The main difference between Physical Vapor Deposition (PVD) and Chemical Vapor Deposition (CVD) lies in their deposition mechanisms, operating conditions, and outcomes. PVD involves physically vaporizing a solid material and depositing it onto a substrate, typically at lower temperatures and without chemical reactions. In contrast, CVD relies on chemical reactions between gaseous precursors and the substrate, often requiring higher temperatures. PVD is known for better surface smoothness and adhesion, while CVD provides superior film density and coverage. The choice between PVD and CVD depends on specific application requirements, such as film quality, substrate compatibility, and production scale.
Key Points Explained:
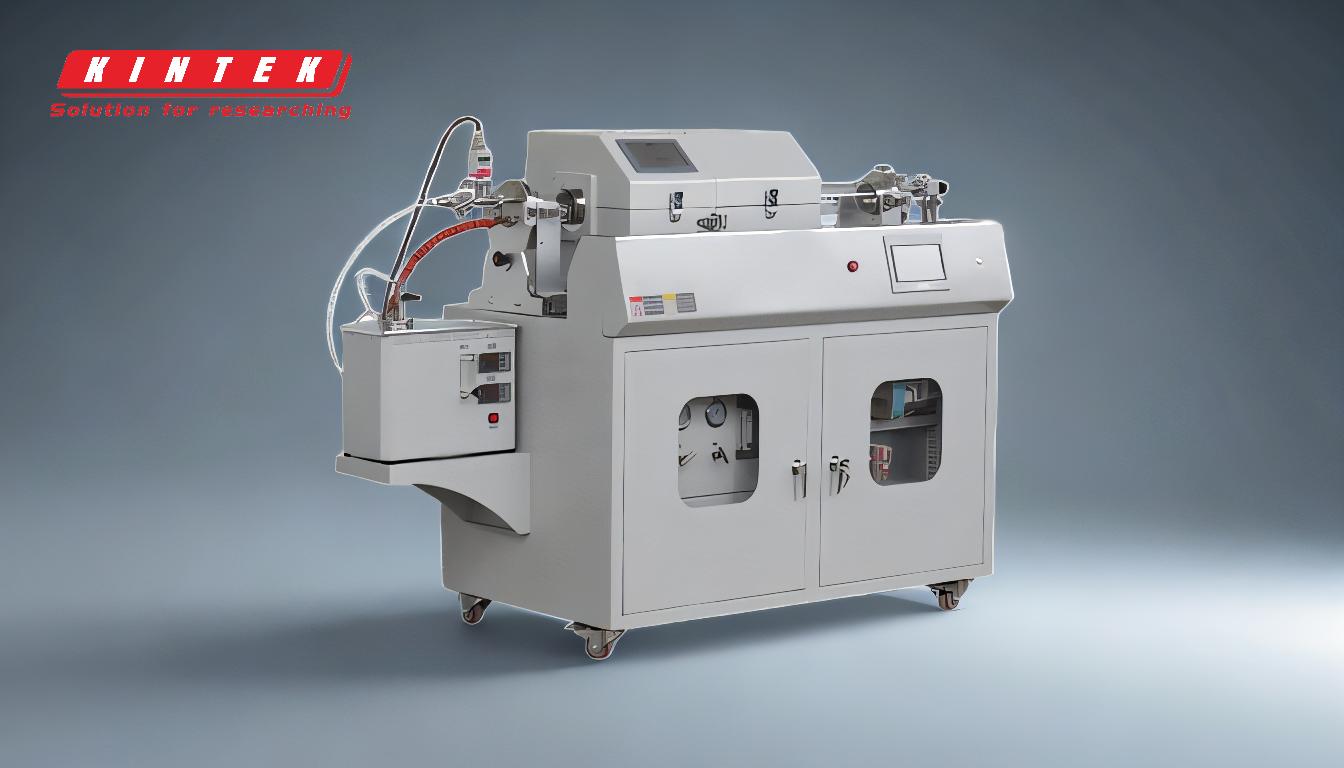
-
Deposition Mechanism:
- PVD: Uses physical methods like evaporation or sputtering to vaporize a solid material, which then condenses onto the substrate. This process is line-of-sight, meaning deposition occurs directly from the source to the substrate.
- CVD: Involves chemical reactions between gaseous precursors and the substrate surface, forming a solid film. This process is multidirectional, allowing for uniform coverage even on complex geometries.
-
Operating Temperature:
- PVD: Operates at lower temperatures, making it suitable for temperature-sensitive substrates. It does not typically require heating the substrate.
- CVD: Often requires high temperatures to facilitate chemical reactions, which can limit its use with certain substrates but enhances film density and uniformity.
-
Film Quality:
- PVD: Produces films with excellent surface smoothness and strong adhesion, ideal for applications requiring precise surface finishes.
- CVD: Yields films with superior density and coverage, making it suitable for applications requiring robust and uniform coatings.
-
Deposition Rate:
- PVD: Generally has lower deposition rates compared to CVD, though specific techniques like Electron Beam PVD (EBPVD) can achieve high rates.
- CVD: Typically offers higher deposition rates, which can be advantageous for large-scale production.
-
Material Utilization Efficiency:
- PVD: High material utilization efficiency, especially in techniques like EBPVD, where up to 100% of the material can be deposited onto the substrate.
- CVD: May involve the formation of corrosive by-products and impurities, reducing material efficiency.
-
Applications:
- PVD: Preferred for high-volume production, decorative coatings, and applications requiring precise control over film thickness and surface finish.
- CVD: Commonly used for depositing metals, semiconductors, and ceramics, particularly in applications requiring high film density and uniformity.
-
Environmental and Safety Considerations:
- PVD: Does not produce corrosive by-products, making it safer and more environmentally friendly.
- CVD: May generate corrosive or hazardous gases, requiring additional safety measures and waste management.
By understanding these key differences, equipment and consumable purchasers can make informed decisions based on the specific needs of their applications, such as film quality, substrate compatibility, and production scale.
Summary Table:
Aspect | PVD | CVD |
---|---|---|
Deposition Mechanism | Physical vaporization (evaporation/sputtering); line-of-sight process. | Chemical reactions with gaseous precursors; multidirectional process. |
Operating Temperature | Lower temperatures, suitable for sensitive substrates. | Higher temperatures, enhances film density and uniformity. |
Film Quality | Excellent surface smoothness and adhesion. | Superior film density and coverage. |
Deposition Rate | Lower rates, but EBPVD can achieve high rates. | Higher rates, ideal for large-scale production. |
Material Efficiency | High efficiency, up to 100% material utilization. | May produce corrosive by-products, reducing efficiency. |
Applications | High-volume production, decorative coatings, precise finishes. | Metals, semiconductors, ceramics; robust and uniform coatings. |
Environmental Impact | Safer, no corrosive by-products. | May generate hazardous gases, requiring safety measures. |
Still unsure which deposition method is right for your application? Contact our experts today for personalized advice!