Graphite is a versatile material with significant industrial applications, particularly as a lubricant. Its unique properties, such as high thermal stability, low friction, and resistance to wear, make it suitable for various high-temperature and high-pressure environments. In industrial settings, graphite lubricants are used in machinery, metalworking, and even in specialized equipment like degassing shafts and impellers. Its ability to maintain dimensional integrity at extreme temperatures, up to 5000°F, further extends its utility in demanding applications. Additionally, graphite's lightweight and durable nature make it valuable in recreational products, though its industrial applications are more prominent.
Key Points Explained:
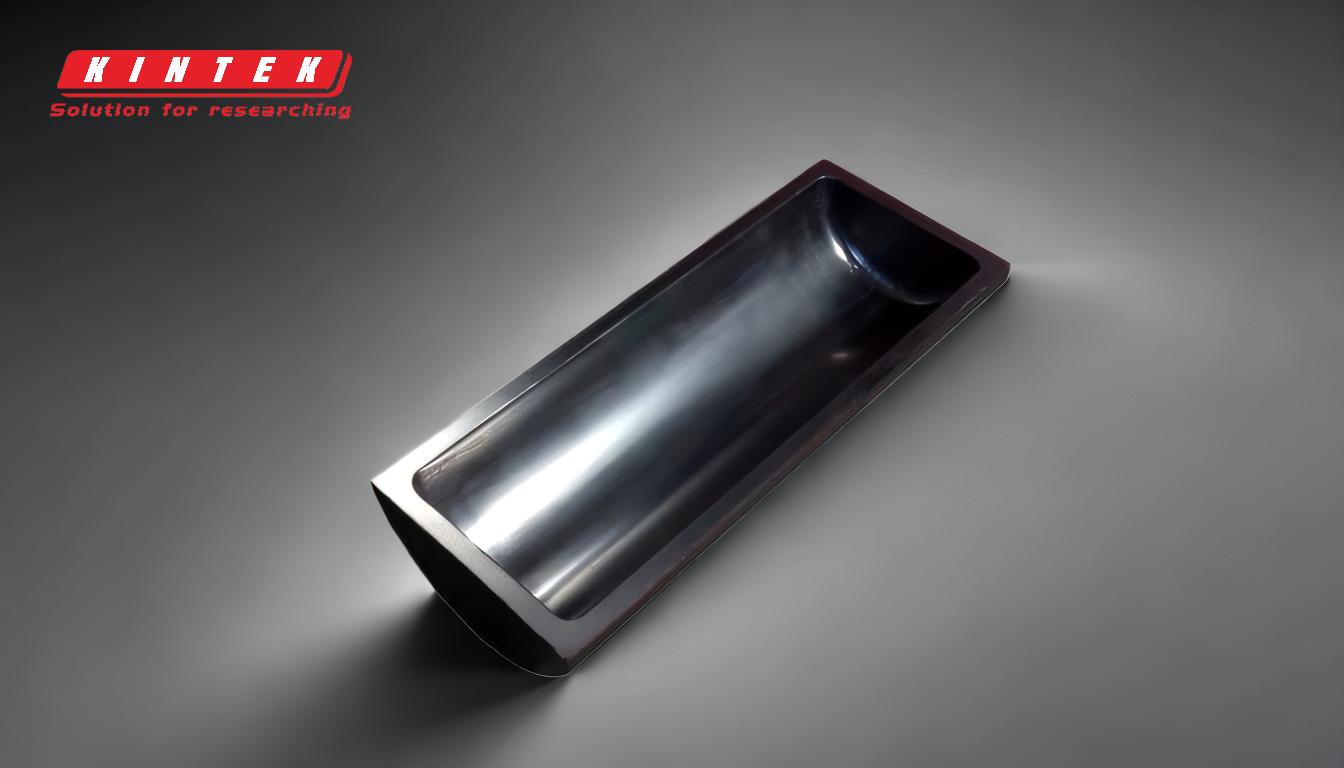
-
Thermal Stability and High-Temperature Applications:
- Graphite is highly valued in industries that operate under extreme temperatures. Its ability to withstand temperatures up to 5000°F without losing its structural integrity makes it ideal for use in high-temperature environments.
- Applications include degassing shafts and impellers, where graphite's thermal stability ensures consistent performance even under intense heat.
- It is also used in fluxing and injection tubes, where its resistance to thermal degradation is critical.
-
Low Friction and Wear Resistance:
- Graphite's natural lubricating properties make it an excellent choice for reducing friction and wear in industrial machinery. It is often used in bearings, seals, and other moving parts where minimizing friction is essential.
- Its self-lubricating nature means it can function effectively without the need for additional lubricants, which is particularly beneficial in environments where contamination must be avoided.
-
Use in Specialized Industrial Equipment:
- Graphite is employed in degassing shafts and impellers, which are critical components in metal processing. Its ability to resist thermal shock and maintain dimensional stability ensures reliable performance in these applications.
- In fluxing and injection tubes, graphite's chemical inertness and thermal properties make it a preferred material for handling molten metals and other high-temperature processes.
-
Applications Beyond Lubrication:
- While graphite is primarily known for its lubricating properties, it is also used in recreational products such as kite or tent frames, kayak riggers, and fishing rods. These applications leverage graphite's lightweight and durable nature.
- However, its industrial applications, particularly as a lubricant, remain its most significant use due to its unique combination of properties.
-
Graphite Furnace Applications:
- In industries requiring precise temperature control, such as metallurgy and materials testing, graphite furnaces are widely used. These furnaces rely on graphite's thermal conductivity and stability to achieve uniform heating and maintain high temperatures.
- The use of graphite in furnaces further underscores its importance in industrial processes, where its properties contribute to efficiency and reliability.
In summary, graphite's industrial applications as a lubricant are vast and varied, driven by its exceptional thermal stability, low friction, and wear resistance. Its use in specialized equipment and high-temperature environments highlights its importance in modern industrial processes. Additionally, while it finds some use in recreational products, its primary value lies in its ability to enhance performance and durability in demanding industrial settings.
Summary Table:
Property | Industrial Application |
---|---|
Thermal Stability | Used in degassing shafts, impellers, and fluxing tubes for high-temperature environments. |
Low Friction | Ideal for bearings, seals, and machinery to reduce wear and friction. |
Wear Resistance | Maintains performance in high-pressure and high-wear industrial settings. |
Chemical Inertness | Suitable for handling molten metals and corrosive materials. |
Dimensional Integrity | Retains shape and functionality at temperatures up to 5000°F. |
Learn how graphite lubricants can optimize your industrial processes—contact us today for expert advice!