Biomass pyrolysis is a thermal decomposition process that occurs in the absence of oxygen, transforming biomass into biochar, bio-oil, and syngas. The mechanism involves breaking down complex organic molecules in biomass into simpler compounds through heat. Key factors influencing the process include temperature, heating rate, residence time, biomass composition, and particle size. Higher temperatures favor gas production, while lower temperatures enhance char formation. The process is divided into stages: pre-treatment, pyrolysis, and post-treatment. Pre-treatment involves drying and grinding the biomass to optimize thermal decomposition. During pyrolysis, biomass is heated, leading to the release of volatiles and the formation of char. Post-treatment includes cooling and refining the products. The process is highly dependent on reaction parameters, which determine the yield and quality of the end products.
Key Points Explained:
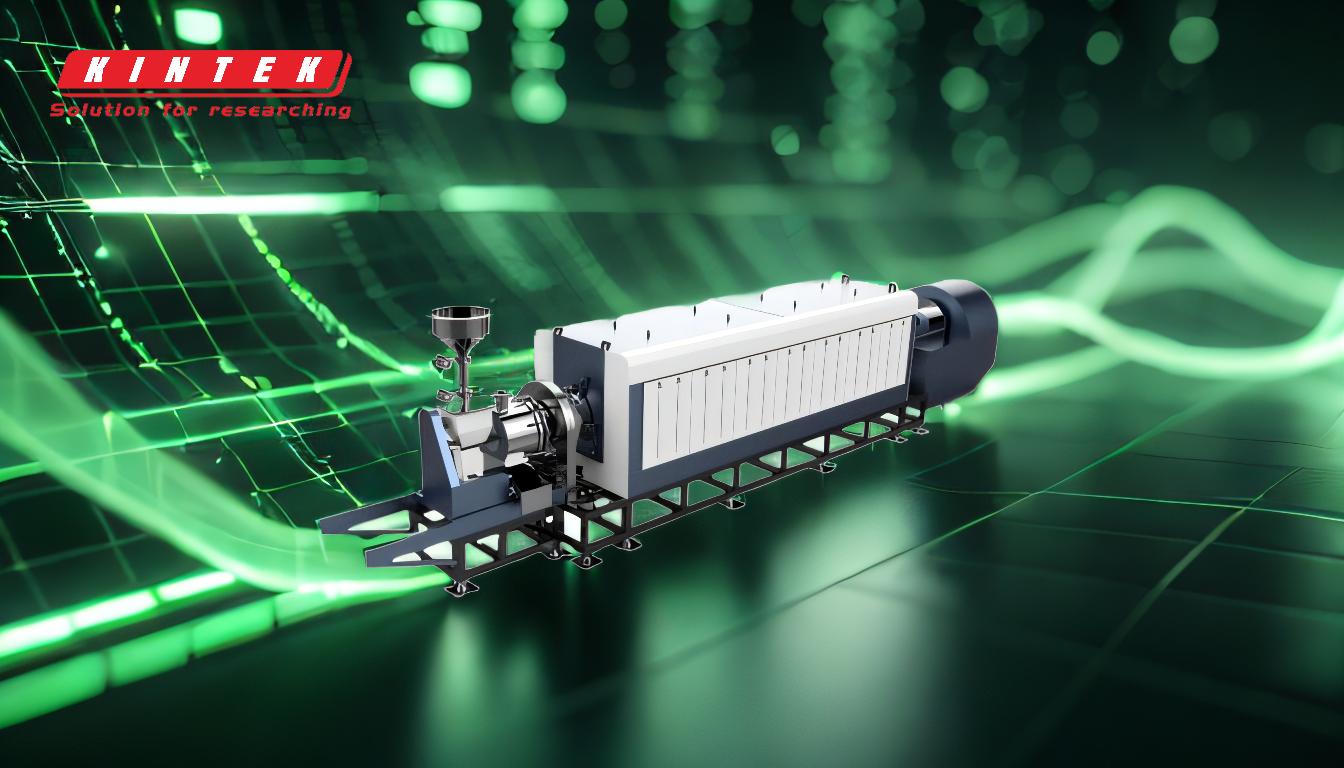
-
Definition and Purpose of Biomass Pyrolysis:
- Biomass pyrolysis is a thermochemical process that decomposes organic materials in the absence of oxygen.
