Co-pyrolysis is a thermochemical process that involves the simultaneous thermal decomposition of two or more materials, typically biomass and plastic waste, in the absence of oxygen. This process combines the benefits of pyrolysis for both materials, leading to enhanced efficiency, reduced emissions, and the production of valuable byproducts such as biochar, bio-oil, and syngas. Below is a detailed explanation of the co-pyrolysis process, its key steps, and its significance.
Key Points Explained:
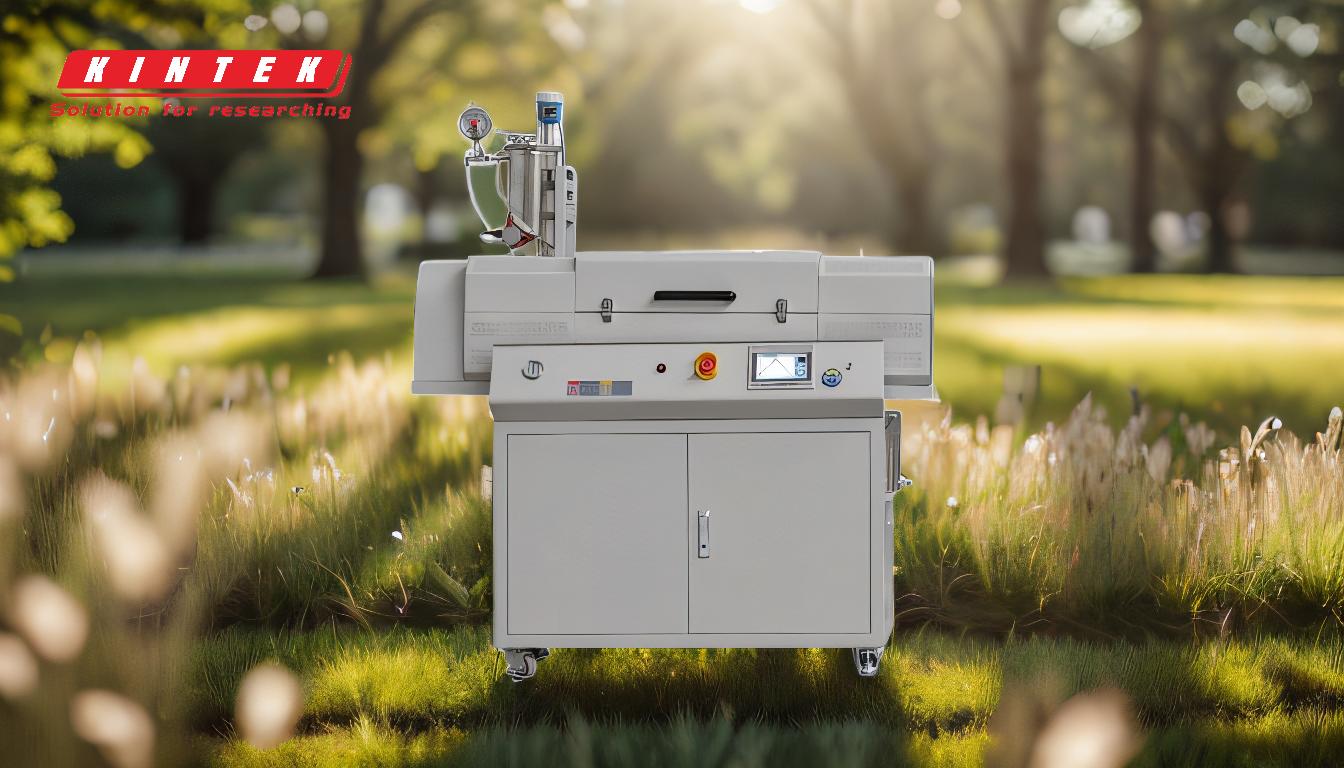
-
Pre-Treatment of Feedstocks:
- Drying and Crushing: Both biomass and plastic waste undergo pre-treatment to ensure optimal conditions for pyrolysis. Biomass is dried to remove moisture and crushed into smaller particles, while plastic waste is shredded and dried to eliminate water content.
- Impurity Removal: Non-plastic materials (e.g., metals, glass) are separated from plastic waste to prevent contamination during pyrolysis.
-
Feeding the Reactor:
- Optimal Feed Preparation: The pre-treated biomass and plastic waste are mixed in specific ratios and fed into a pyrolysis reactor. The reactor operates under low oxygen conditions to prevent combustion.
- Catalyst Addition: A catalyst may be added to enhance the pyrolysis process, improve product yield, and reduce the formation of unwanted byproducts.
-
Pyrolysis Reaction:
- Heating and Decomposition: The reactor is heated to temperatures ranging from 200°C to 900°C, depending on the feedstock and desired products. At these temperatures, the materials undergo thermal decomposition, breaking down into smaller molecules.
- Simultaneous Processing: Biomass and plastic waste decompose simultaneously, with biomass producing biochar, bio-oil, and syngas, while plastic waste yields pyrolysis oil and gases.
-
Product Separation:
- Biochar Formation: Solid biochar settles at the bottom of the reactor and is collected for use as a soil amendment or fuel.
- Condensation of Vapors: The vapors produced during pyrolysis are condensed into liquid bio-oil and pyrolysis oil. These oils can be further refined for use as fuel or chemical feedstocks.
- Syngas Recycling: Non-condensable gases, such as syngas, are recycled back into the combustion chamber to provide heat for the pyrolysis process, improving energy efficiency.
-
Post-Processing:
- Oil Refinement: The collected pyrolysis oil undergoes distillation and purification to remove impurities and improve its quality for commercial use.
- Exhaust Gas Cleaning: The exhaust gases are passed through a de-dusting system to remove particulate matter and harmful substances, ensuring compliance with environmental regulations.
-
Storage and Dispatch:
- Product Storage: The final products, including biochar, bio-oil, and refined pyrolysis oil, are stored in designated containers for dispatch or further processing.
- Environmental Benefits: Co-pyrolysis reduces the volume of waste sent to landfills, minimizes greenhouse gas emissions, and produces renewable energy sources.
Advantages of Co-Pyrolysis:
- Enhanced Efficiency: Combining biomass and plastic waste in co-pyrolysis improves the overall energy efficiency of the process.
- Waste Reduction: It addresses the growing issue of plastic waste by converting it into useful products.
- Renewable Energy Production: The process generates renewable fuels and chemicals, contributing to a circular economy.
By integrating the pyrolysis processes of biomass and plastic waste, co-pyrolysis offers a sustainable solution for waste management and energy production.
Summary Table:
Key Steps | Details |
---|---|
Pre-Treatment | Drying, crushing, and removing impurities from biomass and plastic waste. |
Feeding the Reactor | Mixing feedstocks in specific ratios and adding catalysts for efficiency. |
Pyrolysis Reaction | Heating to 200°C–900°C for thermal decomposition into biochar, oils, and gas. |
Product Separation | Collecting biochar, condensing vapors into oils, and recycling syngas. |
Post-Processing | Refining oils and cleaning exhaust gases for environmental compliance. |
Storage and Dispatch | Storing biochar, bio-oil, and refined pyrolysis oil for further use. |
Discover how co-pyrolysis can revolutionize waste management—contact us today to learn more!