The High-Density Plasma Chemical Vapor Deposition (HDP-CVD) process is a specialized form of CVD used primarily in semiconductor manufacturing to deposit thin films with high uniformity and density. This process leverages high-density plasma to enhance the chemical reactions necessary for film deposition. The HDP-CVD process involves preparing a semiconductor substrate, placing it in a process chamber, and generating high-density plasma. The plasma is created by injecting oxygen and silicon source gases, which react to form a silicon oxide layer. The substrate is heated to high temperatures (550°C to 700°C) to facilitate the reaction. Secondary and primary gases, such as helium, are also introduced to optimize the deposition process. This method is particularly advantageous for creating high-quality, dense films with excellent step coverage, making it ideal for advanced semiconductor applications.
Key Points Explained:
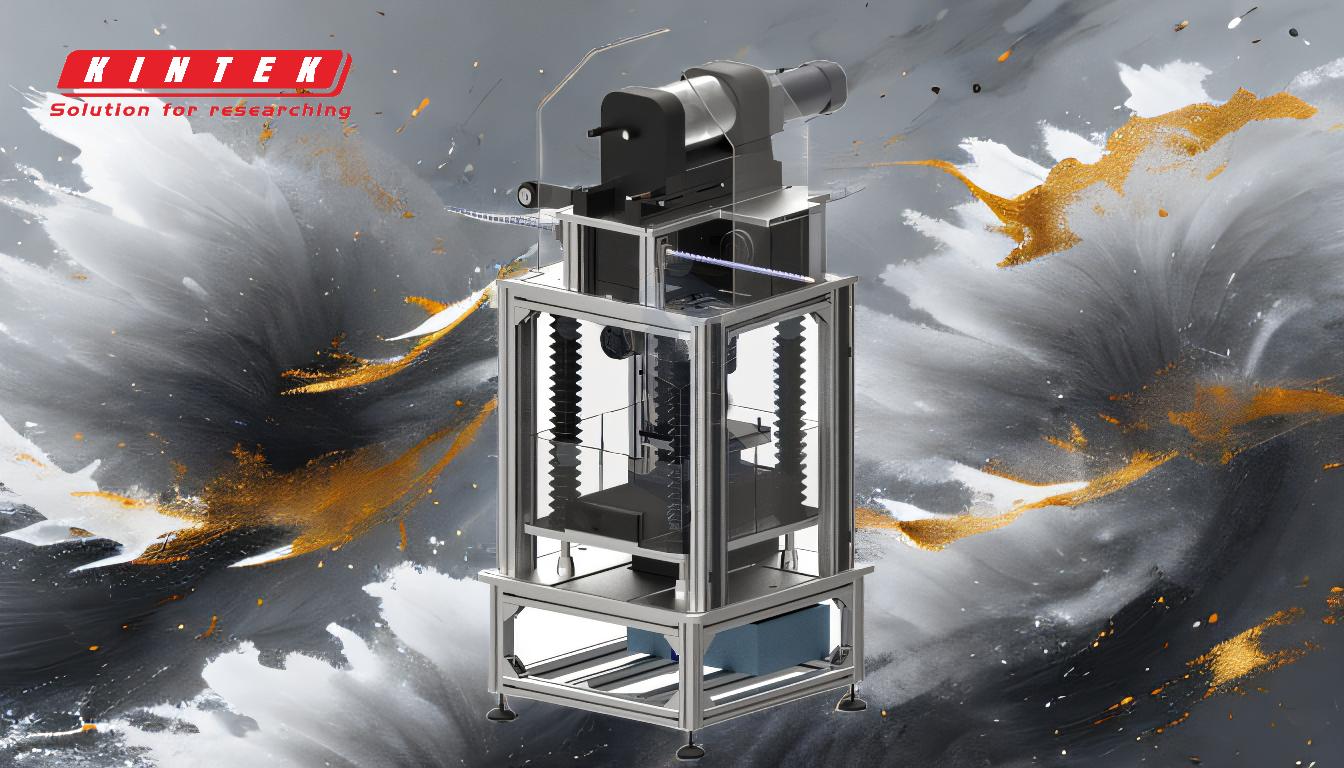
-
Substrate Preparation:
- The process begins with the preparation of a semiconductor substrate. This involves cleaning and sometimes pre-treating the substrate to ensure it is free of contaminants and has the necessary surface properties for optimal film adhesion.
-
Placing the Substrate in the Process Chamber:
- The prepared substrate is then placed inside a process chamber. This chamber is designed to maintain controlled conditions such as temperature, pressure, and gas flow rates, which are critical for the deposition process.
-
Generating High-Density Plasma:
- High-density plasma is generated within the chamber. This is achieved by injecting oxygen and silicon source gases, which are ionized to create a plasma state. The high-density plasma enhances the chemical reactions needed for the deposition of the thin film.
-
Formation of Silicon Oxide Layer:
- The primary reaction in HDP-CVD involves the formation of a silicon oxide layer. The oxygen and silicon source gases react in the plasma to produce silicon dioxide (SiO₂), which deposits onto the substrate.
-
Injection of Secondary and Primary Gases:
- Secondary and primary gases, such as helium, are introduced into the chamber. These gases help to stabilize the plasma, improve film quality, and ensure uniform deposition across the substrate.
-
Heating the Substrate:
- The substrate is heated to temperatures between 550°C and 700°C. This high temperature is necessary to facilitate the chemical reactions and ensure the deposited film has the desired properties, such as density and uniformity.
-
Advantages of HDP-CVD:
- High-Quality Films: HDP-CVD produces films with high density and excellent step coverage, which are crucial for advanced semiconductor devices.
- Uniformity: The use of high-density plasma ensures uniform deposition across the substrate, even on complex geometries.
- Controlled Properties: By adjusting parameters such as temperature, pressure, and gas flow rates, the chemical and physical properties of the films can be precisely controlled.
-
Applications:
- HDP-CVD is widely used in the semiconductor industry for depositing dielectric layers, such as silicon dioxide, in integrated circuits. It is also used in the fabrication of microelectromechanical systems (MEMS) and other advanced electronic devices.
In summary, the HDP-CVD process is a sophisticated and highly controlled method for depositing thin films with exceptional quality and uniformity. Its ability to produce dense, high-purity films makes it indispensable in the semiconductor industry.
Summary Table:
Step | Description |
---|---|
Substrate Preparation | Clean and pre-treat the semiconductor substrate for optimal film adhesion. |
Placing in Process Chamber | Place the substrate in a controlled environment for temperature, pressure, and gas flow. |
Generating High-Density Plasma | Inject oxygen and silicon source gases to create plasma for enhanced reactions. |
Formation of Silicon Oxide | React gases to form a silicon oxide layer (SiO₂) on the substrate. |
Injection of Secondary Gases | Introduce gases like helium to stabilize plasma and improve film quality. |
Heating the Substrate | Heat substrate to 550°C–700°C to facilitate reactions and ensure film uniformity. |
Advantages | High-quality, dense films with excellent step coverage and uniformity. |
Applications | Used in semiconductor manufacturing for dielectric layers and MEMS fabrication. |
Discover how HDP-CVD can enhance your semiconductor manufacturing process—contact our experts today!