The process of film deposition involves a series of chronological steps that are essential for achieving the desired characteristics of thin films. These steps include selecting a pure material source, transporting the material to a prepared substrate, depositing the material onto the substrate, and optionally annealing or heat-treating the film. Thin film deposition techniques are broadly categorized into chemical and physical methods, with Chemical Vapor Deposition (CVD) and Physical Vapor Deposition (PVD) being the most common. Each method has unique processes and applications, such as electron beam evaporation, sputtering, atomic layer deposition (ALD), and spray pyrolysis, which are used to produce high-quality thin films for various electronic and industrial applications.
Key Points Explained:
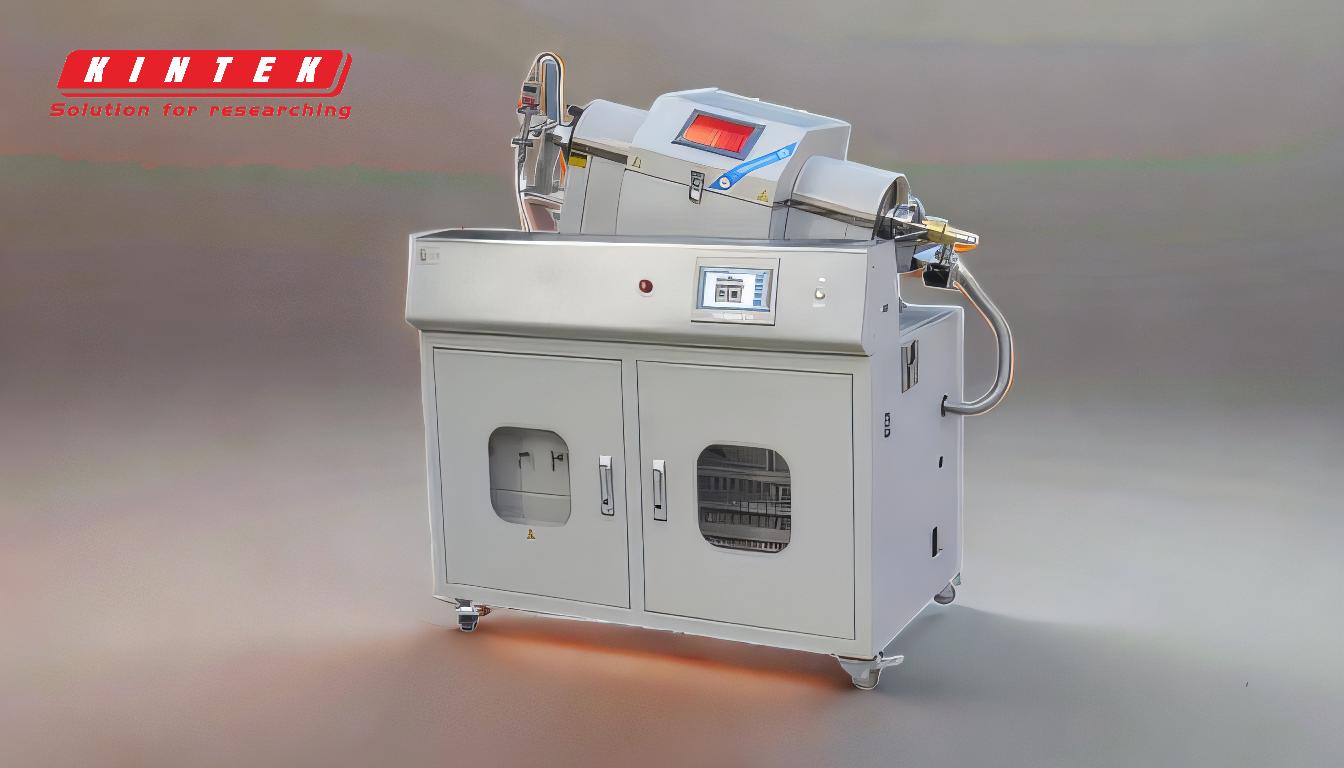
-
Selection of Material Source (Target):
- The process begins with selecting a pure material source, often referred to as the target. This material will be deposited onto the substrate to form the thin film.
- The choice of material depends on the desired properties of the film, such as conductivity, optical properties, or mechanical strength.
-
Transportation of Material to Substrate:
- The target material is transported to the substrate through a medium, which can be a fluid or a vacuum. This step is crucial for ensuring the material reaches the substrate in the desired state.
- In PVD methods like sputtering or evaporation, the material is transported in a vacuum environment. In CVD, the material is transported in a gaseous state.
-
Deposition onto Substrate:
- The material is deposited onto the substrate to form a thin film. This step varies significantly depending on the deposition technique used.
- PVD Techniques: Methods like sputtering and evaporation involve physically transferring the material from the target to the substrate.
- CVD Techniques: These involve chemical reactions to deposit the material onto the substrate. For example, in thermal CVD, the substrate is exposed to volatile precursors that react or decompose on the substrate surface.
- ALD: This method deposits the film one atomic layer at a time, allowing for precise control over film thickness and composition.
- The material is deposited onto the substrate to form a thin film. This step varies significantly depending on the deposition technique used.
-
Optional Annealing or Heat Treatment:
- After deposition, the thin film may undergo annealing or heat treatment to improve its properties. This step can enhance the film's crystallinity, reduce defects, or improve adhesion to the substrate.
- Annealing is particularly important in processes like thermal oxidation, where the film's properties are significantly influenced by heat treatment.
-
Analysis and Process Modification:
- The final step involves analyzing the properties of the deposited film, such as thickness, uniformity, and electrical or optical characteristics.
- Based on the analysis, the deposition process may be modified to achieve the desired film properties. This iterative process ensures the production of high-quality thin films.
-
Common Deposition Techniques:
- Chemical Vapor Deposition (CVD): Includes methods like plasma-enhanced CVD (PECVD), atomic layer deposition (ALD), and thermal oxidation. These techniques are used for depositing high-quality, uniform films.
- Physical Vapor Deposition (PVD): Includes techniques like sputtering, thermal evaporation, and electron beam evaporation. These methods are widely used for depositing metals and other materials in a vacuum environment.
- Spray Pyrolysis: Involves spraying a material solution onto the substrate and thermally degrading it to form a thin layer. This method is often used for depositing oxide films.
-
Applications of Thin Film Deposition:
- Thin films are used in a wide range of applications, including semiconductors, optical coatings, solar cells, and protective coatings.
- The choice of deposition technique depends on the specific application and the desired properties of the film.
By following these steps and selecting the appropriate deposition technique, manufacturers can produce thin films with precise properties tailored to specific applications.
Summary Table:
Step | Description |
---|---|
Selection of Material Source | Choose a pure material (target) based on desired film properties. |
Transportation to Substrate | Transport material via vacuum (PVD) or gaseous state (CVD). |
Deposition onto Substrate | Use PVD (sputtering, evaporation) or CVD (thermal, ALD) techniques. |
Optional Annealing | Heat-treat the film to improve crystallinity, adhesion, and reduce defects. |
Analysis & Modification | Analyze film properties and refine the process for optimal results. |
Common Techniques | CVD (PECVD, ALD), PVD (sputtering, evaporation), and spray pyrolysis. |
Applications | Semiconductors, optical coatings, solar cells, and protective coatings. |
Discover how to optimize your film deposition process—contact our experts today!