Calendering in plastic processing is a high-volume manufacturing technique used to produce plastic films and sheets, primarily for materials like PVC and other modified thermoplastics. The process involves melting the polymer in an extruder, then passing it through a series of heated rollers (calendering rolls) under controlled heat and pressure to form uniform sheets or films. This method ensures high-quality, consistent thickness and smooth surfaces, making it ideal for applications requiring precision and durability. Additionally, calendering machines can also be used in rubber processing to combine rubber sheets with other materials or fabrics, enhancing their properties for specific applications.
Key Points Explained:
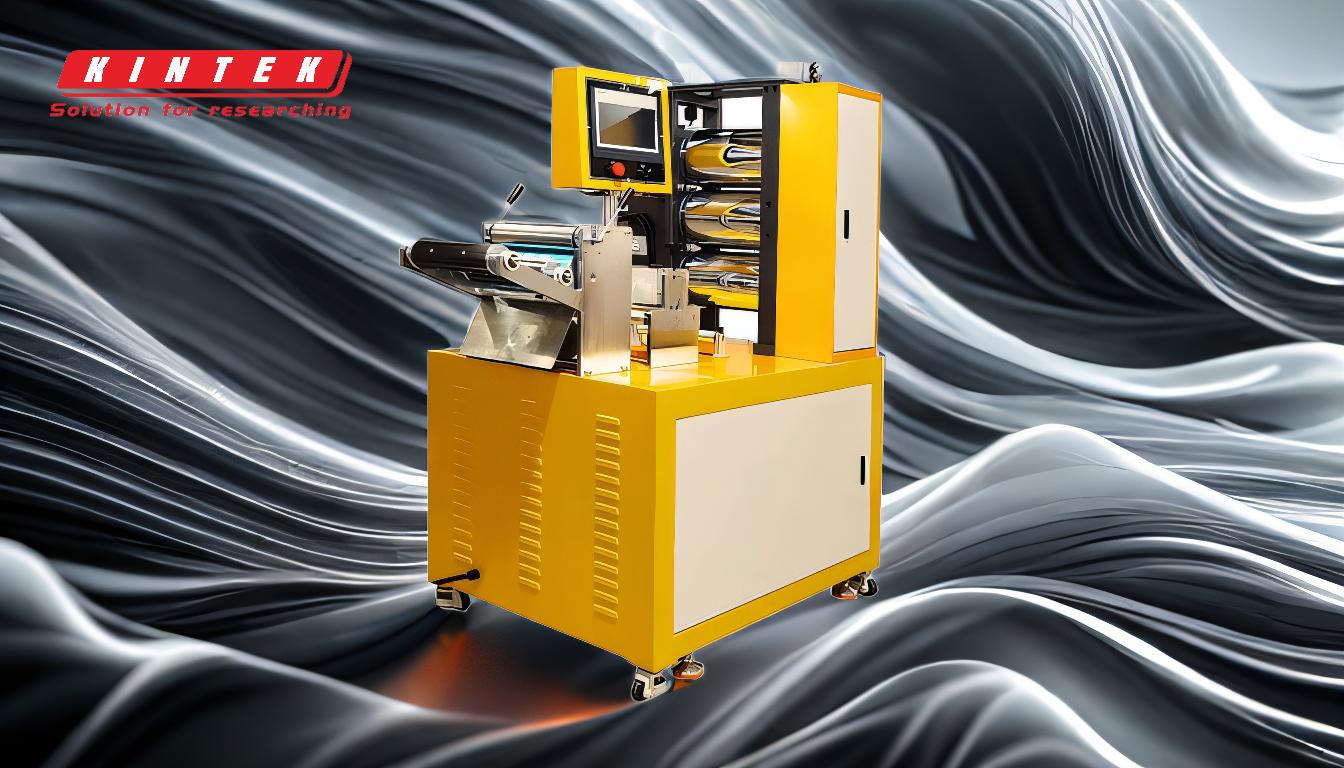
-
Definition and Purpose of Calendering:
- Calendering is a specialized manufacturing process used to produce plastic films and sheets with high precision and consistency.
- It is primarily employed for materials like PVC and certain modified thermoplastics, ensuring high-volume production with excellent quality.
-
Process Overview:
- The polymer is first melted in an extruder, where it is heated to a specific temperature to achieve a molten state.
- The molten polymer is then fed into a series of heated rollers, known as calendering rolls, which apply controlled heat and pressure to shape the material into a uniform sheet or film.
-
Calendering Rolls:
- The calendering rolls are the core component of the process, consisting of multiple horizontal rollers arranged in a specific configuration.
- These rollers are heated to precise temperatures and are adjustable to control the thickness and surface finish of the final product.
- The number of rolls can vary depending on the desired product specifications, with common configurations including 3-roll, 4-roll, and 5-roll systems.
-
Heat and Pressure Control:
- The application of heat and pressure is critical to the calendering process, as it ensures the polymer is evenly distributed and properly formed.
- The temperature of the rolls is carefully controlled to maintain the polymer in a pliable state, allowing it to flow smoothly through the rollers without degrading.
- Pressure is applied to achieve the desired thickness and surface smoothness, with adjustments made based on the specific material and product requirements.
-
Applications of Calendered Products:
- Calendered plastic films and sheets are widely used in various industries, including packaging, automotive, construction, and medical applications.
- The process is particularly valued for producing materials with consistent thickness, smooth surfaces, and excellent mechanical properties.
-
Calendering in Rubber Processing:
- In addition to plastic processing, calendering machines are also used in the rubber industry to produce rubber sheets and combine them with other materials or fabrics.
- Processes such as frictioning or combining involve passing rubber material through horizontal rollers to create composite materials with enhanced properties, such as increased strength or flexibility.
-
Advantages of Calendering:
- High production rates: Calendering allows for continuous, high-volume production of plastic films and sheets.
- Consistent quality: The process ensures uniform thickness and smooth surfaces, reducing the need for additional finishing steps.
- Versatility: Calendering can be used with a variety of materials, including PVC and modified thermoplastics, as well as rubber.
-
Challenges and Considerations:
- Material selection: The choice of polymer and additives must be carefully considered to ensure compatibility with the calendering process.
- Equipment maintenance: Regular maintenance of the calendering rolls and other components is essential to maintain consistent product quality and prevent downtime.
- Process optimization: Achieving the desired product specifications requires precise control of temperature, pressure, and roll alignment, which can be complex and require expertise.
By understanding the calendering process in plastic processing, manufacturers can produce high-quality films and sheets efficiently, meeting the demands of various industries while maintaining cost-effectiveness and consistency.
Summary Table:
Key Aspect | Details |
---|---|
Definition | A high-volume manufacturing process for producing plastic films and sheets. |
Materials Used | PVC, modified thermoplastics, and rubber. |
Process Overview | Polymer is melted, then shaped using heated rollers under controlled conditions. |
Applications | Packaging, automotive, construction, and medical industries. |
Advantages | High production rates, consistent quality, and material versatility. |
Challenges | Material selection, equipment maintenance, and process optimization. |
Discover how calendering can optimize your production process—contact our experts today for tailored solutions!