Electron Beam Melting (EBM) is an advanced additive manufacturing process that uses a focused electron beam to melt and fuse powdered material layer by layer, based on a 3D CAD model. The process occurs in a vacuum environment, ensuring high precision and minimal contamination. The electron beam is controlled by a computer to selectively melt specific areas of the powder bed, building the desired object from the bottom up. This method is particularly suited for creating complex, near-net-shape parts with high mechanical integrity, making it a valuable technology in industries such as aerospace, medical, and automotive.
Key Points Explained:
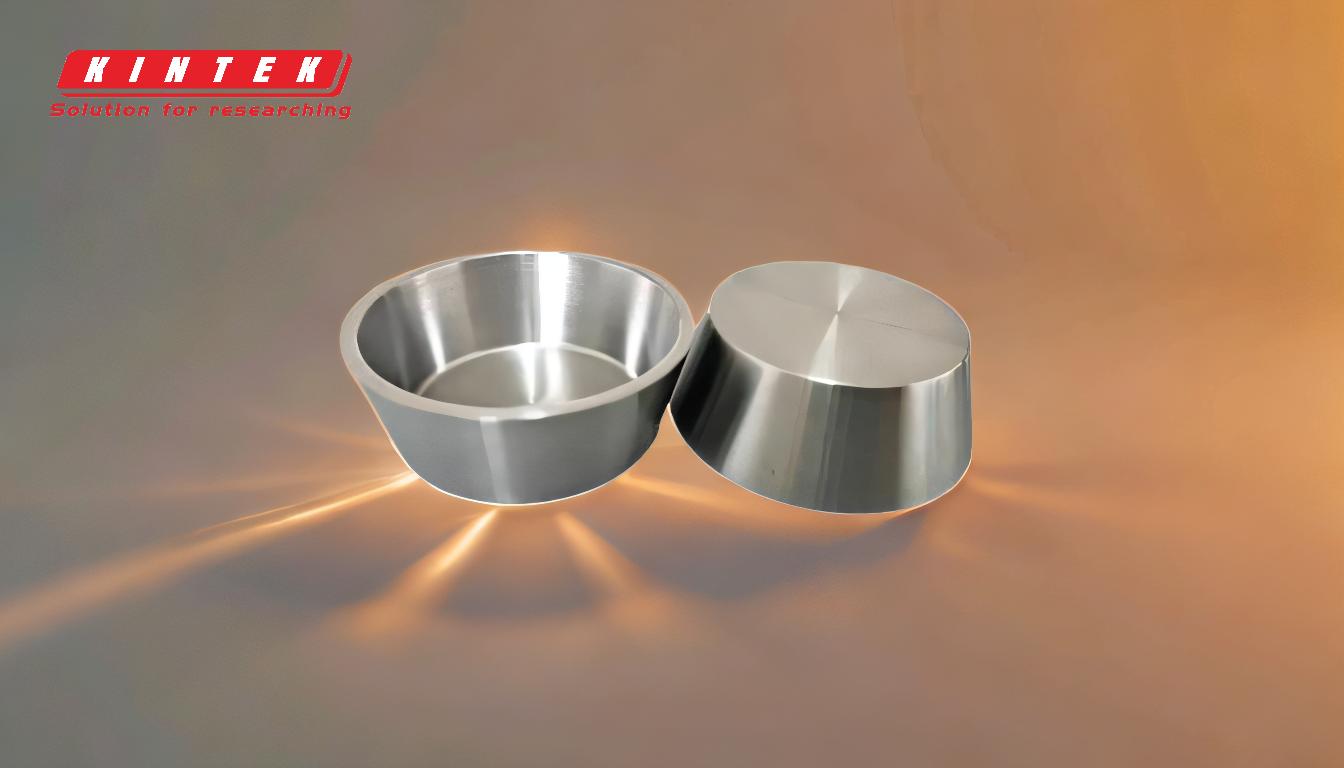
-
Process Overview:
- Layer-by-Layer Construction: EBM builds objects by depositing successive layers of powdered material. Each layer is selectively melted by a focused electron beam, which follows the design from a 3D CAD model.
- Vacuum Environment: The entire process takes place in a vacuum, which prevents oxidation and contamination, ensuring high-quality and precise parts.
-
Electron Beam Generation and Control:
- Electron Beam Generation: A magnet focuses electrons into a high-energy beam. This beam is then directed onto the powder bed.
- Computer-Controlled Scanning: The electron beam is precisely controlled by a computer, which guides it to melt specific areas of the powder according to the 3D model.
-
Material Melting and Fusion:
- Selective Melting: The electron beam selectively melts the powdered material, layer by layer. The energy from the beam causes the powder to melt and fuse together, forming a solid structure.
- Material Types: EBM can process a variety of materials, including metals and ceramics. Metals like aluminum melt and then evaporate, while ceramics sublimate directly from solid to vapor.
-
Advantages of EBM:
- High Precision: The computer-controlled electron beam allows for extremely precise melting, resulting in parts with high dimensional accuracy and complex geometries.
- Near-Net-Shape Parts: EBM can produce parts that are very close to the final desired shape, reducing the need for extensive post-processing.
- Mechanical Integrity: The vacuum environment and precise control result in parts with excellent mechanical properties, such as high strength and durability.
-
Applications:
- Aerospace: EBM is used to create lightweight, high-strength components for aircraft and spacecraft.
- Medical: The technology is employed to produce custom implants and prosthetics with complex geometries tailored to individual patients.
- Automotive: EBM is utilized to manufacture durable and precise parts for high-performance vehicles.
-
Comparison with Other Additive Manufacturing Techniques:
- EBM vs. Laser-Based Methods: Unlike laser-based additive manufacturing, EBM uses an electron beam, which can achieve higher energy densities and faster melting rates. This makes EBM particularly suitable for materials with high melting points.
- EBM vs. Traditional Manufacturing: EBM offers significant advantages over traditional manufacturing methods, including the ability to produce complex geometries that would be difficult or impossible to achieve with conventional techniques.
-
Environmental and Economic Benefits:
- Material Efficiency: EBM minimizes material waste by using only the necessary amount of powder to build the part.
- Energy Efficiency: The process is energy-efficient, as the electron beam can be precisely controlled to minimize energy consumption.
- Reduced Post-Processing: The high precision of EBM reduces the need for extensive post-processing, saving time and resources.
In summary, Electron Beam Melting is a sophisticated additive manufacturing process that leverages a focused electron beam to melt and fuse powdered material layer by layer in a vacuum environment. This method offers high precision, excellent mechanical properties, and the ability to produce complex, near-net-shape parts, making it a valuable technology across various industries.
Summary Table:
Aspect | Details |
---|---|
Process | Layer-by-layer melting of powdered material in a vacuum environment. |
Key Advantage | High precision, minimal contamination, and excellent mechanical integrity. |
Materials | Metals (e.g., aluminum) and ceramics. |
Applications | Aerospace, medical implants, automotive parts. |
Environmental Benefits | Material and energy efficiency, reduced post-processing. |
Interested in leveraging Electron Beam Melting for your industry? Contact us today to learn more!