The inert atmosphere method involves replacing the ambient air in a system or device with non-reactive (inert) gases like nitrogen, argon, or carbon dioxide to create a controlled environment. This method is widely used in industries such as heat treatment, food preservation, and engineering to prevent oxidation, contamination, and unwanted chemical reactions. By maintaining a stable, non-reactive environment, the inert atmosphere method ensures the integrity, quality, and safety of materials and processes. Key applications include protecting metals and ceramics during heat treatment, preventing spoilage in food preservation, and reducing fire or explosion risks in industrial settings.
Key Points Explained:
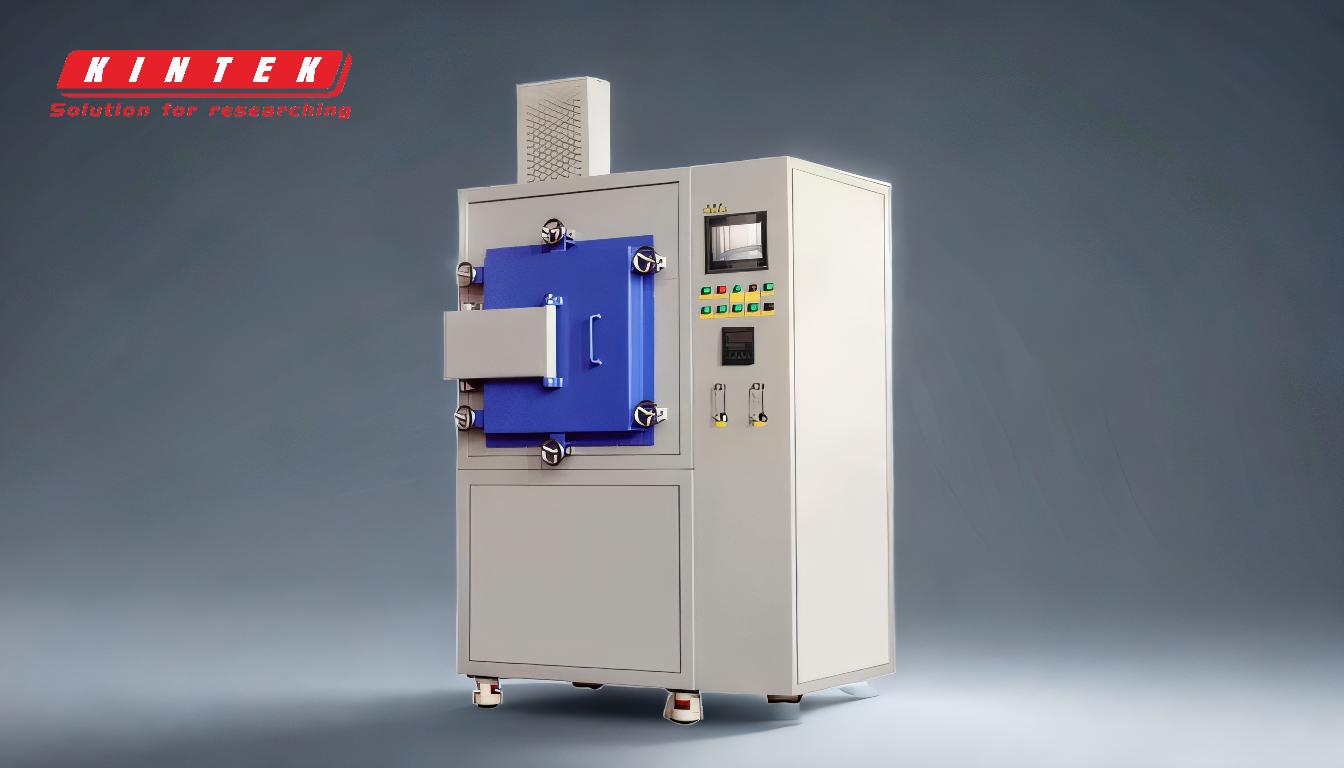
-
Definition and Purpose of an Inert Atmosphere:
- An inert atmosphere is a controlled environment created by replacing reactive gases (like oxygen) with non-reactive gases (such as nitrogen or argon).
