Chemical Vapor Deposition (CVD) is a widely used technique for depositing thin films of materials onto a substrate through chemical reactions in the vapor phase. The process involves several key steps, including the transport of gaseous precursors to the substrate surface, adsorption, chemical reactions, and the formation of a solid film. CVD is highly controllable and can produce uniform, high-quality coatings, making it suitable for applications in electronics, optics, and energy storage. However, it often requires sophisticated equipment and precise conditions, which can increase costs and limit its scalability for large-scale production.
Key Points Explained:
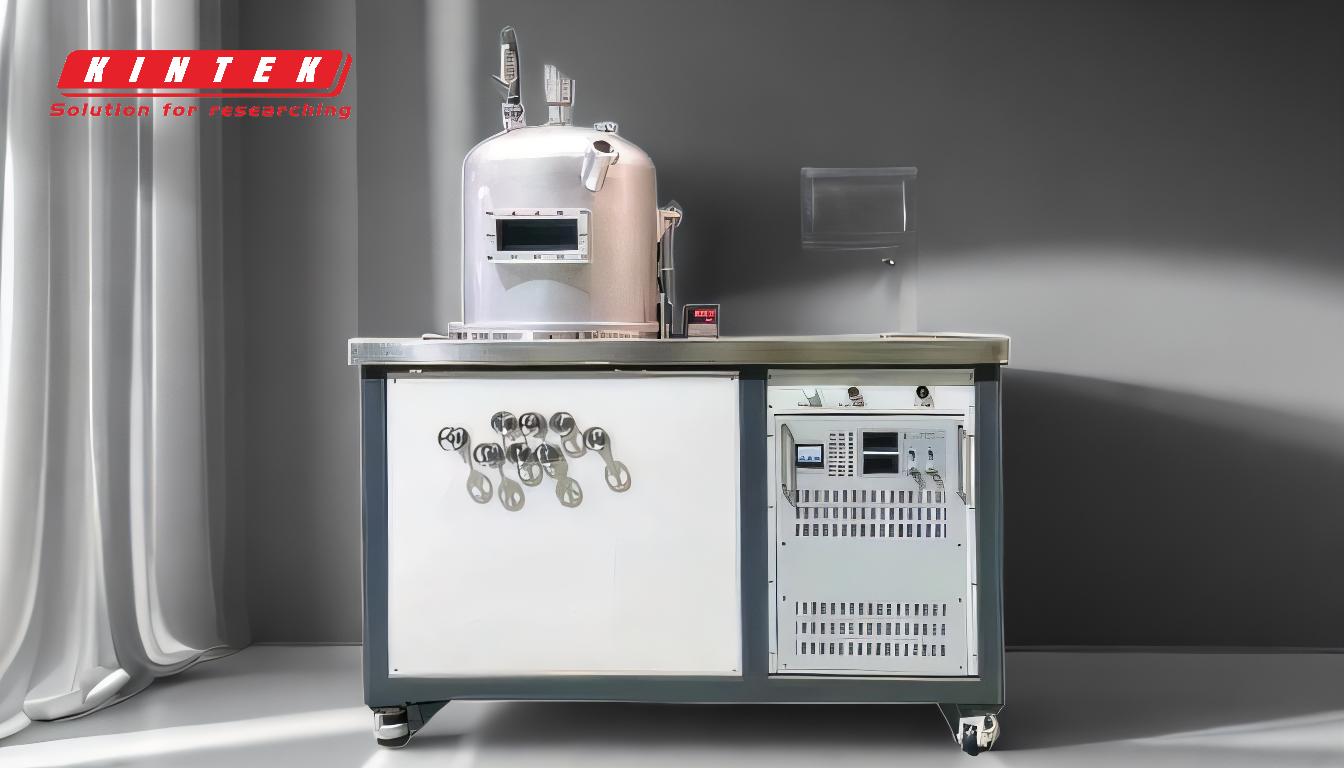
-
Introduction to CVD:
- CVD is a process used to deposit thin films of materials onto a substrate through chemical reactions in the vapor phase.
- It is widely used in industries such as electronics, optics, and energy storage due to its ability to produce high-quality, uniform coatings.
-
Steps Involved in CVD:
-
Transport of Reacting Gaseous Species:
- The process begins with the introduction of volatile precursors into a reaction chamber, often under vacuum or controlled atmospheric conditions.
- These precursors are transported to the substrate surface through diffusion or convection.
