The impact of pyrolysis techniques on biochar characteristics, particularly when applied to soil, is significant and multifaceted. Pyrolysis conditions, such as temperature, heating rate, and residence time, directly influence biochar's physical and chemical properties, which in turn affect its suitability for soil applications. Higher pyrolysis temperatures generally lead to biochar with increased carbon stability, reduced volatile matter, and higher surface area, making it more effective for long-term carbon sequestration and soil amendment. However, these conditions may also reduce nutrient availability and alter the biochar's pH, which can affect soil health and plant growth. Understanding these relationships is crucial for optimizing biochar production to meet specific soil amendment goals.
Key Points Explained:
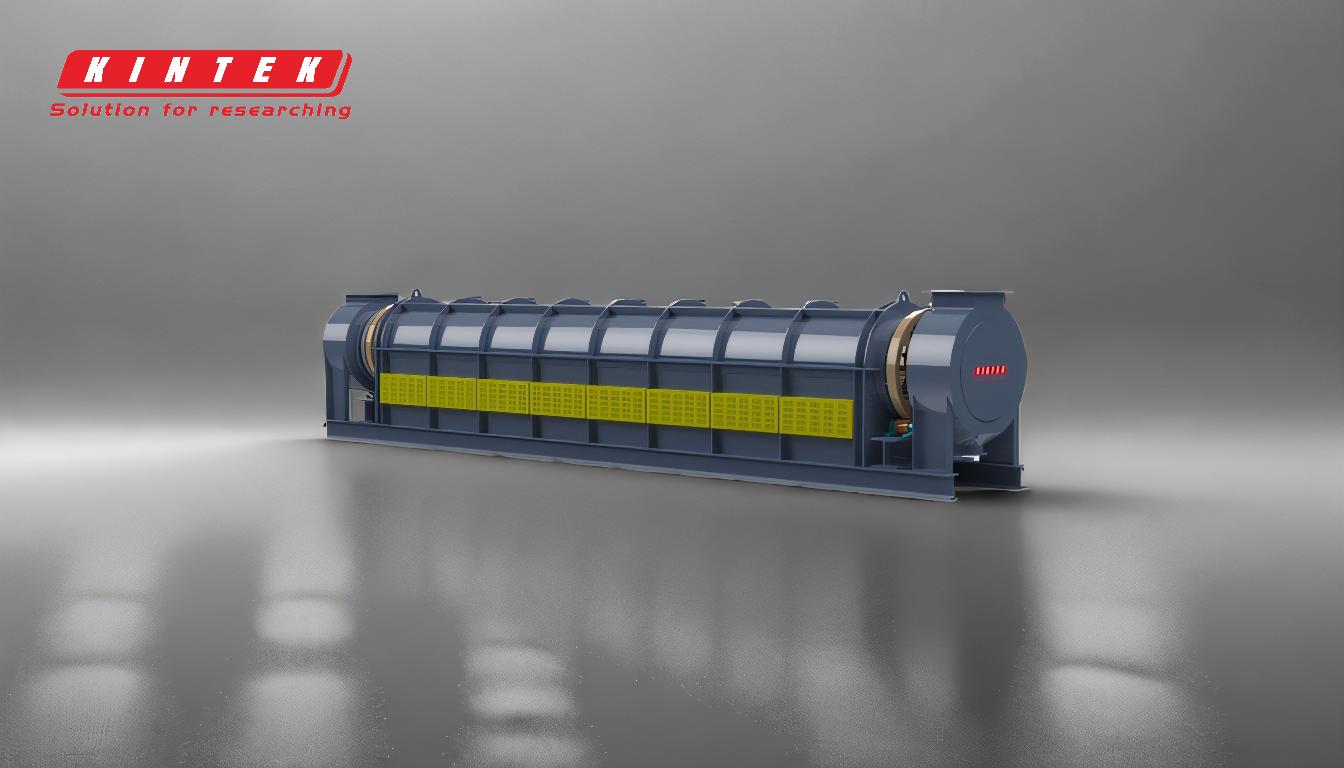
-
Influence of Pyrolysis Temperature:
- Higher Temperatures: Increase carbon stability and surface area, enhancing biochar's ability to sequester carbon and improve soil structure.
- Lower Temperatures: Result in biochar with higher volatile matter and nutrient content, which can be beneficial for short-term soil fertility.
-
Heating Rate:
- Slow Pyrolysis: Produces biochar with higher yield and more stable carbon, suitable for long-term soil carbon storage.
- Fast Pyrolysis: Leads to lower biochar yield but higher liquid and gas by-products, which might not be ideal for soil application.
-
Vapor Residence Time:
- Longer Residence Time: Allows for more complete carbonization, resulting in biochar with lower volatile content and higher stability.
- Shorter Residence Time: Produces biochar with more volatile compounds, which can be beneficial for immediate soil nutrient release but less stable over time.
-
Biomass Feedstock:
- Type of Biomass: Different feedstocks (e.g., wood, crop residues) yield biochar with varying properties. For example, woody biomass typically produces biochar with higher carbon content and stability.
- Feedstock Composition: The inherent nutrients and chemical composition of the feedstock influence the biochar's nutrient content and pH, affecting its suitability for different soil types.
-
Impact on Soil Application:
- Carbon Sequestration: Biochar produced at higher temperatures is more effective for long-term carbon storage in soil, helping mitigate climate change.
- Soil Fertility: Biochar with higher nutrient content and lower stability can enhance soil fertility in the short term but may require more frequent application.
- Soil pH and Microbial Activity: The pH of biochar can affect soil acidity, and its porous structure can influence microbial habitats, impacting soil health and plant growth.
By carefully selecting pyrolysis conditions, producers can tailor biochar properties to meet specific soil amendment needs, balancing benefits like carbon sequestration, nutrient availability, and soil health improvement.
Summary Table:
Factor | Impact on Biochar | Soil Application Effect |
---|---|---|
Pyrolysis Temperature | Higher temps: ↑ carbon stability, ↑ surface area, ↓ volatile matter | Effective for long-term carbon sequestration and soil structure improvement |
Lower temps: ↑ volatile matter, ↑ nutrient content | Beneficial for short-term soil fertility | |
Heating Rate | Slow pyrolysis: ↑ yield, ↑ stable carbon | Ideal for long-term soil carbon storage |
Fast pyrolysis: ↓ yield, ↑ liquid/gas by-products | Less suitable for soil application | |
Residence Time | Longer time: ↓ volatile content, ↑ stability | Better for long-term soil health |
Shorter time: ↑ volatile compounds | Provides immediate nutrient release but less stable over time | |
Biomass Feedstock | Woody biomass: ↑ carbon content, ↑ stability | Suitable for carbon-rich soil amendments |
Crop residues: Varies in nutrient content and pH | Tailored for specific soil needs | |
Soil Application | Carbon sequestration: Effective at higher temps | Mitigates climate change |
Soil fertility: Higher nutrient content at lower temps | Enhances short-term fertility but may require frequent application | |
Soil pH and microbial activity: Influences soil acidity and microbial habitats | Impacts soil health and plant growth |
Optimize your biochar production for soil applications—contact our experts today!