- The primary purpose is to prevent oxidation, contamination, and unwanted chemical reactions, ensuring the stability and integrity of materials or processes.
-
Common Gases Used:
- Nitrogen: Widely used due to its high natural abundance, affordability, and high diffusion rate.
- Argon: Preferred for applications requiring a denser and more stable inert gas, such as in high-temperature heat treatment.
- Carbon Dioxide: Used in specific applications like food preservation or fire suppression.
- Helium and Hydrogen: Occasionally used in specialized applications, though less common due to cost or reactivity concerns.
-
Applications of Inert Atmospheres:
- Heat Treatment: Inert atmospheres are crucial in furnaces to protect metals and ceramics from oxidation during high-temperature processes. This ensures the materials retain their desired properties and structural integrity.
- Food Preservation: Replacing oxygen with inert gases like nitrogen or carbon dioxide slows down spoilage and extends shelf life by inhibiting microbial growth and oxidation.
- Industrial Safety: Inert atmospheres reduce the risk of fire or explosions by eliminating reactive gases in environments where flammable materials are present.
-
Scientific Basis:
- The method relies on the principle that different gases have varying reactivity and oxidation potentials. By replacing reactive gases with inert ones, reaction rates are reduced, and stability is maintained even under extreme conditions.
- For example, argon and nitrogen are chemically inert, meaning they do not readily react with other substances, making them ideal for creating a stable environment.
-
Implementation in Furnaces:
- In heat-treating furnaces, the process typically involves:
- Creating a slight vacuum (up to 0.1MPa) using a rotary vane oil-filled vacuum pump to remove ambient air.
- Purging the furnace with inert gas (argon or nitrogen) to surround the material being treated.
- Maintaining the inert atmosphere throughout the process to prevent oxide formation and contamination.
- In heat-treating furnaces, the process typically involves:
-
Benefits of Using an Inert Atmosphere:
- Reduced Oxidation: Slows down or prevents oxidation processes, preserving the quality of materials.
- Contamination Prevention: Protects materials from contamination by reactive gases or particles.
- Enhanced Safety: Reduces the risk of fire or explosions in industrial settings.
- Vacuum Creation: Facilitates the creation of a vacuum environment, which is essential for certain processes.
- Chemical Reaction Control: Slows down or prevents unwanted chemical reactions, ensuring process stability.
-
Considerations for Equipment and Consumable Purchasers:
- Gas Selection: Choose the appropriate inert gas based on the application. For example, nitrogen is cost-effective for general use, while argon is better suited for high-temperature applications.
- System Compatibility: Ensure that the equipment (e.g., furnaces, storage systems) is compatible with the chosen inert gas and can maintain the required atmosphere.
- Cost and Availability: Consider the cost and availability of the inert gas, as well as the infrastructure needed for its storage and delivery.
- Safety Measures: Implement safety protocols to handle inert gases, especially in confined spaces where oxygen displacement could pose risks.
By understanding the principles, applications, and practical considerations of the inert atmosphere method, equipment and consumable purchasers can make informed decisions to optimize processes, ensure material quality, and enhance safety in their operations.
Summary Table:
Key Aspect | Details |
---|---|
Definition | Replacing ambient air with non-reactive gases (e.g., nitrogen, argon). |
Purpose | Prevent oxidation, contamination, and unwanted chemical reactions. |
Common Gases | Nitrogen, Argon, Carbon Dioxide, Helium, Hydrogen. |
Applications | Heat treatment, food preservation, industrial safety. |
Benefits | Reduced oxidation, contamination prevention, enhanced safety. |
Considerations | Gas selection, system compatibility, cost, safety measures. |
Optimize your processes with inert atmosphere solutions—contact our experts today!