The pressure in a pyrolysis reactor is a critical parameter that influences the efficiency and outcomes of the pyrolysis process. While the provided references do not explicitly state the exact pressure values, they highlight the interdependence of pressure with other factors such as temperature, residence time, and reactor type. Pyrolysis reactors typically operate under controlled atmospheric conditions, often at or near atmospheric pressure, to ensure optimal thermal decomposition of materials. However, the pressure can vary depending on the reactor design and the specific requirements of the process, such as the need to enhance gas production or optimize the yield of pyrolysis oil. Understanding the interplay between pressure and other variables is essential for achieving desired pyrolysis outcomes.
Key Points Explained:
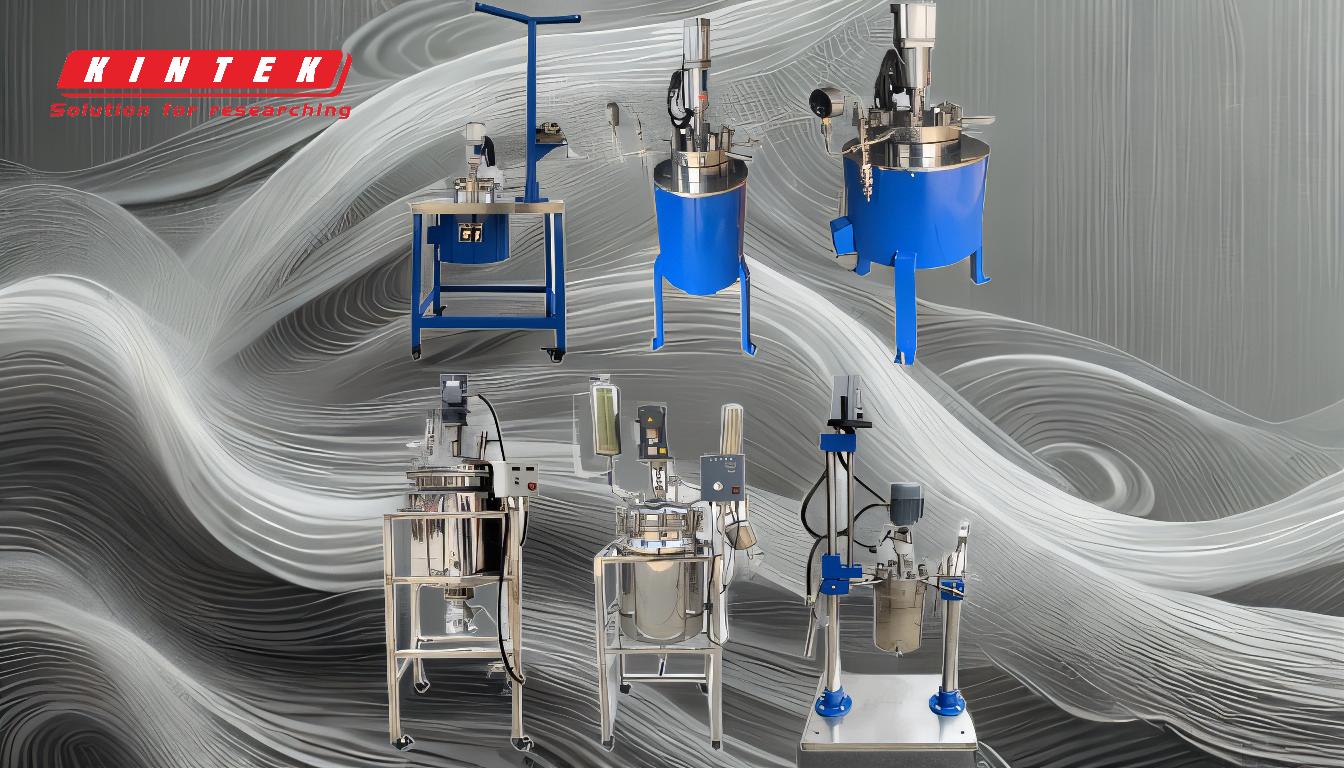
-
Pressure in Pyrolysis Reactors:
- Pyrolysis reactors often operate at or near atmospheric pressure to facilitate thermal decomposition of materials.
- The pressure is carefully controlled to ensure efficient breakdown of waste materials into valuable products like pyrolysis oil, carbon black, and syn-gas.
- While the references do not specify exact pressure values, the process is typically designed to maintain a stable environment conducive to high-temperature reactions.
-
Interdependence of Pressure with Other Factors:
- Temperature: Higher temperatures (350-400°C) are necessary for effective pyrolysis, and pressure must be managed to support these thermal conditions.
- Residence Time: The duration materials spend in the reactor affects thermal conversion, and pressure adjustments may be needed to optimize this parameter.
- Reactor Type: Different reactor designs (e.g., tubular, rotary-kiln, semi-batch) may require specific pressure settings to achieve desired outcomes.
-
Role of Pressure in Product Yield:
- Higher pressures can influence the composition of pyrolysis products, potentially increasing the production of non-condensable gases.
- Lower pressures may favor the formation of high-quality solid products, such as carbon black.
- The pressure must be balanced with other factors to achieve the desired balance of gas, liquid, and solid outputs.
-
Reactor Design and Pressure Management:
- Tubular Reactors: Efficiency is influenced by flow velocity and heat supply, which may require pressure adjustments to maintain optimal conditions.
- Rotary-Kiln Reactors: The speed of rotation and heat supply are key factors, and pressure control ensures consistent thermal decomposition.
- Semi-Batch Reactors: Carrier gas flow rate and heating rate are critical, and pressure must be managed to support these variables.
-
Practical Considerations for Pressure Control:
- Atmospheric Pressure Operation: Many pyrolysis reactors operate at or near atmospheric pressure to simplify design and operation.
- Closed System Operation: Reactors often function as closed systems, relying on thermodynamic principles to maintain stable pressure conditions.
- Pressure Adjustments: In some cases, slight pressure adjustments may be necessary to optimize the process for specific feedstocks or desired outputs.
-
Impact of Feedstock Characteristics on Pressure:
- The composition, particle size, and physical structure of the feedstock can influence pressure requirements.
- Smaller particle sizes may require adjustments in pressure to ensure uniform thermal decomposition.
- Different biomass components decompose at varying temperatures, necessitating careful pressure management to achieve consistent results.
In summary, while the exact pressure in a pyrolysis reactor is not explicitly detailed in the references, it is clear that pressure is a critical variable that interacts with temperature, residence time, and reactor design to influence the efficiency and outcomes of the pyrolysis process. Proper pressure management is essential for optimizing product yields and ensuring the effective thermal decomposition of materials.
Summary Table:
Key Factors | Impact on Pyrolysis |
---|---|
Pressure | Influences product yield (gas, liquid, solid) and thermal decomposition efficiency. |
Temperature | Higher temperatures (350-400°C) require pressure adjustments for optimal performance. |
Residence Time | Duration in reactor affects thermal conversion; pressure may need optimization. |
Reactor Type | Design-specific pressure settings for tubular, rotary-kiln, or semi-batch reactors. |
Feedstock Characteristics | Particle size and composition influence pressure requirements for uniform decomposition. |
Need help optimizing your pyrolysis reactor? Contact our experts today for tailored solutions!