DC magnetron sputtering is a physical vapor deposition (PVD) technique used to deposit thin films of materials onto substrates. It involves a direct current (DC) power source to generate a plasma in a low-pressure gas environment, typically argon. The process relies on a magnetic field to enhance the efficiency of sputtering by trapping electrons near the target surface, increasing plasma density and ion bombardment. This results in high-quality coatings with excellent uniformity and adhesion. The magnetic field plays a critical role in controlling the movement of electrons and ions, ensuring sustained plasma and efficient sputtering of target materials.
Key Points Explained:
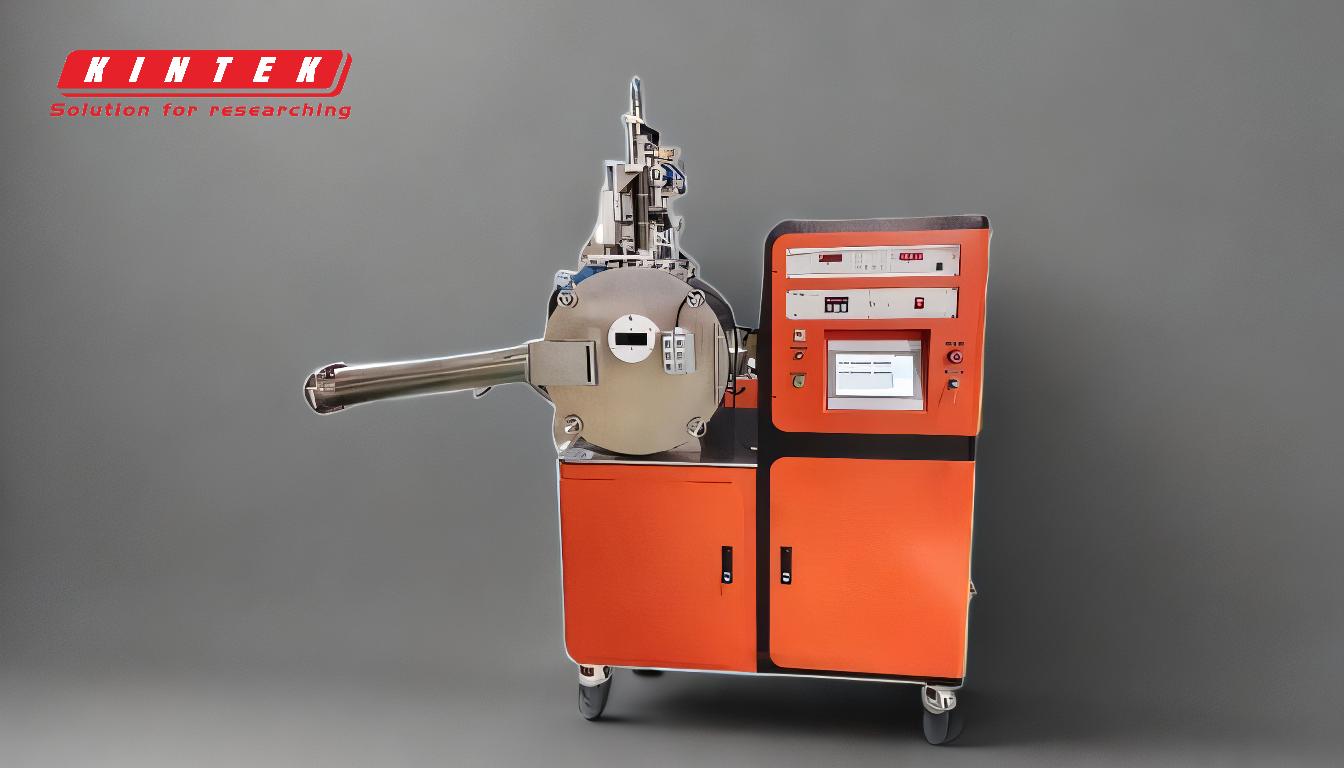
-
Basic Principle of DC Magnetron Sputtering:
- DC magnetron sputtering uses a DC power source to create a plasma in a low-pressure gas environment.
