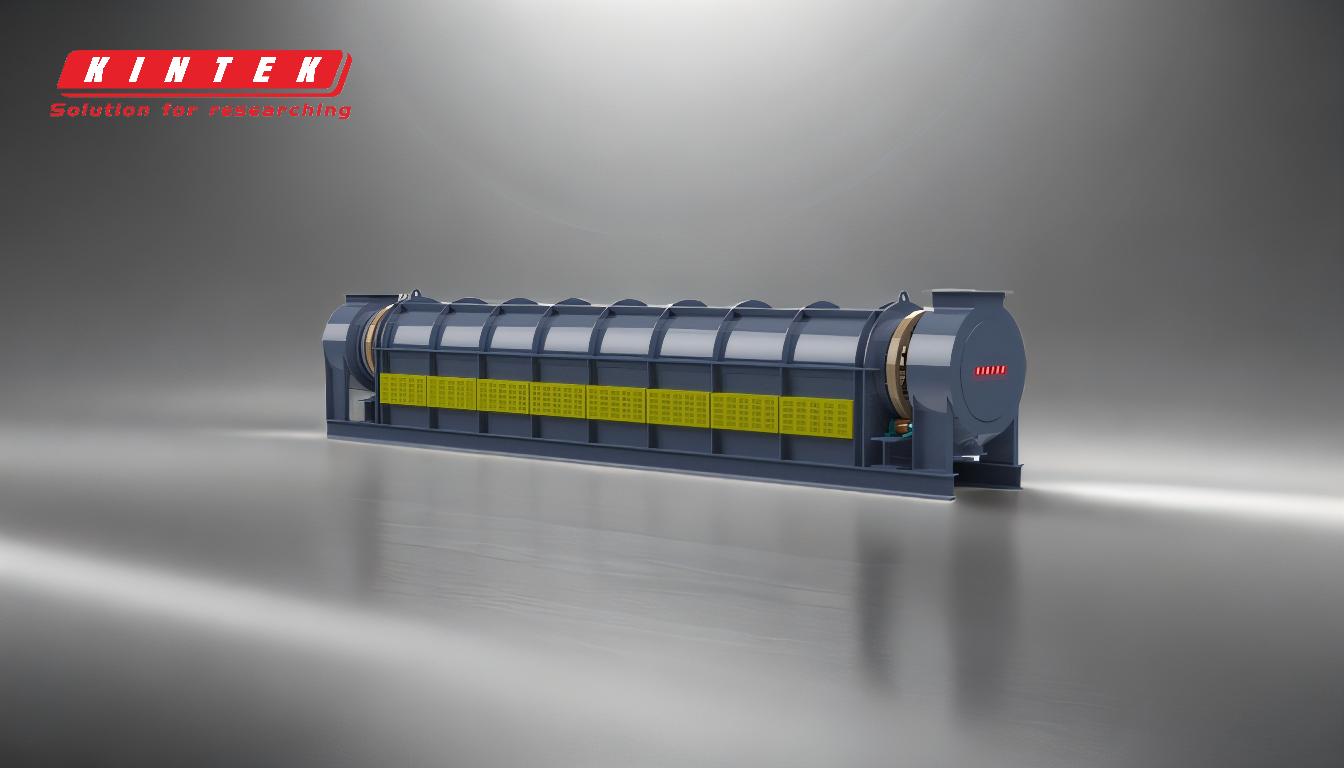
-
Origins of CVD and Early Applications:
- The CVD process traces its roots back to the late 19th and early 20th centuries, when researchers began experimenting with gas-phase reactions to deposit materials onto surfaces.
- Early applications included the production of carbon filaments for incandescent lamps and the coating of metals with protective layers.
- The process gained traction in the mid-20th century with the rise of the semiconductor industry, where CVD became essential for depositing silicon and other materials onto wafers.
-
Role of Vacuum Technology in CVD:
- Vacuum systems, like those used in short path vacuum distillation, played a crucial role in the development of CVD. By reducing atmospheric pressure, vacuum technology enabled precise control over deposition conditions, minimizing contamination and improving material purity.
- The ability to lower boiling points and prevent thermal degradation in CVD processes mirrored the advantages seen in vacuum distillation, making it possible to deposit thin films without damaging sensitive substrates.
-
Advancements in CVD Techniques:
- Over time, CVD techniques diversified to include variants such as Plasma-Enhanced CVD (PECVD), Low-Pressure CVD (LPCVD), and Atomic Layer Deposition (ALD). Each method leveraged vacuum systems to achieve specific material properties and deposition rates.
- These advancements were driven by the need for higher precision and scalability in industries like microelectronics, optics, and renewable energy.
-
Modern Applications of CVD:
- Today, CVD is widely used in the production of semiconductors, solar panels, and advanced coatings for aerospace and medical devices.
- The integration of vacuum systems continues to be a cornerstone of CVD, ensuring consistent results and enabling the deposition of complex, multi-layered structures.
-
Future Trends in CVD:
- Ongoing research focuses on improving the energy efficiency and environmental sustainability of CVD processes, as well as expanding their applications to emerging fields like nanotechnology and flexible electronics.
- Innovations in vacuum technology and process control are expected to further enhance the capabilities of CVD, making it an even more versatile and indispensable tool in materials science.
By understanding the historical context and technological evolution of CVD, it becomes clear how vacuum systems and precise process control have been instrumental in shaping its development. The parallels between CVD and short path vacuum distillation highlight the broader importance of vacuum technology in achieving high-purity, efficient material processing.
Summary Table:
Key Milestones | Details |
---|---|
Origins of CVD | Late 19th to early 20th century; gas-phase reactions for material deposition. |
Early Applications | Carbon filaments for lamps, protective metal coatings. |
Semiconductor Industry Boom | Mid-20th century; CVD became essential for silicon wafer deposition. |
Role of Vacuum Technology | Enabled precise control, reduced contamination, and improved material purity. |
Advancements in CVD Techniques | PECVD, LPCVD, ALD; driven by precision and scalability needs. |
Modern Applications | Semiconductors, solar panels, aerospace coatings, medical devices. |
Future Trends | Focus on sustainability, nanotechnology, and flexible electronics. |
Discover how CVD can revolutionize your material processing—contact our experts today!