Gold sputtering is a specialized thin-film deposition technique used to coat substrates with a fine, even layer of gold. This process is widely used in industries such as electronics, optics, and materials science due to gold's excellent conductivity, corrosion resistance, and aesthetic appeal. The process involves creating a vacuum environment, bombarding a gold target with high-energy ions to eject gold atoms, and depositing these atoms onto a substrate. The result is a uniform, high-quality gold coating that adheres well to the surface. The process is highly controlled, requiring precise management of vacuum levels, temperature, and energy inputs to ensure optimal results.
Key Points Explained:
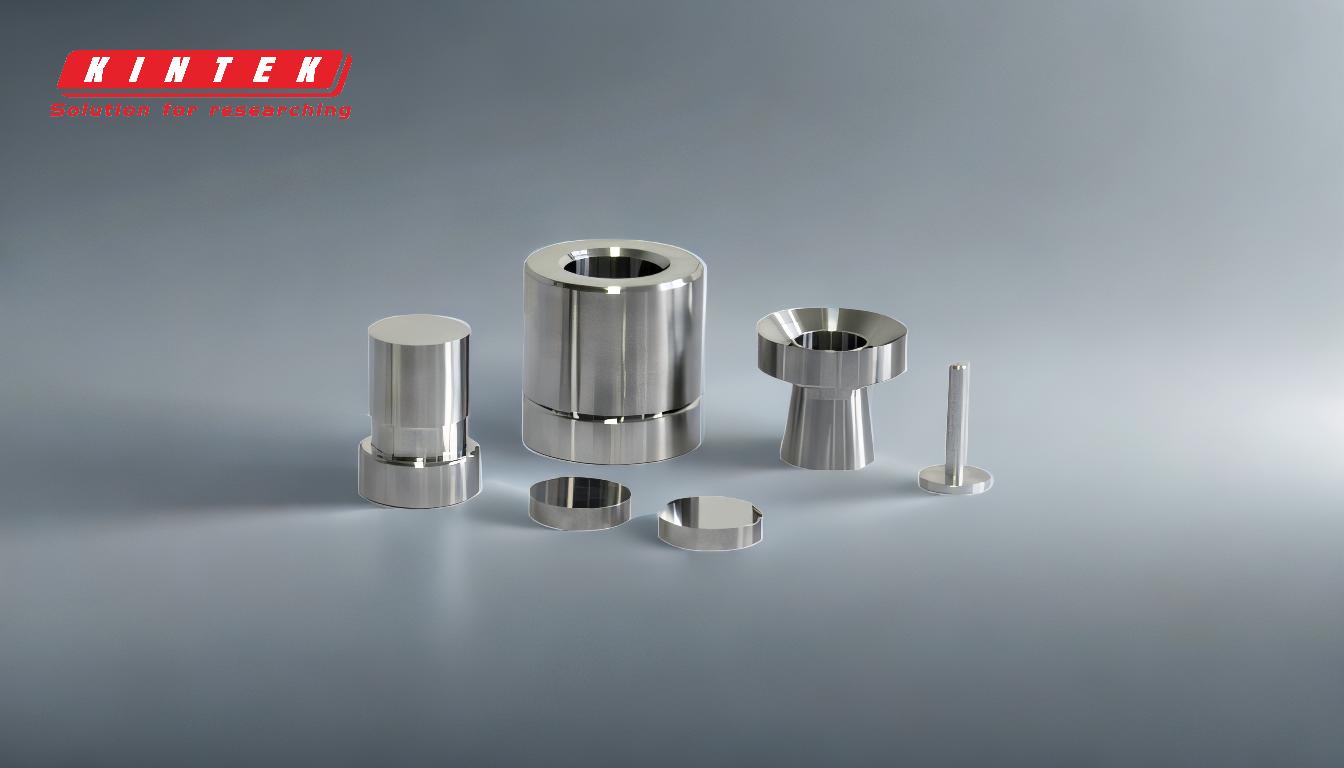
-
Vacuum Environment Setup:
- The sputtering process begins by creating a vacuum in the deposition chamber. This is crucial because it removes air and other gases that could interfere with the deposition process. The substrate is mounted on a holder in a load lock chamber, which is then evacuated to achieve the necessary vacuum. The vacuum environment ensures that the sputtered gold atoms travel unimpeded to the substrate, resulting in a clean and uniform coating.
-
Target Material Preparation:
- The gold target, typically in the form of a disc, is placed in the sputter gun. This target is the source of the gold atoms that will be deposited onto the substrate. Before the actual sputtering begins, a pre-sputtering step is often performed to clean the target surface. This involves bombarding the target with ions to remove any surface contaminants, ensuring that only pure gold atoms are ejected during the deposition process.
-
Ion Bombardment and Sputtering:
- High-energy ions, usually from an inert gas like argon, are directed at the gold target. These ions collide with the gold atoms, transferring enough energy to eject them from the target surface. This process is driven by momentum exchange between the ions and the gold atoms. The ejected gold atoms enter the gas phase and are transported through the vacuum chamber toward the substrate. The energy of the ions and the vacuum conditions are carefully controlled to ensure a consistent and even deposition.
-
Deposition and Film Formation:
- The sputtered gold atoms travel through the vacuum and condense onto the substrate, forming a thin, uniform film. The substrate is typically held at a controlled temperature to promote adhesion and film quality. The thickness of the gold layer can be precisely controlled by adjusting the duration of the sputtering process and the power applied to the sputter gun. This step is critical for achieving the desired electrical, optical, or decorative properties of the coating.
-
Post-Deposition Cooling and Venting:
- After the deposition is complete, the chamber undergoes a ramp-down stage. This involves gradually reducing the temperature and pressure to return the chamber to ambient conditions. Cooling systems are used to manage the heat generated during the process, ensuring that the substrate and equipment are not damaged. Once the chamber is at room temperature and pressure, the coated substrate can be safely removed.
-
Applications and Advantages:
- Gold sputtering is used in a variety of applications, including semiconductor manufacturing, optical coatings, and decorative finishes. The process offers several advantages, such as the ability to deposit extremely thin and uniform layers, excellent adhesion to the substrate, and high purity of the deposited gold. Additionally, the vacuum environment minimizes contamination, resulting in high-quality coatings with consistent properties.
By following these steps, gold sputtering provides a reliable and precise method for creating thin gold films with exceptional properties, making it an essential technique in many high-tech industries.
Summary Table:
Step | Description |
---|---|
1. Vacuum Environment Setup | Create a vacuum in the deposition chamber to ensure clean, uniform gold coating. |
2. Target Material Preparation | Clean the gold target surface to eject pure gold atoms during sputtering. |
3. Ion Bombardment & Sputtering | Use high-energy ions to eject gold atoms from the target. |
4. Deposition & Film Formation | Sputtered gold atoms condense on the substrate, forming a thin, uniform layer. |
5. Post-Deposition Cooling | Gradually cool and vent the chamber to safely remove the coated substrate. |
6. Applications & Advantages | Used in semiconductors, optics, and decorative finishes for high-quality results. |
Discover how gold sputtering can enhance your projects—contact our experts today!