Electron beam evaporation is a sophisticated physical vapor deposition (PVD) technique used to deposit thin films of materials onto substrates. The process involves heating a target material using a focused electron beam in a high-vacuum environment. The electron beam, generated by thermionic emission from a tungsten filament, is accelerated and focused onto the target material, causing it to evaporate. The vaporized material then travels through the vacuum chamber and condenses onto a substrate, forming a thin film. This method is particularly effective for materials with high melting points and is widely used in industries requiring precise and high-quality thin-film coatings.
Key Points Explained:
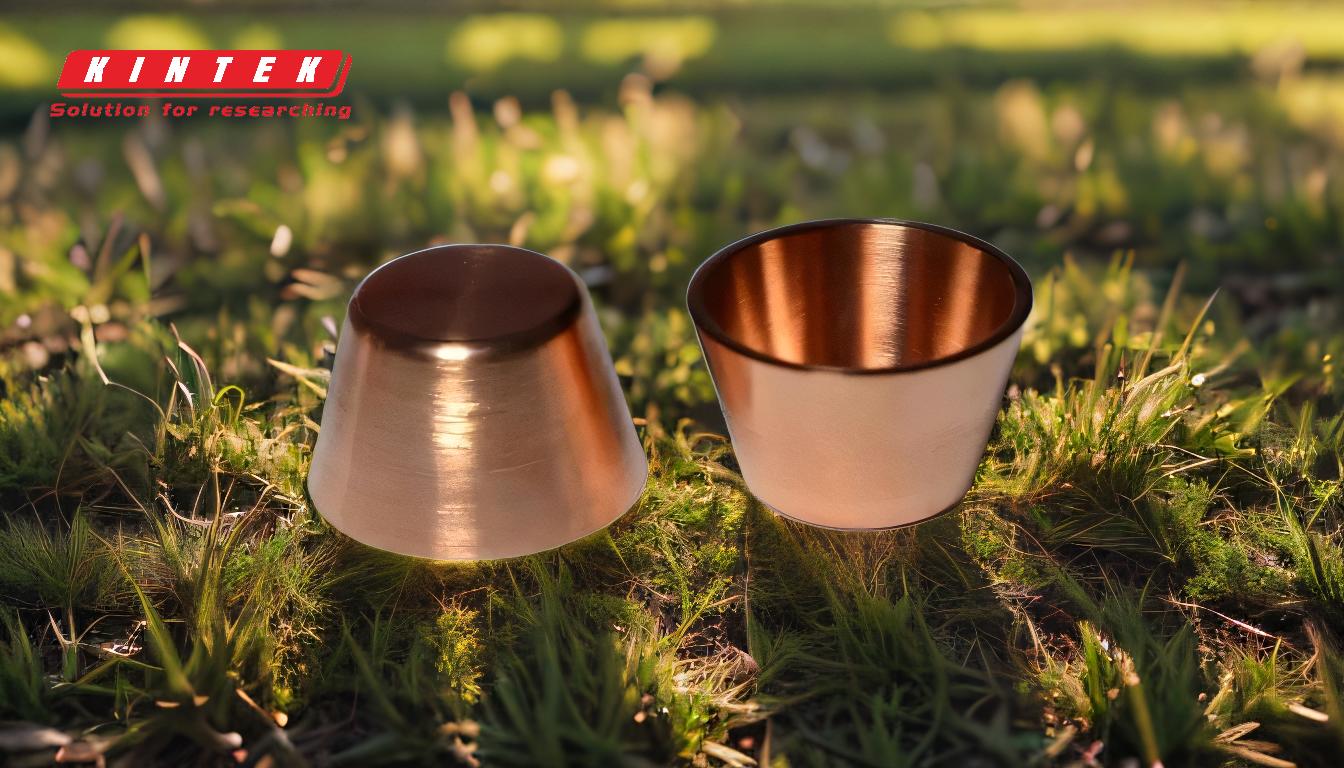
-
Generation of the Electron Beam:
- Thermionic Emission: The process begins with a tungsten filament heated by an electric current (5-10 kV). This heating causes the filament to emit electrons through thermionic emission.
- Electron Acceleration: The emitted electrons are accelerated by a high-voltage electric field, typically up to 15 keV, giving them high kinetic energy.
-
Focusing and Direction of the Electron Beam:
- Magnetic Field Focusing: A magnetic field is used to focus the high-energy electrons into a precise beam. This ensures that the electron beam is accurately directed onto the target material.
- Water-Cooled Crucible: The target material is placed in a water-cooled crucible to manage the intense heat generated by the electron beam.
-
Heating and Evaporation of the Target Material:
- Energy Transfer: When the electron beam strikes the target material, the kinetic energy of the electrons is converted into thermal energy, heating the material to extremely high temperatures.
- Vaporization: The heat causes the target material to evaporate or sublimate, releasing it into the vacuum chamber in a vapor phase.
-
Deposition onto the Substrate:
- Line of Sight Deposition: The vaporized material travels through the vacuum chamber and condenses onto the substrate, forming a thin film. This is a line-of-sight process, meaning the material deposits directly onto surfaces facing the vapor source.
- High Vacuum Environment: The vacuum environment (typically 10^-7 mbar or lower) minimizes contamination and allows for high vapor pressures at relatively low temperatures, ensuring a clean and high-quality deposition.
-
Advantages and Limitations:
- High Melting Point Materials: Electron beam evaporation is particularly effective for materials with very high melting points, which are difficult to evaporate using other methods.
- Limited Sidewall Coverage: The line-of-sight nature of the process means that it has limited ability to coat complex geometries or sidewalls, making it less suitable for certain applications requiring uniform coverage on intricate structures.
- Reactive Deposition: Reactive gases like oxygen or nitrogen can be introduced into the chamber to deposit non-metallic films, adding versatility to the process.
-
Applications:
- Semiconductor Industry: Used for depositing thin films of metals, oxides, and other materials in the fabrication of semiconductor devices.
- Optical Coatings: Ideal for creating high-quality optical coatings on lenses, mirrors, and other optical components.
- Decorative and Protective Coatings: Applied in industries requiring durable and aesthetically pleasing coatings on various substrates.
In summary, electron beam evaporation is a precise and efficient method for depositing thin films, particularly for materials with high melting points. Its ability to operate in a high vacuum environment ensures minimal contamination, making it a preferred choice for applications requiring high-purity coatings. However, its line-of-sight deposition characteristic limits its effectiveness in coating complex geometries.
Summary Table:
Aspect | Details |
---|---|
Process | Uses a focused electron beam to evaporate target materials in a vacuum. |
Key Components | Tungsten filament, magnetic field, water-cooled crucible, high vacuum. |
Advantages | High melting point material compatibility, minimal contamination. |
Limitations | Limited sidewall coverage, less effective for complex geometries. |
Applications | Semiconductors, optical coatings, decorative and protective coatings. |
Discover how electron beam evaporation can enhance your thin-film processes—contact us today for expert guidance!