- The primary goal is to convert biomass into valuable products such as biochar, bio-oil, and syngas, which can be used for energy, chemicals, or soil amendment.
-
Key Stages of the Pyrolysis Process:
-
Pre-treatment:
- Biomass is dried to reduce moisture content, which improves the efficiency of thermal decomposition.
- The biomass is crushed or ground into smaller particles to increase the surface area, facilitating faster and more uniform heating.
-
Pyrolysis:
- The pre-treated biomass is heated in a pyrolysis chamber at temperatures typically ranging from 200°C to 900°C.
- The heat breaks down the complex organic molecules in the biomass into simpler compounds, releasing volatiles and forming solid char.
-
Post-treatment:
- The products are cooled and refined. For example, biochar is discharged and cooled, while vapors are condensed into bio-oil.
- Exhaust gases are cleaned (de-dusting) to remove harmful substances before being released.
-
Pre-treatment:
-
Factors Influencing Pyrolysis Outcomes:
-
Temperature:
- Higher temperatures (above 500°C) favor the production of non-condensable gases (syngas).
- Lower temperatures (below 500°C) promote the formation of biochar and bio-oil.
-
Heating Rate:
- Fast heating rates lead to higher yields of bio-oil, as they minimize secondary reactions.
- Slow heating rates favor char production.
-
Residence Time:
- Longer residence times allow for more complete thermal conversion, increasing gas yields.
- Shorter residence times are preferred for maximizing liquid (bio-oil) production.
-
Biomass Composition:
- Different biomass components (cellulose, hemicellulose, lignin) decompose at different temperatures, affecting the product distribution.
-
Particle Size:
- Smaller particles decompose more quickly and uniformly, leading to higher yields of pyrolysis oil.
-
Temperature:
-
Product Distribution and Optimization:
-
Char Production:
- Maximized at low temperatures (200-400°C) and slow heating rates.
-
Bio-oil Production:
- Optimal at moderate temperatures (400-600°C) with high heating rates and short gas residence times.
-
Syngas Production:
- Increased at high temperatures (above 700°C) with low heating rates and long residence times.
-
Char Production:
-
Mechanism of Thermal Decomposition:
-
Primary Reactions:
- Biomass undergoes thermal cracking, breaking down into smaller molecules such as gases, tars, and char.
-
Secondary Reactions:
- Volatiles released during primary reactions may further decompose or recombine, depending on the temperature and residence time.
-
Free Radical Formation:
- The breakdown of biomass generates free radicals, which play a crucial role in the formation of final products.
-
Primary Reactions:
-
Applications and Importance:
-
Biochar:
- Used as a soil amendment to improve fertility and carbon sequestration.
-
Bio-oil:
- Can be refined into biofuels or used as a feedstock for chemical production.
-
Syngas:
- Utilized as a renewable energy source for heat, electricity, or synthesis of chemicals.
-
Biochar:
In summary, biomass pyrolysis is a versatile process that converts organic materials into valuable products through controlled thermal decomposition. The process is influenced by various factors, including temperature, heating rate, residence time, and biomass properties. By optimizing these parameters, it is possible to tailor the product distribution to meet specific needs, making pyrolysis a key technology in the transition to sustainable energy and resource management.
Summary Table:
Key Aspect | Details |
---|---|
Process | Thermal decomposition of biomass in the absence of oxygen. |
Key Products | Biochar, bio-oil, and syngas. |
Key Stages | Pre-treatment, pyrolysis, and post-treatment. |
Factors Influencing | Temperature, heating rate, residence time, biomass composition, particle size. |
Applications | Soil amendment, biofuels, renewable energy, and chemical production. |
Discover how biomass pyrolysis can benefit your projects—contact us today for expert guidance!