Ion Beam Deposition (IBD) is a precise and controlled physical vapor deposition (PVD) technique used to deposit thin films onto a substrate. The process involves generating a monoenergetic and highly collimated ion beam that sputters atoms from a target material, which then condense onto a substrate to form a thin film. The system typically includes an ion source, a target, and a substrate, with some configurations incorporating a second ion source for ion-assisted deposition to enhance film quality. The process is characterized by its ability to produce uniform, high-quality films with strong adhesion, making it suitable for applications in optics, electronics, and advanced materials.
Key Points Explained:
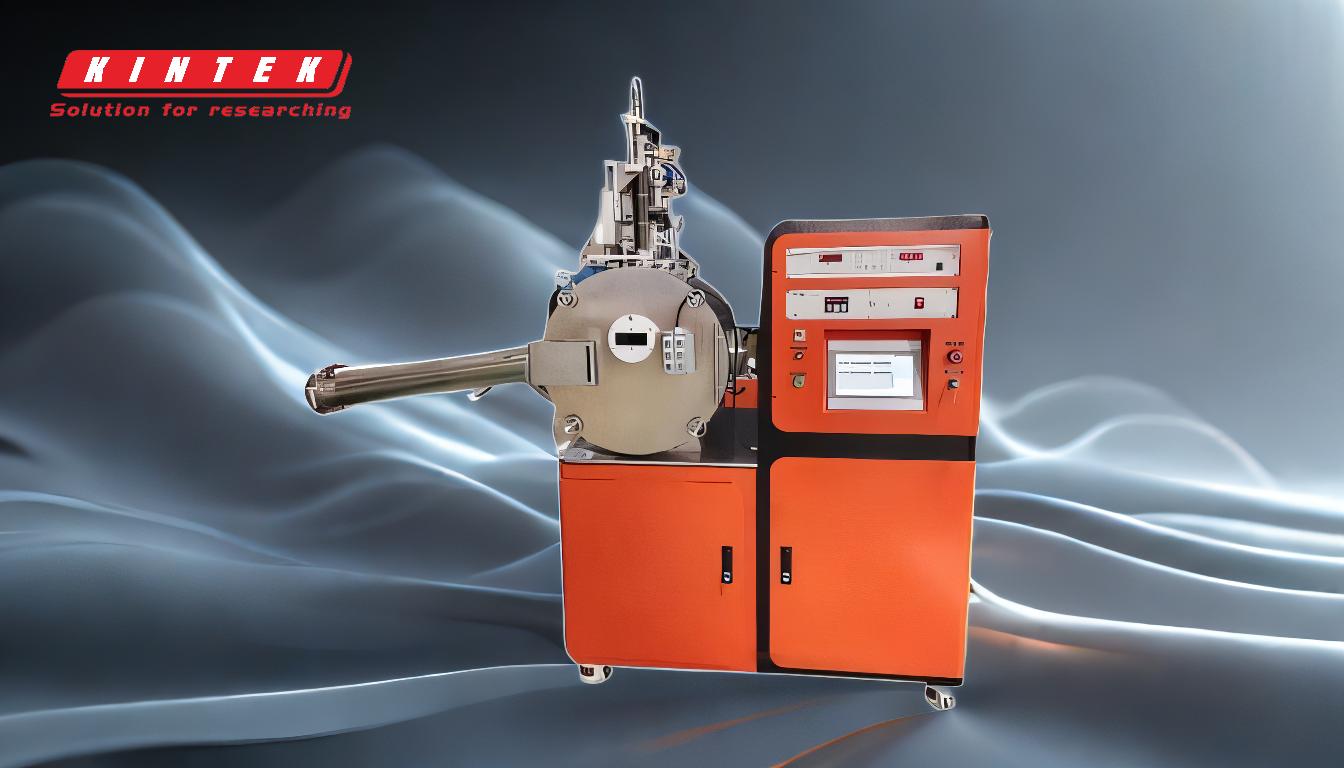
-
Components of an Ion Beam Deposition System:
- Ion Source: Generates a beam of ions with equal energy, ensuring the process is monoenergetic and highly collimated. This source is critical for controlling the energy and direction of the ions.
- Target Material: The material to be sputtered. The ion beam strikes the target, ejecting atoms or molecules from its surface.
- Substrate: The surface onto which the sputtered material is deposited, forming a thin film. The substrate is positioned in proximity to the target to ensure efficient deposition.
- Optional Second Ion Source: Some systems include a second gridded ion source directed at the substrate to assist in the deposition process, improving film adhesion and quality.
-
Process of Ion Beam Deposition:
- Ion Beam Generation: The ion source produces a beam of ions, typically using a broad-beam ion source with high-voltage acceleration. The ions are monoenergetic, meaning they all have the same energy, which ensures uniformity in the sputtering process.
- Sputtering: The ion beam is directed at the target material. When the ions strike the target, they transfer their energy to the target atoms, causing them to be ejected from the surface. This process is known as sputtering.
- Deposition: The sputtered atoms or molecules travel through the vacuum environment and condense onto the substrate, forming a thin film. The deposition occurs in a controlled manner, ensuring a uniform and tightly bonded layer.
-
Characteristics of Ion Beam Deposition:
- Monoenergetic Ions: The use of ions with equal energy ensures a highly controlled and uniform sputtering process, which is critical for producing high-quality thin films.
- High Collimation: The ion beam is highly collimated, meaning it is focused and directional. This reduces scattering and ensures precise deposition onto the substrate.
- Ion-Assisted Deposition (Optional): In some configurations, a second ion source is used to bombard the substrate during deposition. This ion-assisted deposition enhances the adhesion and density of the thin film, improving its mechanical and optical properties.
-
Advantages of Ion Beam Deposition:
- Precision and Control: The monoenergetic and collimated nature of the ion beam allows for precise control over the deposition process, resulting in uniform and high-quality films.
- Strong Adhesion: The sputtered atoms form a tight bond with the substrate, ensuring excellent adhesion and durability of the deposited film.
- Versatility: IBD can be used with a wide range of target materials and substrates, making it suitable for various applications, including optics, electronics, and advanced materials.
-
Applications of Ion Beam Deposition:
- Optical Coatings: IBD is widely used to deposit thin films for optical applications, such as anti-reflective coatings, filters, and mirrors, due to its ability to produce uniform and high-quality films.
- Electronics: The technique is employed in the fabrication of semiconductor devices, where precise control over film thickness and composition is essential.
- Advanced Materials: IBD is used in the development of advanced materials, such as superconductors, magnetic films, and nanostructured materials, where high-quality thin films are required.
In summary, Ion Beam Deposition is a highly controlled and precise PVD technique that uses a monoenergetic and collimated ion beam to sputter target material onto a substrate, forming high-quality thin films. The process is characterized by its precision, strong adhesion, and versatility, making it suitable for a wide range of applications in optics, electronics, and advanced materials.
Summary Table:
Aspect | Details |
---|---|
Components | Ion source, target material, substrate, optional second ion source |
Process | Ion beam generation, sputtering, deposition |
Characteristics | Monoenergetic ions, high collimation, ion-assisted deposition (optional) |
Advantages | Precision, strong adhesion, versatility |
Applications | Optical coatings, electronics, advanced materials |
Discover how Ion Beam Deposition can elevate your projects—contact our experts today!