Chemical vapor deposition (CVD) is a sophisticated process used to deposit thin films of material onto a substrate through chemical reactions in the vapor phase. It involves several key steps, including the vaporization of a precursor material, its transport to the substrate, and subsequent chemical reactions that result in the formation of a solid film. This process is widely used in industries such as semiconductor manufacturing, nanotechnology, and coatings due to its ability to produce high-quality, uniform layers with precise control over thickness and composition. CVD is particularly valued for its versatility, enabling the deposition of a wide range of materials, including metals, ceramics, and polymers, under controlled conditions.
Key Points Explained:
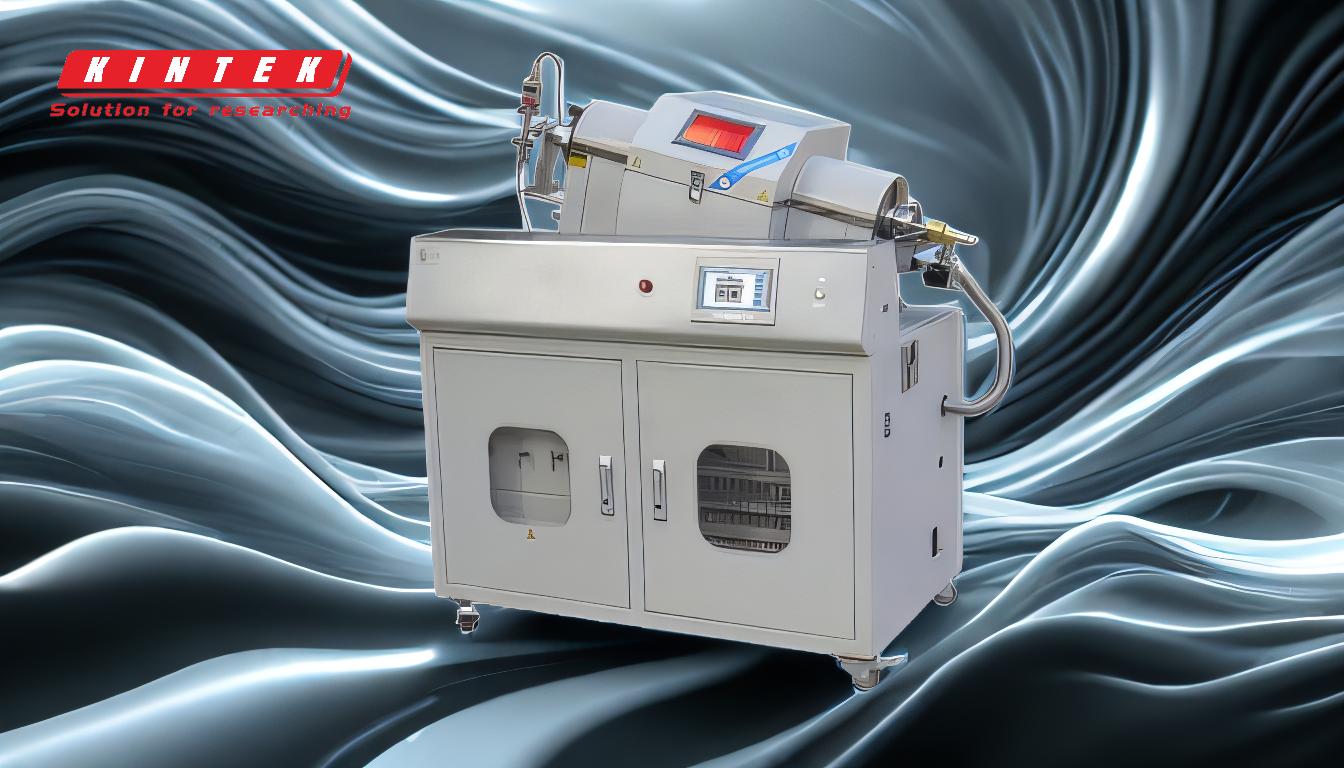
-
Vaporization of Precursor Material:
- The process begins with the evaporation of a volatile compound containing the material to be deposited. This precursor is typically in a liquid or solid state and is heated to produce a vapor.
