Chemical Vapor Deposition (CVD) is a process used to deposit thin, high-quality solid films onto a substrate through chemical reactions in a controlled environment. The principle involves introducing gaseous or liquid precursors into a reaction chamber, where they decompose or react at elevated temperatures, plasma, or other energy sources. The resulting atoms or molecules bond to the substrate surface, forming a uniform, dense layer. By-products are removed via gas flow or vacuum systems. CVD is widely used in industries like semiconductors, coatings, and materials science due to its ability to produce precise, high-performance materials.
Key Points Explained:
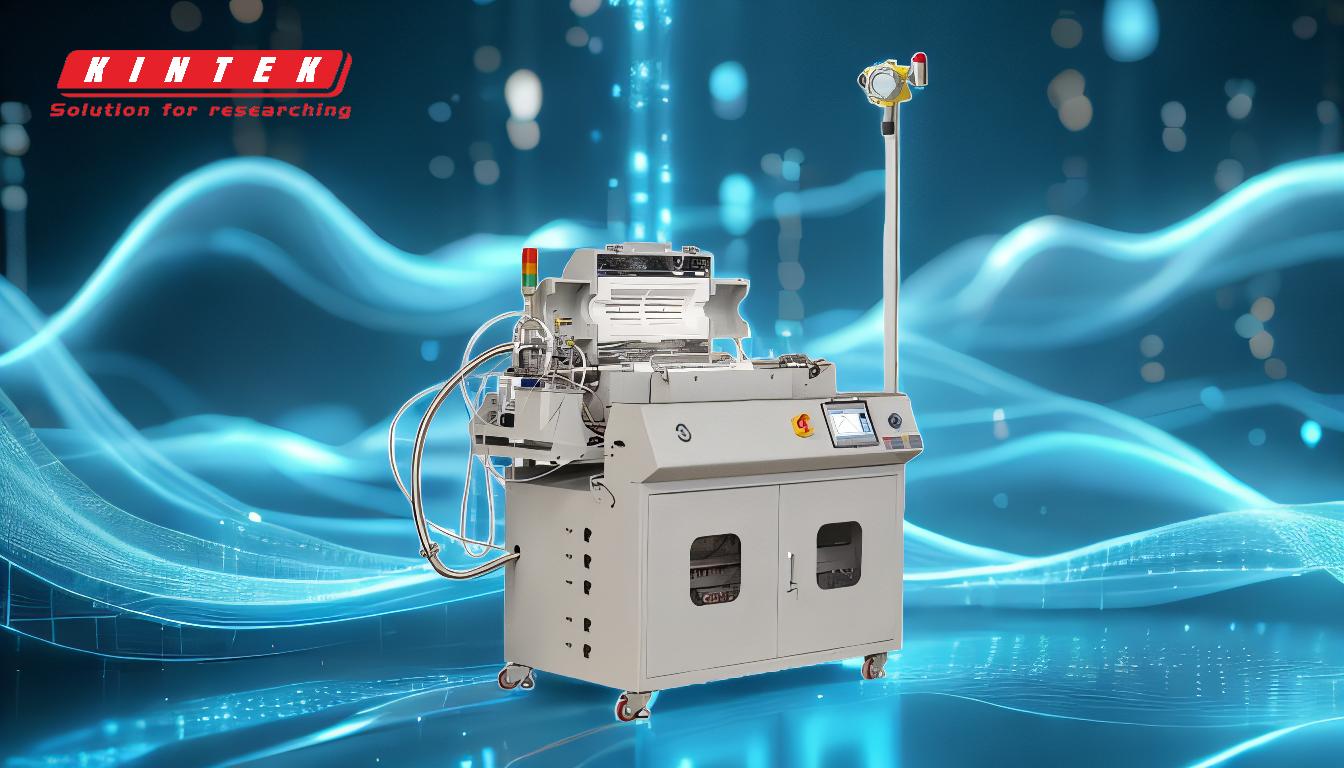
-
Introduction of Precursors:
- Gaseous or liquid reactants containing the desired film elements are introduced into a reaction chamber.
- These precursors are often volatile and can be transported easily in their vapor state.
- Example: Silicon tetrachloride (SiCl₄) for silicon deposition.
-
Chemical Reactions:
- The precursors undergo decomposition or chemical reactions on the substrate surface.
- These reactions are driven by energy sources such as heat, plasma, laser irradiation, or photochemical processes.
- Example: SiCl₄ + 2H₂ → Si + 4HCl (silicon deposition).
-
Deposition Mechanism:
- The decomposed or reacted atoms or molecules bond to the substrate, forming a thin, uniform layer.
- The process occurs in a vacuum or controlled atmosphere to ensure purity and uniformity.
- Example: Formation of a silicon film on a wafer for semiconductor applications.
-
Energy Sources:
- Thermal CVD: Uses high temperatures to drive reactions.
- Plasma-Enhanced CVD (PECVD): Uses plasma to lower the reaction temperature.
- Laser or Photochemical CVD: Uses light energy to induce reactions.
- Example: PECVD for depositing silicon nitride at lower temperatures.
-
By-Product Removal:
- Volatile by-products are formed during the reactions and are removed from the chamber.
- Gas flow or vacuum pumps are used to evacuate these by-products.
- Example: Removal of HCl gas in silicon deposition.
-
Applications:
- Semiconductor manufacturing: Deposition of silicon, silicon dioxide, and other materials.
- Protective coatings: Deposition of wear-resistant or corrosion-resistant layers.
- Advanced materials: Production of graphene, carbon nanotubes, and other nanomaterials.
- Example: CVD diamond coatings for cutting tools.
-
Advantages of CVD:
- High-quality, uniform films with precise control over thickness and composition.
- Ability to deposit a wide range of materials, including metals, ceramics, and polymers.
- Suitable for complex geometries and large-area substrates.
- Example: CVD for creating intricate patterns in microelectronics.
-
Challenges and Considerations:
- High temperatures and energy requirements can limit substrate choices.
- Precursor toxicity and by-product handling require careful safety measures.
- Process optimization is needed to balance deposition rate, film quality, and cost.
- Example: Managing the toxicity of precursors like silane (SiH₄) in semiconductor manufacturing.
By understanding these key points, equipment and consumable purchasers can better evaluate CVD systems, precursors, and related materials for their specific applications, ensuring optimal performance and cost-effectiveness.
Summary Table:
Key Aspect | Details |
---|---|
Process | Deposits thin, high-quality solid films via chemical reactions. |
Precursors | Gaseous or liquid reactants introduced into a reaction chamber. |
Energy Sources | Heat, plasma, laser, or photochemical processes drive reactions. |
Applications | Semiconductors, protective coatings, advanced materials like graphene. |
Advantages | High-quality, uniform films; wide material range; complex geometries. |
Challenges | High temperatures, precursor toxicity, and process optimization required. |
Discover how CVD can revolutionize your production process—contact our experts today!