-
Adsorption of Species on the Surface:
- Once the gaseous precursors reach the substrate, they adsorb onto its surface.
- Adsorption is a critical step as it determines the initial interaction between the precursor molecules and the substrate.
-
Heterogeneous Surface-Catalyzed Reactions:
- The adsorbed species undergo chemical reactions on the substrate surface, often catalyzed by the surface itself.
- These reactions can include decomposition, oxidation, reduction, or other chemical transformations.
-
Surface Diffusion to Growth Sites:
- The reacted species diffuse across the substrate surface to find suitable growth sites.
- Surface diffusion is essential for the uniform growth of the thin film.
-
Nucleation and Growth of the Film:
- At the growth sites, nucleation occurs, leading to the formation of small clusters of the deposited material.
- These clusters grow and coalesce to form a continuous thin film.
-
Desorption of Gaseous Reaction Products:
- As the film grows, by-products of the chemical reactions are desorbed from the surface.
- These by-products are transported away from the substrate, often through the same mechanisms that brought the precursors to the surface.
-
Transport of Reacting Gaseous Species:
-
Types of CVD Reactions:
-
Decomposition Reactions:
- In some CVD processes, the precursor molecules decompose upon heating, releasing the desired material in atomic or molecular form.
- For example, in the deposition of carbon films, solid glucose can be heated to decompose into carbon clusters that deposit onto the substrate.
-
Reduction Reactions:
- In other cases, the precursor molecules undergo reduction reactions, often in the presence of a reducing gas like hydrogen.
- This is common in the deposition of metals or metal oxides.
-
Oxidation Reactions:
- Oxidation reactions can also occur, particularly in the deposition of oxide films.
- Oxygen or other oxidizing agents are introduced into the reaction chamber to facilitate the formation of oxide layers.
-
Chemical Interaction with Other Gases:
- Sometimes, the precursor gases chemically interact with other gases or vapors in the chamber to form the desired film.
- This can lead to the formation of complex compounds or alloys.
-
Decomposition Reactions:
-
Advantages of CVD:
-
High-Quality Films:
- CVD can produce films that are stoichiometric, dense, and of high quality, with excellent adhesion to the substrate.
-
Uniformity and Control:
- The process allows for precise control over film thickness, composition, and morphology, leading to uniform coatings.
-
Versatility:
- CVD can be used to deposit a wide range of materials, including metals, semiconductors, and insulators.
-
Environmental Friendliness:
- Some CVD processes are environmentally friendly, as they can use non-toxic precursors and produce minimal waste.
-
High-Quality Films:
-
Challenges and Limitations of CVD:
-
High Costs:
- The need for sophisticated equipment and precise control over process parameters can make CVD expensive.
-
Scalability Issues:
- CVD is often less suitable for large-scale production due to its slower deposition rates and higher costs.
-
Complexity:
- The process can be complex, requiring careful optimization of parameters such as temperature, pressure, and gas flow rates.
-
Lower Decomposition Rates:
- Some precursors have lower decomposition rates, leading to longer production times and increased costs.
-
High Costs:
-
Applications of CVD:
-
Electronics:
- CVD is widely used in the semiconductor industry for depositing thin films of silicon, silicon dioxide, and other materials used in integrated circuits.
-
Optics:
- CVD is used to deposit anti-reflective coatings, optical filters, and other thin films used in optical devices.
-
Energy Storage:
- In the field of energy storage, CVD is used to coat materials like LiFePO4 with carbon to enhance their performance in lithium-ion batteries.
-
Protective Coatings:
- CVD is used to deposit protective coatings on tools, components, and other materials to improve their durability and performance.
-
Electronics:
In summary, Chemical Vapor Deposition is a versatile and precise method for depositing thin films, with applications across various industries. While it offers significant advantages in terms of film quality and control, it also presents challenges related to cost, scalability, and process complexity. Understanding the mechanisms and steps involved in CVD is crucial for optimizing the process and achieving the desired film properties.
Summary Table:
Aspect | Details |
---|---|
Process | Deposits thin films via chemical reactions in the vapor phase. |
Key Steps | Transport, adsorption, surface reactions, diffusion, nucleation, desorption. |
Advantages | High-quality, uniform films; precise control; versatile; eco-friendly. |
Challenges | High costs, scalability issues, complexity, lower decomposition rates. |
Applications | Electronics, optics, energy storage, protective coatings. |
Discover how CVD can enhance your thin film processes—contact our experts today for tailored solutions!