Magnetron sputtering is a widely used physical vapor deposition (PVD) technique for depositing thin films onto substrates. The process involves the creation of a plasma in a low-pressure environment, where argon gas is ionized, and the resulting ions are accelerated toward a target material. The target material is then sputtered, ejecting atoms that deposit onto a substrate to form a thin film. The process is enhanced by the use of magnetic fields, which confine the plasma near the target surface, increasing the sputtering rate and efficiency. This method is versatile, allowing for the deposition of a wide range of materials, including metals, semiconductors, and insulators, with precise control over film properties.
Key Points Explained:
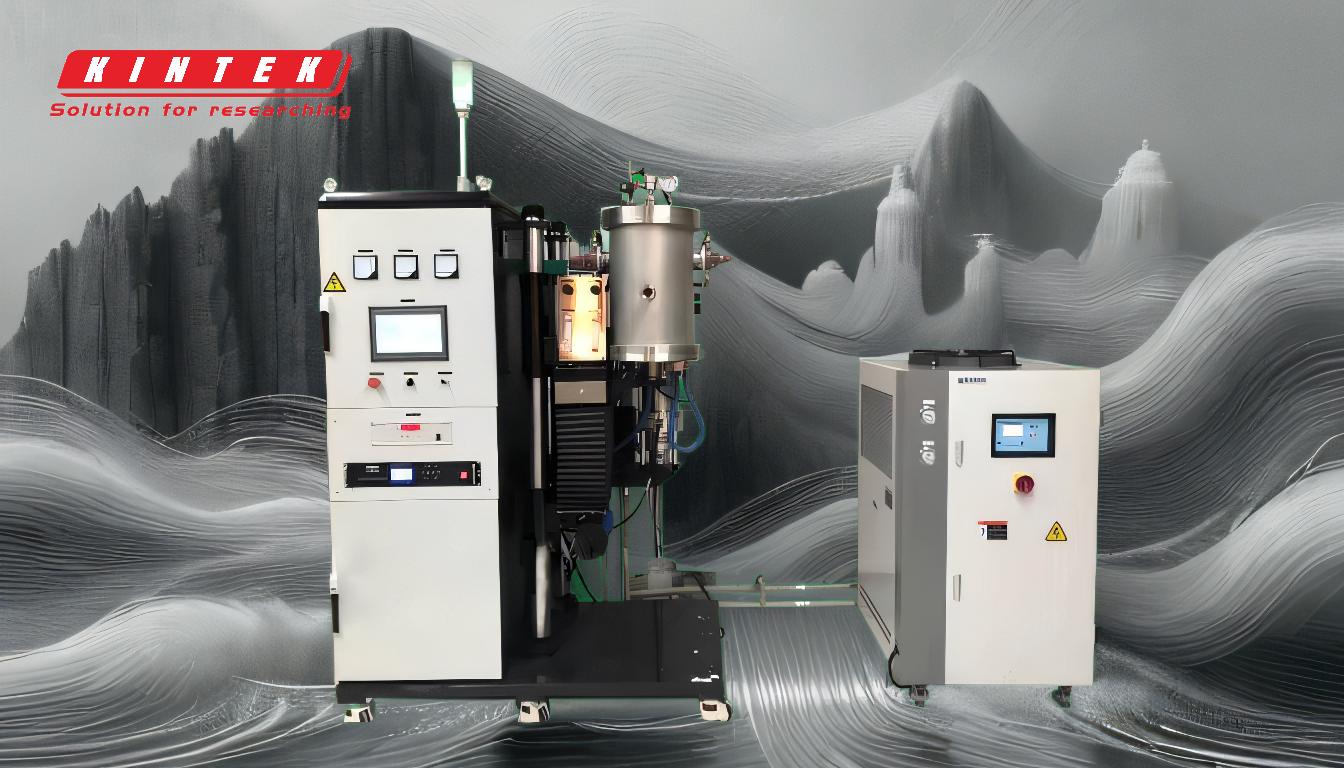
-
Principle of Magnetron Sputtering:
- Magnetron sputtering involves the use of a magnetic field to enhance the sputtering process. The magnetic field traps electrons near the target surface, increasing the ionization of the argon gas and thus the density of the plasma. This results in a higher sputtering rate and more efficient deposition of the target material onto the substrate.
-
Key Components:
- Substrate Holder: Holds the substrate where the thin film will be deposited.
- Load Lock Chamber: Allows for the introduction and removal of substrates without breaking the vacuum.
- Deposition Chamber: The main chamber where the sputtering process occurs.
- Sputter Gun with Target Material: Contains the material to be sputtered.
- Strong Magnets: Create the magnetic field necessary to confine the plasma.
- Argon Gas Flow System: Supplies the inert gas needed to create the plasma.
-
Process Steps:
- Gas Introduction: Argon gas is introduced into the chamber.
- Plasma Creation: A high voltage is applied, creating a plasma of argon ions and free electrons.
- Ion Bombardment: The negatively charged target attracts the positively charged argon ions, which bombard the target, ejecting atoms.
- Film Deposition: The ejected atoms travel through the chamber and deposit onto the substrate, forming a thin film.
-
Types of Magnetron Sputtering:
- DC Magnetron Sputtering: Uses a direct current power supply, suitable for conductive materials.
- Pulsed DC Sputtering: Alternates the polarity of the power supply, reducing arcing and allowing for the deposition of insulating materials.
- RF Magnetron Sputtering: Uses a radio frequency power supply, suitable for both conductive and insulating materials.
-
Key Parameters:
- Magnetic Field Strength: Influences the confinement of the plasma and the sputtering rate.
- Gas Flow Rate and Pressure: Affects the density of the plasma and the uniformity of the film.
- Power Supply Voltage and Frequency: Determines the energy of the ions and the stability of the plasma.
- Substrate Temperature: Can influence the microstructure and properties of the deposited film.
- Deposition Rate: Controlled by the power density and gas pressure, affects the thickness and quality of the film.
-
Advantages of Magnetron Sputtering:
- High Deposition Rates: The magnetic field increases the plasma density, leading to faster deposition.
- Versatility: Can deposit a wide range of materials, including metals, semiconductors, and insulators.
- Precision: Allows for precise control over film thickness and properties.
- Efficiency: The use of magnetic fields reduces the need for high operating pressures, making the process more energy-efficient.
-
Applications:
- Optical Coatings: Used in the production of anti-reflective and reflective coatings.
- Semiconductor Devices: Essential for the deposition of thin films in integrated circuits and solar cells.
- Decorative Coatings: Used to apply thin films for aesthetic purposes on various products.
- Wear-Resistant Coatings: Applied to tools and components to enhance durability.
In summary, magnetron sputtering is a highly efficient and versatile technique for depositing thin films with precise control over their properties. The process is enhanced by the use of magnetic fields, which increase the plasma density and sputtering rate, leading to high-quality films suitable for a wide range of applications.
Summary Table:
Aspect | Details |
---|---|
Principle | Magnetic fields confine plasma, increasing argon ionization and sputtering. |
Key Components | Substrate holder, load lock chamber, deposition chamber, sputter gun, magnets, argon gas system. |
Process Steps | Gas introduction, plasma creation, ion bombardment, film deposition. |
Types | DC, Pulsed DC, RF magnetron sputtering. |
Key Parameters | Magnetic field strength, gas flow rate, power supply, substrate temperature, deposition rate. |
Advantages | High deposition rates, versatility, precision, energy efficiency. |
Applications | Optical coatings, semiconductor devices, decorative coatings, wear-resistant coatings. |
Unlock the potential of magnetron sputtering for your applications—contact our experts today!