- The target material, typically a metal or ceramic, is negatively charged (cathode), attracting positively charged ions from the plasma.
- These ions bombard the target surface, transferring energy and causing atoms to be ejected (sputtered) from the target.
- The sputtered atoms then deposit onto the substrate, forming a thin film.
-
Role of the Magnetic Field:
- A magnetic field is applied perpendicular to the electric field near the cathode.
- This magnetic field traps electrons, forcing them to move in a cycloidal (spiral) path rather than traveling directly to the anode.
- The increased path length of electrons enhances the probability of collisions with gas atoms, leading to higher ionization rates and denser plasma.
- The magnetic field also confines the plasma close to the target surface, increasing the efficiency of ion bombardment and sputtering.
-
Plasma Generation and Ion Bombardment:
- Electrons emitted from the cathode collide with argon atoms in the gas, creating Ar+ ions and additional electrons.
- The Ar+ ions are accelerated toward the negatively charged target by the electric field, gaining high kinetic energy.
- When these ions strike the target surface, they transfer their energy, causing target atoms to be ejected.
- The ejected atoms travel through the vacuum chamber and deposit onto the substrate.
-
Advantages of Magnetic Field in Sputtering:
- Increased Sputtering Rate: The magnetic field increases the density of ions near the target, leading to more efficient sputtering.
- Uniform Deposition: The controlled movement of electrons and ions ensures a more uniform deposition of material on the substrate.
- Lower Operating Pressure: The magnetic field allows the process to operate at lower pressures (1–100 mTorr), reducing contamination and improving film quality.
- Sustained Plasma: The magnetic field helps maintain a stable plasma, enabling continuous sputtering over long periods.
-
Applications of DC Magnetron Sputtering:
- DC magnetron sputtering is widely used in industries for depositing thin films of metals (e.g., Cu, Fe, Ni) and ceramics.
- It is ideal for applications requiring high-quality coatings, such as semiconductors, optical coatings, and protective layers.
- The technique is also used in research and development for creating advanced materials with precise control over thickness and composition.
-
System Components:
- Cathode (Target): Holds the material to be sputtered and is negatively charged.
- Anode (Substrate Holder): Grounded and holds the substrate where the thin film is deposited.
- Magnetic Assembly: Generates the magnetic field to control electron and ion movement.
- Vacuum Chamber: Maintains the low-pressure environment necessary for plasma generation.
- DC Power Supply: Provides the voltage needed to create and sustain the plasma.
-
Process Parameters:
- Power Supply: DC voltage typically ranges from a few hundred to several thousand volts.
- Gas Pressure: Operates at low pressures (1–100 mTorr) to minimize collisions and ensure efficient sputtering.
- Magnetic Field Strength: Optimized to balance plasma confinement and sputtering efficiency.
- Target Material: Determines the composition of the deposited film and must be compatible with the sputtering process.
By understanding these key points, one can appreciate the critical role of the magnetic field in DC magnetron sputtering and how it enhances the efficiency, uniformity, and quality of thin film deposition. This technique is a cornerstone of modern materials science and industrial coating processes.
Summary Table:
Key Aspect | Details |
---|---|
Basic Principle | Uses DC power to create plasma, sputtering target material onto substrates. |
Role of Magnetic Field | Traps electrons, increases plasma density, and enhances sputtering rate. |
Advantages | High-quality coatings, uniform deposition, lower operating pressure. |
Applications | Semiconductors, optical coatings, protective layers, and advanced R&D. |
System Components | Cathode, anode, magnetic assembly, vacuum chamber, DC power supply. |
Process Parameters | DC voltage, gas pressure, magnetic field strength, target material. |
Discover how DC magnetron sputtering can revolutionize your thin film processes—contact our experts today!