Thin film preparation involves the deposition of a thin layer of material onto a substrate, which can be achieved through various chemical, physical, and electrically-based methods. The process typically includes selecting the target material, transporting it to the substrate, and depositing it to form a thin film. Post-deposition processes like annealing or heat treatment may also be applied. The choice of deposition method depends on the desired film properties, application, and industry requirements. Common techniques include Physical Vapor Deposition (PVD), Chemical Vapor Deposition (CVD), Atomic Layer Deposition (ALD), and Spray Pyrolysis, among others. These methods allow for precise control over film thickness and composition, enabling the creation of films with specific properties for applications ranging from semiconductors to flexible electronics.
Key Points Explained:
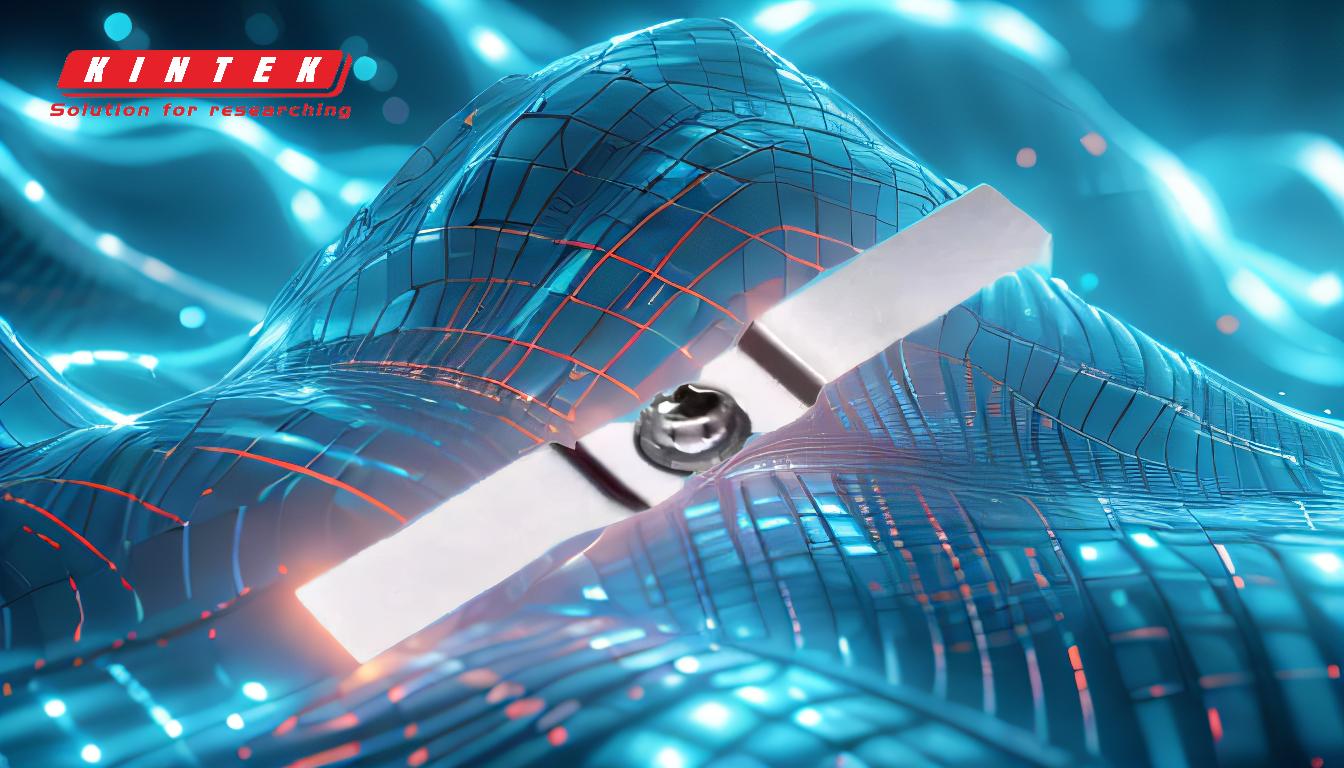
-
Selection of Target Material:
- The first step in thin film preparation is selecting the material to be deposited, known as the target. This material determines the properties of the thin film, such as conductivity, optical properties, and mechanical strength. The choice of material is crucial and depends on the intended application, whether it be for semiconductors, solar cells, or OLEDs.
