The particle size achieved in a ball mill depends on several factors, including the initial particle size of the material, the size and type of grinding medium (balls), the grinding time, and operational parameters such as rotation speed and filling ratio. Typically, ball mills are used to reduce particle sizes to the range of 1–20 μm, with smaller balls and longer grinding times yielding finer particles. The final particle size is influenced by the grinding cycles, residence time, and specific operational conditions of the mill.
Key Points Explained:
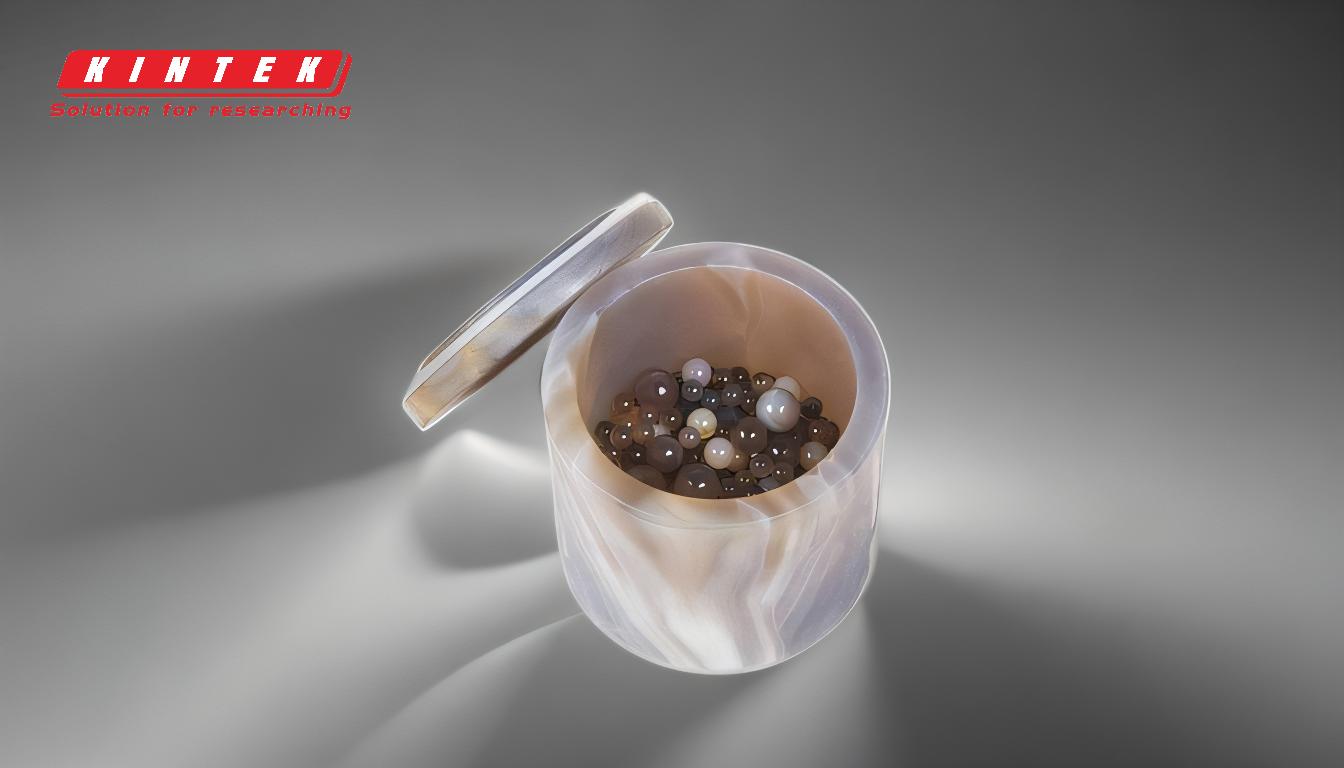
-
Typical Particle Size Range in Ball Mills:
- Ball mills are commonly used to achieve particle sizes in the range of 1–20 μm, particularly in ceramic laboratories and ore comminution processes.
- The initial average particle size (d50) of the material being ground plays a significant role in determining the final particle size.
-
Factors Influencing Particle Size:
- Grinding Medium (Balls): Smaller balls are more effective at producing finer particles. The size, density, and number of balls directly impact the grinding efficiency.
- Grinding Time: Longer grinding times generally result in smaller particle sizes, as the material is subjected to more collisions and abrasion.
- Residence Time: The time the material spends in the mill chamber affects the degree of size reduction. Longer residence times allow for more thorough grinding.
- Rotation Speed: The speed at which the mill rotates influences the energy imparted to the grinding medium and the material. Higher speeds can enhance grinding efficiency but must be optimized to avoid excessive wear or overheating.
- Filling Ratio: The percentage of the mill volume filled with grinding medium (balls) affects the grinding performance. An optimal filling ratio ensures efficient grinding without overloading the mill.
-
Operational Parameters:
- Drum Dimensions: The diameter and length of the drum, as well as the ratio of drum diameter to length (optimal L:D ratio is 1.56–1.64), influence the grinding efficiency.
- Feed Rate and Level: The rate at which material is fed into the mill and the level of material in the vessel can affect the grinding process. Consistent feed rates help maintain optimal grinding conditions.
- Material Properties: The hardness and physical-chemical properties of the material being ground play a role in determining the grinding efficiency and final particle size.
-
Optimization for Specific Applications:
- In industrial applications, optimizing ball mill parameters is crucial for achieving the desired particle size distribution. This includes selecting the appropriate ball size, adjusting rotation speed, and controlling the filling ratio.
- For ceramic applications, achieving a thoroughly mixed state of starting powders with a specific particle size range is often the goal.
-
Practical Considerations:
- Grinding Cycles: The number of grinding cycles and the residence time inside the mill determine the degree of size reduction. Multiple cycles may be required to achieve the desired fineness.
- Timely Removal of Ground Product: Efficient removal of the ground material from the mill prevents over-grinding and ensures consistent particle size distribution.
By carefully controlling these factors, operators can achieve the desired particle size in ball milling processes, whether for industrial ore comminution or ceramic powder preparation.
Summary Table:
Factor | Impact on Particle Size |
---|---|
Grinding Medium (Balls) | Smaller balls produce finer particles; size, density, and number affect grinding efficiency. |
Grinding Time | Longer grinding times yield smaller particles due to increased collisions and abrasion. |
Rotation Speed | Higher speeds enhance grinding efficiency but must be optimized to avoid wear or overheating. |
Filling Ratio | Optimal filling ratio ensures efficient grinding without overloading the mill. |
Drum Dimensions | Diameter, length, and L:D ratio influence grinding efficiency. |
Material Properties | Hardness and physical-chemical properties affect grinding efficiency and final particle size. |
Optimize your ball milling process for precise particle size—contact our experts today!