Reactive sputtering is a thin-film deposition technique where a target material is sputtered in the presence of a reactive gas, such as oxygen or nitrogen, to form a compound film on a substrate. The process involves ionizing the reactive gas in a plasma environment, which then chemically reacts with the sputtered target atoms to form compounds like oxides or nitrides. This method allows precise control over film composition and properties by adjusting parameters like gas flow and partial pressure. The mechanism is complex due to interactions between the reactive gas and target, often requiring careful optimization to avoid hysteresis-like behavior and achieve desired film stoichiometry and functional properties.
Key Points Explained:
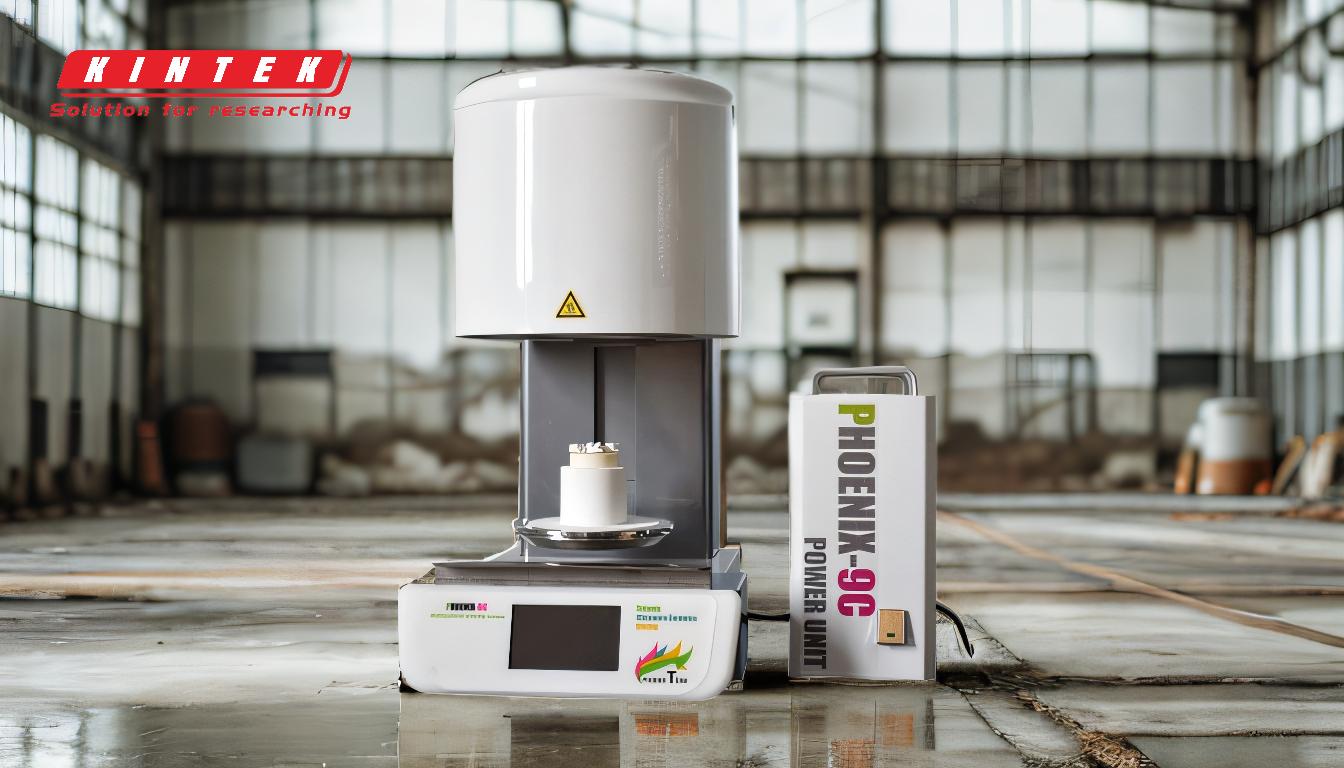
-
Definition and Purpose of Reactive Sputtering:
- Reactive sputtering is a variation of plasma sputtering used to deposit thin films with specific chemical compositions, such as oxides or nitrides.
- The process involves introducing a reactive gas (e.g., oxygen or nitrogen) into the sputtering chamber, which chemically reacts with the sputtered target material to form a compound film.
-
Key Components Involved:
- Target Material: The source of atoms to be sputtered (e.g., silicon, aluminum, or titanium).
- Reactive Gas: A gas like oxygen or nitrogen that reacts with the sputtered atoms to form a compound.
- Inert Gas: Typically argon, used to create the plasma that sputters the target material.
- Substrate: The surface on which the thin film is deposited (e.g., a silicon wafer).
-
Mechanism of Reactive Sputtering:
- The inert gas (argon) is ionized to form a plasma, which bombards the target material, ejecting atoms into the chamber.
- The reactive gas is introduced into the chamber and becomes ionized in the plasma environment.
- The ionized reactive gas chemically reacts with the sputtered target atoms, forming a compound (e.g., silicon oxide or titanium nitride).
- The compound is then deposited onto the substrate as a thin film.
-
Role of Reactive Gas:
- The reactive gas determines the chemical composition of the deposited film.
- For example, oxygen can form oxides (e.g., silicon oxide), while nitrogen can form nitrides (e.g., titanium nitride).
- The amount and type of reactive gas influence the stoichiometry and properties of the film.
-
Challenges and Control Parameters:
- Hysteresis-Like Behavior: The introduction of a reactive gas can lead to non-linear effects, making the process difficult to control. This requires careful management of parameters like gas flow and partial pressure.
- Berg Model: A theoretical framework used to predict the impact of the reactive gas on target erosion and deposition rates.
- Stoichiometry Control: Adjusting the relative pressures of inert and reactive gases allows precise control over film composition and properties, such as stress and refractive index.
-
Applications of Reactive Sputtering:
- Optical Coatings: Producing films with specific refractive indices for lenses and mirrors.
- Barrier Layers: Creating thin solid films like titanium nitride for use in semiconductor devices.
- Functional Films: Depositing materials with tailored mechanical, electrical, or optical properties for advanced applications.
-
DC and HF Variants:
- Reactive sputtering can be performed using direct current (DC) or high-frequency (HF) power sources.
- The choice of power source depends on the target material and desired film properties.
-
Advantages of Reactive Sputtering:
- Enables the deposition of a wide range of compound films with precise control over composition and properties.
- Suitable for creating films with specific functional characteristics, such as high hardness, transparency, or conductivity.
-
Practical Considerations:
- The process requires careful optimization to balance the reactive gas flow and sputtering rate.
- Proper chamber design and gas delivery systems are critical to achieving consistent results.
By understanding these key points, equipment and consumable purchasers can better evaluate the requirements for reactive sputtering systems, such as the choice of target materials, reactive gases, and process control tools, to achieve optimal thin-film deposition results.
Summary Table:
Aspect | Details |
---|---|
Definition | Thin-film deposition using a reactive gas to form compound films. |
Key Components | Target material, reactive gas (e.g., oxygen, nitrogen), inert gas, substrate. |
Mechanism | Inert gas plasma sputters target atoms, which react with reactive gas ions. |
Applications | Optical coatings, barrier layers, functional films. |
Advantages | Precise control over film composition and properties. |
Challenges | Hysteresis-like behavior, requires careful parameter optimization. |
Ready to optimize your thin-film deposition process? Contact our experts today for tailored solutions!