Induction brazing is a process that uses electromagnetic induction to heat and join two or more metal components using a filler material. Unlike furnace brazing, which heats the entire assembly uniformly, induction brazing targets specific areas, making it highly efficient for localized heating. The process involves generating an alternating magnetic field around the workpiece, which induces eddy currents within the metal. These currents generate heat due to electrical resistance, melting the filler material and creating a strong bond upon cooling. Induction brazing is widely used in industries requiring precision, such as automotive, aerospace, and electronics, due to its rapid heating, minimal oxidation, and ability to handle complex geometries.
Key Points Explained:
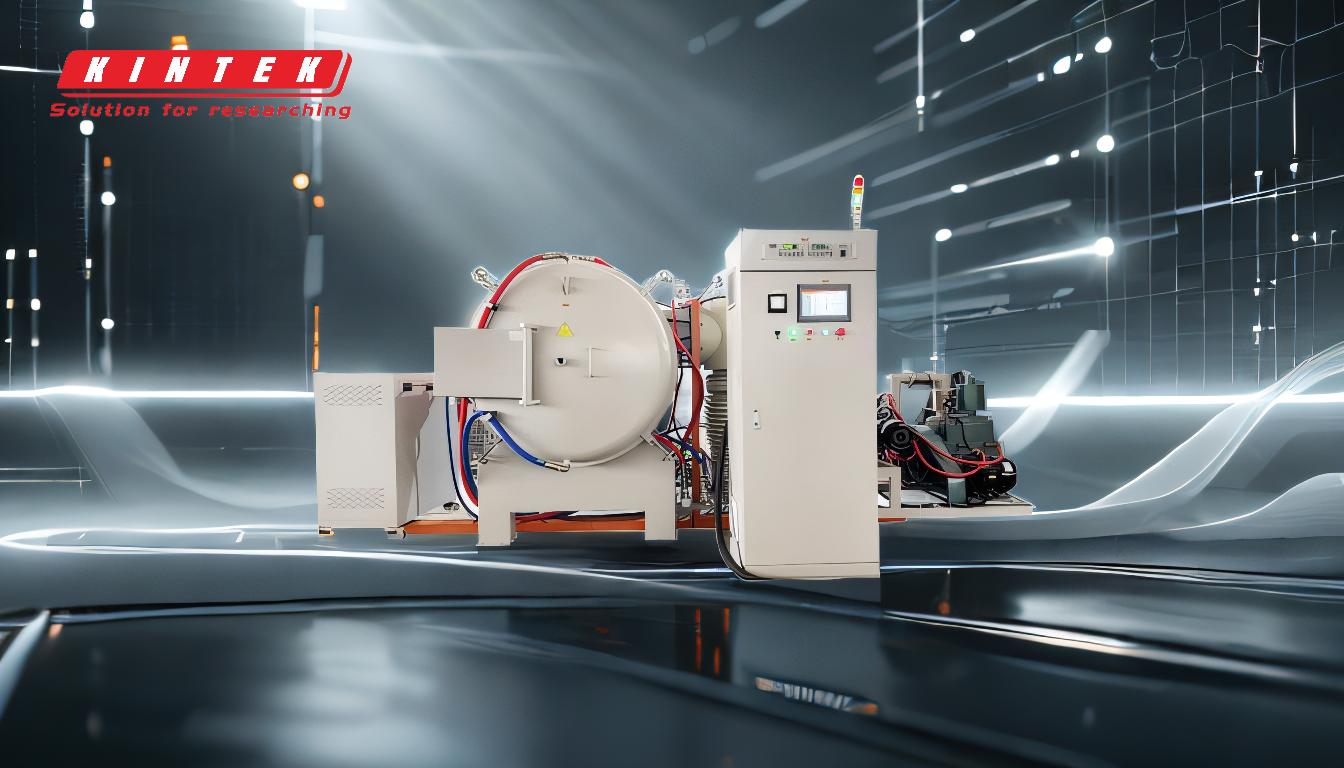
-
Principle of Induction Heating:
- Induction brazing relies on electromagnetic induction to generate heat. An alternating current passes through a coil, creating a magnetic field around the workpiece. This magnetic field induces eddy currents within the metal, which produce heat due to the material's electrical resistance. The heat is localized, allowing precise control over the brazing process.
-
Components of Induction Brazing:
- Induction Coil: The coil generates the magnetic field and is designed to match the shape of the workpiece for optimal heating.
- Power Supply: Provides the alternating current required for induction heating.
- Filler Material: A metal alloy with a lower melting point than the base materials, used to create the joint.
- Flux or Protective Atmosphere: Prevents oxidation during the brazing process, ensuring a clean and strong joint.
-
Steps in Induction Brazing:
- Preparation: Clean the metal surfaces to remove contaminants and ensure proper joint fit-up.
- Assembly: Position the filler material (e.g., preplaced rings or paste) at the joint and secure the components.
- Heating: Activate the induction coil to heat the joint area until the filler material melts and flows into the joint.
- Cooling: Allow the assembly to cool naturally or use controlled cooling to solidify the filler material.
- Post-Processing: Clean the brazed assembly to remove any residual flux or oxidation.
-
Advantages of Induction Brazing:
- Localized Heating: Only the joint area is heated, reducing thermal distortion and energy consumption.
- Speed: Rapid heating and cooling cycles improve production efficiency.
- Precision: Suitable for complex geometries and delicate components.
- Minimal Oxidation: The use of flux or a protective atmosphere ensures clean joints.
-
Applications of Induction Brazering:
- Automotive: Used for joining components like turbochargers, sensors, and fuel injectors.
- Aerospace: Ideal for brazing turbine blades, heat exchangers, and other critical parts.
- Electronics: Used for assembling connectors, heat sinks, and other precision components.
-
Comparison with Other Brazing Methods:
- Furnace Brazing: Heats the entire assembly uniformly, suitable for mass production but less precise for localized joints.
- Vacuum Brazing: Performed in a vacuum environment to prevent oxidation, ideal for high-purity applications but requires specialized equipment.
- Flame Brazing: Uses a torch for heating, which is less controlled and more prone to oxidation compared to induction brazing.
-
Challenges and Considerations:
- Coil Design: The coil must be tailored to the workpiece geometry to ensure even heating.
- Material Compatibility: The base and filler materials must have compatible thermal and metallurgical properties.
- Process Control: Precise control of heating time and temperature is critical to avoid defects like incomplete joints or overheating.
Induction brazing is a versatile and efficient method for joining metals, offering significant advantages in terms of precision, speed, and quality. Its ability to target specific areas makes it particularly valuable for industries requiring high-performance components.
Summary Table:
Aspect | Details |
---|---|
Principle | Electromagnetic induction heats metal via eddy currents for localized brazing. |
Components | Induction coil, power supply, filler material, flux/protective atmosphere. |
Steps | Preparation, assembly, heating, cooling, post-processing. |
Advantages | Localized heating, speed, precision, minimal oxidation. |
Applications | Automotive, aerospace, electronics. |
Comparison | More precise than furnace brazing, cleaner than flame brazing. |
Challenges | Coil design, material compatibility, process control. |
Discover how induction brazing can elevate your manufacturing process—contact our experts today!