Electron Beam Physical Vapor Deposition (EBPVD) is a specialized form of Physical Vapor Deposition (PVD) that uses an electron beam to vaporize a solid material, which then condenses onto a substrate to form a thin film. The process is highly controlled, occurring in a vacuum or low-pressure environment to minimize contamination and ensure precise deposition. EBPVD is particularly useful for creating high-quality coatings with excellent adhesion and uniformity, making it suitable for applications in aerospace, electronics, and optics. The process involves several key steps, including material vaporization, vapor transport, and condensation on the substrate, with the transition from line-of-sight to scattered deposition influenced by pressure and source-to-substrate distance.
Key Points Explained:
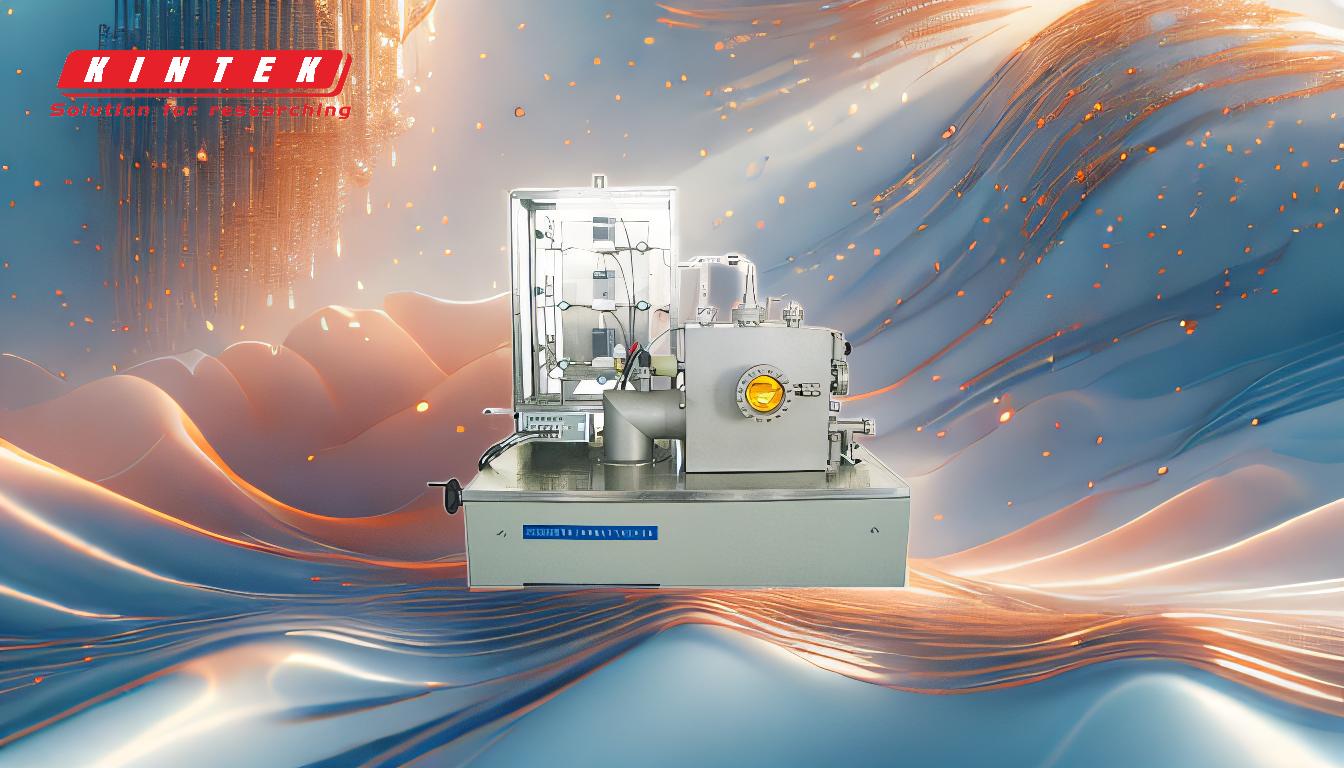
-
Material Vaporization:
- In EBPVD, a solid precursor material is vaporized using a high-energy electron beam. This beam heats the target material to extremely high temperatures, causing it to transition from a solid to a vapor phase.
- The electron beam is precisely controlled to ensure uniform vaporization, which is critical for achieving consistent film thickness and quality.
-
Vapor Transport:
- Once vaporized, the material atoms or molecules travel through a vacuum or low-pressure environment to the substrate. This environment minimizes the presence of background gases that could react with the vaporized material, ensuring a pure deposition.
- The transport process can be either line-of-sight or scattered, depending on the pressure within the chamber. At low pressures (<10^-4 Torr), the process is primarily line-of-sight, meaning the vapor travels directly from the source to the substrate. At higher pressures (≥10^-4 Torr), significant scattering occurs, allowing the vapor to coat surfaces not directly in the line of sight.
-
Condensation on Substrate:
- The vaporized material condenses onto the substrate, forming a thin film. The substrate is typically held at a controlled temperature, which can range from 50 to 600 degrees Celsius, depending on the material and desired film properties.
- The condensation process is influenced by factors such as the substrate's temperature, the angle of incidence of the vapor, and the distance between the source and the substrate. These factors determine the film's adhesion, uniformity, and microstructure.
-
Control of Film Thickness and Rate:
- The thickness and deposition rate of the film are carefully controlled using a quartz crystal rate monitor. This device measures the rate at which material is deposited onto the substrate, allowing for precise control over the film's thickness.
- The electron beam's power, the pressure within the chamber, and the substrate's temperature are all adjusted to achieve the desired deposition rate and film properties.
-
Advantages of EBPVD:
- High-Quality Coatings: EBPVD produces thin films with excellent adhesion, uniformity, and purity, making it suitable for high-performance applications.
- Versatility: The process can be used with a wide range of materials, including those with high melting points, which are difficult to deposit using other methods.
- Precision: The use of an electron beam allows for precise control over the vaporization and deposition processes, resulting in highly controlled film properties.
-
Applications of EBPVD:
- Aerospace: EBPVD is used to apply thermal barrier coatings (TBCs) on turbine blades, protecting them from high temperatures and extending their lifespan.
- Electronics: The process is used to deposit thin films in the production of semiconductors, solar cells, and other electronic components.
- Optics: EBPVD is employed to create anti-reflective coatings, mirrors, and other optical components with precise thickness and optical properties.
In summary, EBPVD is a sophisticated and versatile deposition technique that leverages the precision of electron beams to create high-quality thin films. Its ability to handle a wide range of materials and produce coatings with excellent properties makes it invaluable in industries requiring advanced material performance.
Summary Table:
Key Aspect | Description |
---|---|
Material Vaporization | Electron beam heats solid material to vaporize it, ensuring uniform vaporization. |
Vapor Transport | Vapor travels in a vacuum/low-pressure environment, minimizing contamination. |
Condensation on Substrate | Vapor condenses on substrate, forming thin films with controlled properties. |
Film Thickness Control | Quartz crystal rate monitor ensures precise thickness and deposition rate. |
Advantages | High-quality coatings, versatility, and precision. |
Applications | Aerospace (TBCs), electronics (semiconductors), and optics (anti-reflective coatings). |
Discover how EBPVD can enhance your material performance—contact us today!