-
Transport of Target to Substrate:
- Once the target material is selected, it needs to be transported to the substrate. This can be achieved through various mechanisms depending on the deposition method. For example, in Physical Vapor Deposition (PVD), the target material is evaporated or sputtered, and the resulting vapor is transported to the substrate. In Chemical Vapor Deposition (CVD), the target material is transported in the form of a gas or vapor that reacts on the substrate surface.
-
Deposition of Target onto Substrate:
- The deposition process involves the actual formation of the thin film on the substrate. This can be done through several techniques:
- Physical Vapor Deposition (PVD): Includes methods like sputtering and thermal evaporation, where the target material is physically transformed into a vapor and then condensed onto the substrate.
- Chemical Vapor Deposition (CVD): Involves chemical reactions that occur on the substrate surface to deposit the thin film.
- Atomic Layer Deposition (ALD): Deposits the film one atomic layer at a time, allowing for extremely precise control over film thickness and uniformity.
- Spray Pyrolysis: Involves spraying a solution of the target material onto the substrate, followed by thermal decomposition to form the thin film.
- The deposition process involves the actual formation of the thin film on the substrate. This can be done through several techniques:
-
Post-Deposition Processes:
- After the thin film is deposited, it may undergo additional processes to improve its properties. These processes include:
- Annealing: Heating the film to relieve internal stresses and improve crystallinity.
- Heat Treatment: Used to modify the film's microstructure, enhancing its mechanical, electrical, or optical properties.
- After the thin film is deposited, it may undergo additional processes to improve its properties. These processes include:
-
Deposition Methods:
- Thin films can be deposited using a variety of methods, broadly categorized into chemical and physical deposition techniques:
- Chemical Methods: Include electroplating, sol-gel, dip coating, spin coating, CVD, PECVD, and ALD. These methods rely on chemical reactions to form the thin film.
- Physical Methods: Primarily involve PVD techniques such as sputtering, thermal evaporation, electron beam evaporation, MBE, and PLD. These methods use physical processes to deposit the film.
- Thin films can be deposited using a variety of methods, broadly categorized into chemical and physical deposition techniques:
-
Applications and Industry-Specific Techniques:
- The choice of thin film deposition technique often depends on the specific application and industry requirements. For example:
- Semiconductors: Commonly use CVD and PVD techniques like sputtering and MBE.
- Flexible Electronics: May employ techniques like spin coating and ALD to create thin films of polymer compounds.
- Solar Cells: Utilize methods such as spray pyrolysis and PECVD to deposit thin films with specific optical and electrical properties.
- The choice of thin film deposition technique often depends on the specific application and industry requirements. For example:
-
Control Over Film Properties:
- One of the key advantages of thin film deposition techniques is the ability to precisely control the thickness and composition of the film. This control is essential for applications where the film's properties must be tightly regulated, such as in microelectronics, where even a few nanometers of variation can significantly impact device performance.
In summary, the principle of thin film preparation involves a series of carefully controlled steps, from material selection to deposition and post-processing. The choice of deposition method and subsequent treatments are tailored to achieve the desired film properties for specific applications, making thin film technology a versatile and essential tool in modern manufacturing and research.
Summary Table:
Key Aspect | Details |
---|---|
Target Material Selection | Determines film properties like conductivity, optical, and mechanical strength. |
Transport to Substrate | Achieved via evaporation, sputtering, or gas/vapor transport depending on method. |
Deposition Techniques | Includes PVD (sputtering, evaporation), CVD, ALD, and spray pyrolysis. |
Post-Deposition Processes | Annealing and heat treatment to enhance film properties. |
Applications | Semiconductors, flexible electronics, solar cells, and more. |
Discover how thin film technology can revolutionize your projects—contact our experts today!