E-beam coating, or electron beam coating, is a highly precise and directional process used to deposit thin layers of materials, such as metals or carbon, onto a substrate. This process involves evaporating the source material using a focused electron beam in a vacuum chamber. The evaporated particles then flow upward and bond with the substrate, forming a thin, high-purity coating typically ranging from 5 to 250 nanometers in thickness. E-beam coating is particularly useful for applications requiring ultra-thin layers, directional coating, or minimal heat and charged particle impact on the substrate. The process is widely used in industries where precision and purity are critical, such as optics, electronics, and replicas.
Key Points Explained:
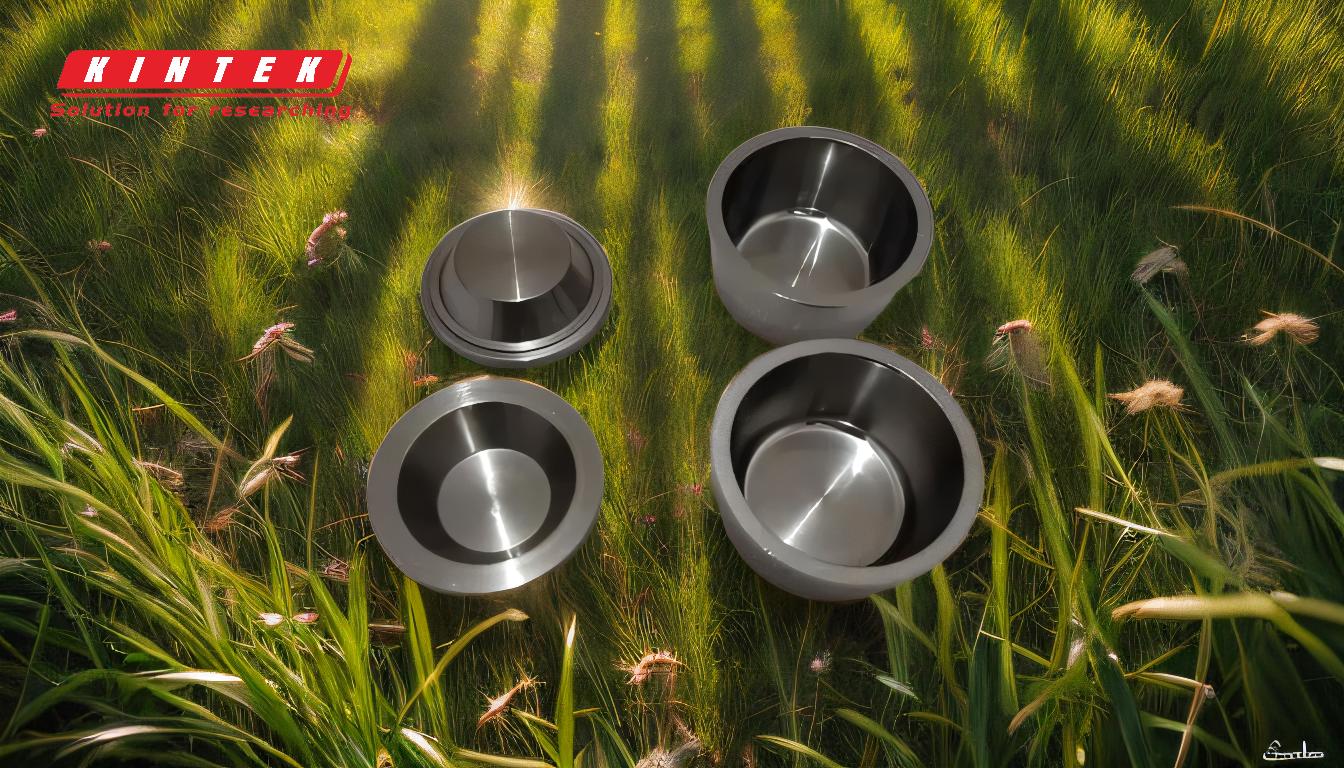
-
Overview of E-Beam Coating:
- E-beam coating is a vacuum deposition process that uses an electron beam to evaporate source materials like metals or carbon.
- The process is highly directional, allowing for precise control over the coating's thickness and placement.
- It is ideal for applications requiring ultra-thin layers (5–250 nm) or directional coating, such as shadowing and replicas.
-
Components of the E-Beam Coating System:
- Electron Beam Gun: Generates and accelerates electrons using high voltage, focusing them into a beam.
- Crucible: Holds the source material (e.g., metal or carbon) that is to be evaporated.
- Vacuum Chamber: Provides a controlled environment to minimize contamination and ensure high-purity coatings.
- Substrate: The material to be coated, positioned above the crucible to receive the evaporated particles.
-
Step-by-Step Process of E-Beam Coating:
- Preparation: The substrate and source material are prepared and placed in the vacuum chamber. The substrate is cleaned to ensure proper adhesion of the coating.
- Evaporation: The electron beam gun generates a focused beam of electrons, which is directed at the source material in the crucible. The intense heat from the electron beam melts and evaporates the source material.
- Deposition: The evaporated particles flow upward in the vacuum chamber and bond with the substrate, forming a thin, high-purity coating.
- Completion: The coated substrate is removed from the chamber, and the coating is inspected for quality and uniformity.
-
Advantages of E-Beam Coating:
- High Precision: The directional nature of the electron beam allows for precise control over the coating's thickness and placement.
- High Purity: The vacuum environment minimizes contamination, resulting in high-purity coatings.
- Minimal Heat Impact: The process generates minimal heat, reducing the risk of thermal damage to the substrate.
- Versatility: E-beam coating can be used with a wide range of materials, including metals and carbon.
-
Applications of E-Beam Coating:
- Optics: Used to create anti-reflective coatings, mirrors, and other optical components.
- Electronics: Applied in the production of semiconductors, thin-film transistors, and other electronic devices.
- Replicas and Shadowing: Ideal for applications requiring precise directional coating, such as replicas and shadowing in microscopy.
- Protective Coatings: Used to apply thin, durable coatings that protect substrates from wear, corrosion, or other environmental factors.
-
Comparison with Other Coating Processes:
- Physical/Chemical Vapor Deposition (PVD/CVD): E-beam coating is a subset of PVD, offering higher precision and directional control compared to other PVD methods like sputtering.
- Thermal Spraying: E-beam coating produces thinner and more uniform layers compared to thermal spraying, which is better suited for thicker coatings.
- Electrodeposition: E-beam coating does not require a liquid medium, making it more suitable for applications where contamination must be minimized.
-
Challenges and Limitations:
- Limited Coated Area: The directional nature of the process limits the size of the area that can be coated in a single run.
- Cost: The equipment and vacuum environment required for e-beam coating can be expensive.
- Material Limitations: While versatile, the process is not suitable for all materials, particularly those with high melting points or low vapor pressures.
By understanding the process, components, advantages, and applications of e-beam coating, purchasers can make informed decisions about whether this technology is suitable for their specific needs. Its precision, purity, and versatility make it a valuable tool in industries where high-quality coatings are essential.
Summary Table:
Aspect | Details |
---|---|
Process | Uses an electron beam to evaporate materials in a vacuum chamber. |
Coating Thickness | 5–250 nanometers, ideal for ultra-thin layers. |
Key Components | Electron beam gun, crucible, vacuum chamber, substrate. |
Advantages | High precision, high purity, minimal heat impact, versatile material use. |
Applications | Optics, electronics, replicas, protective coatings. |
Challenges | Limited coated area, high cost, material limitations. |
Interested in e-beam coating for your project? Contact our experts today to learn more!