Melting loss in an induction furnace refers to the reduction in the quantity of metal during the melting process, primarily due to factors like oxidation, evaporation, and slag formation. However, induction furnaces, particularly those using IGBT induction furnace technology, are designed to minimize these losses. They achieve this through efficient heating, controlled environments, and advanced automation. The process ensures rapid heating, reduced oxidation, and minimal contamination, making induction furnaces a cost-effective and efficient solution for metal melting.
Key Points Explained:
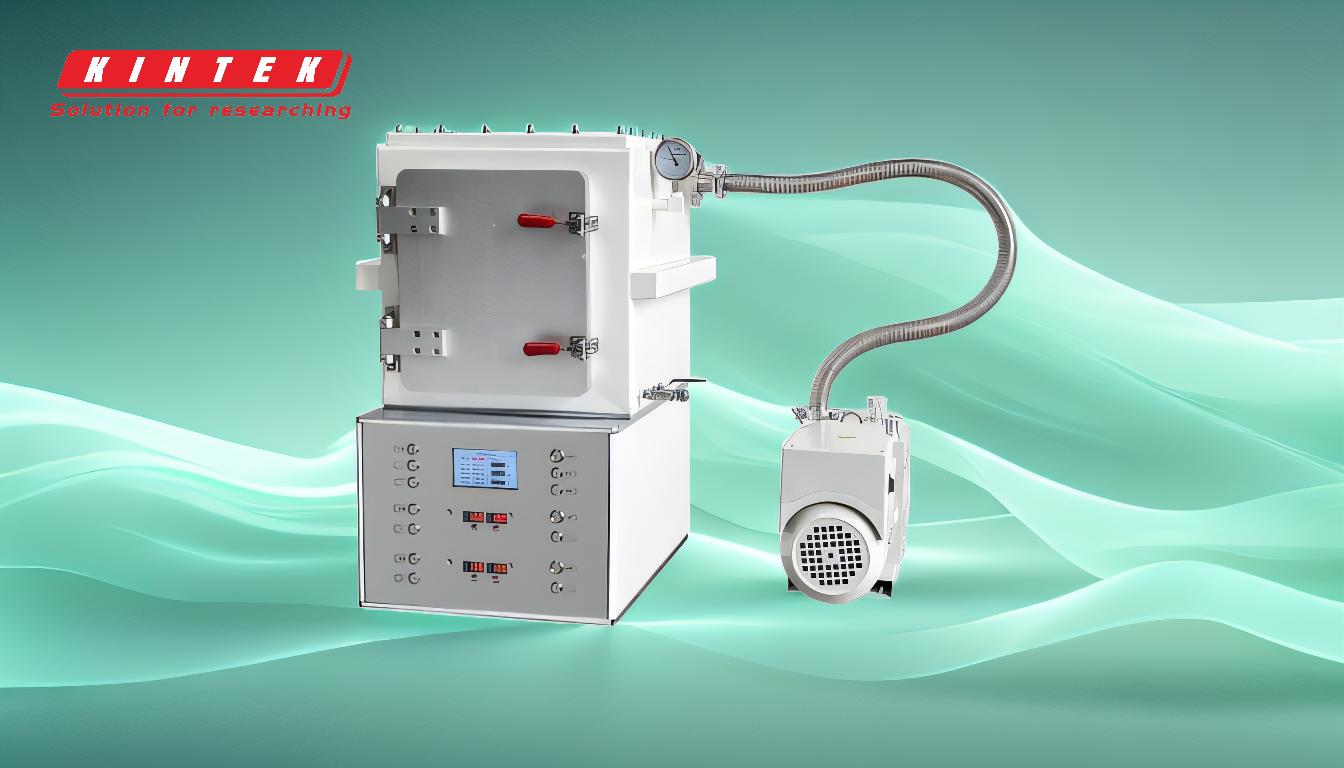
-
What is Melting Loss?
- Melting loss refers to the reduction in the quantity of metal during the melting process. This can occur due to oxidation, evaporation, or the formation of slag. In traditional melting methods, such as those using electrical furnaces, these losses can be significant due to prolonged exposure to high temperatures and contaminants like carbon rods.
-
How Induction Furnaces Minimize Melting Loss:
- Induction furnaces, especially those using IGBT induction furnace technology, are designed to minimize melting loss. They achieve this through:
- Rapid Heating: The use of high-frequency currents ensures that the metal heats up quickly, reducing the time it is exposed to high temperatures and minimizing oxidation.
- Controlled Environment: The heavy-gauge hollow copper pipe coil with double insulation and cold water circulation prevents overheating and maintains a stable temperature, further reducing oxidation and evaporation.
- No Carbon Rods: Unlike traditional methods, induction furnaces do not require carbon rods, which can cause contamination and additional metal loss.
- Induction furnaces, especially those using IGBT induction furnace technology, are designed to minimize melting loss. They achieve this through:
-
Factors Influencing Melting Loss:
- Several factors can influence the extent of melting loss in any furnace, including:
- Temperature: Higher temperatures can increase the rate of oxidation and evaporation.
- Pressure: The pressure within the furnace can affect the rate of metal loss.
- Impurities and Slags: The presence of impurities can lead to the formation of slag, which can trap some of the metal, leading to loss.
- Oxidants: The presence of oxidants can accelerate the oxidation process, leading to greater metal loss.
- Several factors can influence the extent of melting loss in any furnace, including:
-
Advantages of Induction Furnaces in Reducing Melting Loss:
- Efficiency: Induction furnaces are highly efficient, with rapid heating and cooling cycles that reduce the time the metal is exposed to high temperatures.
- Purity: Automatic stirring ensures that the metal remains pure and free from contaminants, reducing the formation of slag and other waste products.
- Cost-Effectiveness: By reducing power consumption and minimizing waste products, induction furnaces lower the overall cost of operation.
-
Comparison with Traditional Methods:
- Traditional melting methods, such as those using electrical furnaces, often result in higher melting losses due to prolonged exposure to high temperatures and the use of carbon rods. Induction furnaces, on the other hand, offer a more controlled environment, reducing these losses significantly.
In summary, melting loss in an induction furnace, particularly those using IGBT induction furnace technology, is significantly lower compared to traditional methods. The rapid heating, controlled environment, and absence of contaminants like carbon rods ensure that the metal remains pure and the losses are minimized. This makes induction furnaces a preferred choice for industries looking to reduce costs and improve efficiency in metal melting processes.
Summary Table:
Key Aspect | Details |
---|---|
What is Melting Loss? | Reduction in metal quantity due to oxidation, evaporation, or slag formation. |
How Induction Furnaces Help | Rapid heating, controlled environments, and no carbon rods minimize losses. |
Factors Influencing Loss | Temperature, pressure, impurities, and oxidants affect melting loss. |
Advantages | Efficiency, purity, and cost-effectiveness in reducing melting loss. |
Comparison with Traditional Methods | Induction furnaces offer lower losses than electrical furnaces. |
Learn how induction furnaces can optimize your metal melting process—contact our experts today!