- The vaporized precursor is then transported to the substrate, often in a carrier gas, which ensures uniform distribution and controlled delivery.
-
Transport of Gaseous Species to the Substrate:
- The gaseous precursor is directed toward the substrate, where it interacts with the surface. This step is critical for ensuring that the precursor reaches the substrate uniformly.
- The transport process is influenced by factors such as pressure, temperature, and flow dynamics within the reaction chamber.
-
Adsorption and Surface Reactions:
- Once the precursor reaches the substrate, it adsorbs onto the surface. Adsorption is the process by which molecules adhere to the surface, forming a thin layer.
- Surface-catalyzed reactions then occur, where the adsorbed molecules decompose or react with other gases, vapors, or liquids present in the environment. These reactions are often heterogeneous, meaning they occur at the interface between the gas and the solid substrate.
-
Nucleation and Film Growth:
- The decomposed or reacted species diffuse across the substrate surface to growth sites, where they nucleate and form the initial layers of the film.
- As more material is deposited, the film grows in thickness, forming a continuous and uniform layer. The growth rate and film properties depend on factors such as temperature, pressure, and the nature of the precursor.
-
Desorption and Removal of Byproducts:
- After the film has formed, any gaseous byproducts of the reaction desorb from the surface and are transported away from the substrate.
- This step ensures that the deposited film remains pure and free from contaminants, which is essential for achieving high-quality coatings.
-
Applications of CVD:
- CVD is widely used in the semiconductor industry to deposit thin films of materials such as silicon dioxide, silicon nitride, and various metals.
- It is also employed in the production of carbon nanotubes, graphene, and other nanomaterials, which have applications in electronics, energy storage, and advanced composites.
- Additionally, CVD is used to apply protective coatings, such as those on cutting tools, and to create magnetic coatings for data storage devices.
-
Advantages of CVD:
- CVD offers excellent control over film thickness, composition, and uniformity, making it suitable for producing high-quality coatings.
- The process can be performed at relatively low temperatures compared to other deposition methods, reducing the risk of thermal damage to the substrate.
- CVD is highly versatile, capable of depositing a wide range of materials, including metals, ceramics, and polymers.
-
Challenges and Considerations:
- CVD requires precise control over process parameters, such as temperature, pressure, and gas flow rates, to achieve consistent results.
- The use of toxic or hazardous precursors necessitates careful handling and proper safety measures.
- The equipment used in CVD, such as vacuum chambers and gas delivery systems, can be expensive and complex to operate.
In summary, chemical vapor deposition is a highly versatile and precise process for depositing thin films of materials onto substrates. Its ability to produce high-quality, uniform coatings makes it indispensable in industries ranging from semiconductors to nanotechnology. By understanding the key steps and factors involved in CVD, manufacturers can optimize the process to meet specific application requirements.
Summary Table:
Step | Description |
---|---|
1. Vaporization of Precursor | Volatile precursor is heated to produce vapor for deposition. |
2. Transport to Substrate | Gaseous precursor is carried to the substrate via a carrier gas. |
3. Adsorption & Reactions | Precursor adsorbs onto the substrate and undergoes surface-catalyzed reactions. |
4. Nucleation & Film Growth | Reacted species form nuclei, leading to uniform film growth. |
5. Desorption of Byproducts | Gaseous byproducts are removed to ensure film purity. |
Applications | Semiconductors, nanomaterials, protective coatings, and more. |
Advantages | Precise control, low temperatures, and versatility in material deposition. |
Challenges | Requires precise parameter control and specialized equipment. |
Discover how CVD can enhance your manufacturing process—contact our experts today for tailored solutions!