Ion plating is a Physical Vapor Deposition (PVD) process that involves the deposition of thin films on a substrate using ion bombardment. This method is characterized by its ability to deposit materials at lower temperatures and higher rates compared to traditional PVD techniques. The process involves vaporizing the coating material, ionizing it, and then accelerating the ions toward the substrate to form a uniform coating. Ion plating is known for its versatility, as it can use various methods to vaporize the material, such as evaporation, sputtering, or arc erosion. The energetic particle bombardment during deposition modifies the film's properties, enhancing adhesion, composition, and surface coverage. This technique is ideal for applications requiring high uniformity and is widely used in industries such as aerospace, automotive, and electronics.
Key Points Explained:
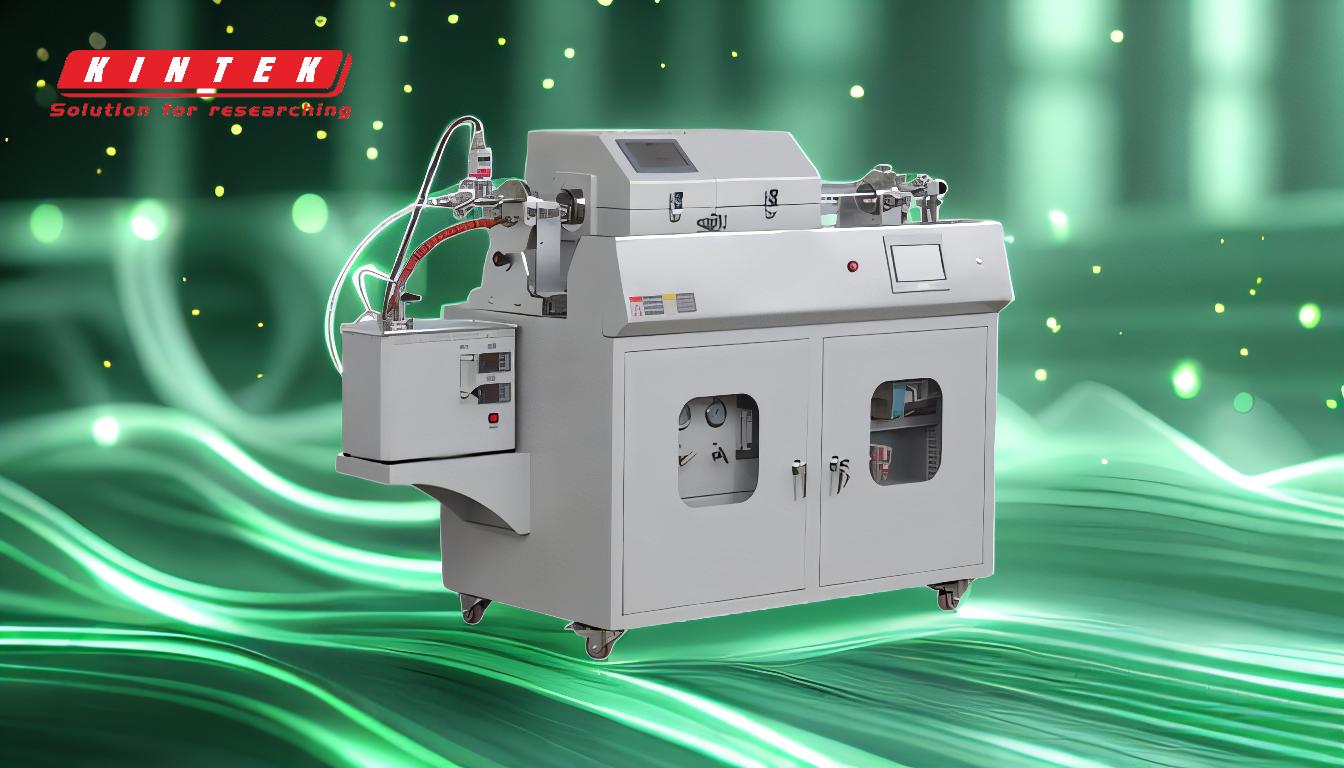
-
Introduction to Ion Plating:
- Ion plating is a PVD process that deposits thin films on a substrate using ion bombardment.
- It is similar to sputter deposition but uses ions instead of electrons, allowing for lower temperature deposition and higher rates.
-
Vaporization Methods:
- The coating material can be vaporized using various methods:
- Evaporation: Heating the material until it vaporizes.
- Sputtering: Bombarding the target material with ions to eject atoms.
- Arc Erosion: Using an electric arc to vaporize the material.
- Chemical Vapor Precursor Decomposition: Breaking down a chemical precursor to release the coating material.
- The coating material can be vaporized using various methods:
-
Ion Bombardment:
- During deposition, the substrate is bombarded with energetic particles (ions) to modify the film's properties.
- Bombardment can be done using ions of inert gases (e.g., argon) or reactive gases (e.g., nitrogen), or even ions of the film material itself.
- The ions can be extracted from a plasma or generated using a separate ion gun (ion beam-assisted deposition).
-
Ionization and Acceleration:
- The gas containing the coating material is ionized in a vacuum chamber.
- The ions are then accelerated and directed toward the substrate, ensuring a uniform and consistent coating.
- This process is particularly beneficial for applications requiring high uniformity and precise control over film properties.
-
Advantages of Ion Plating:
- Lower Temperature Deposition: Suitable for temperature-sensitive substrates.
- Higher Deposition Rates: Faster coating compared to traditional methods.
- Enhanced Film Properties: Improved adhesion, composition, and surface coverage due to ion bombardment.
- Versatility: Can be used with a wide range of materials and substrates.
-
Applications:
- Aerospace: Coatings for turbine blades and other high-performance components.
- Automotive: Wear-resistant coatings for engine parts.
- Electronics: Thin films for semiconductors and optical coatings.
- Medical Devices: Biocompatible coatings for implants.
-
Comparison with Other PVD Techniques:
- Thermal Evaporation: Ion plating combines thermal evaporation with ion bombardment, offering better film properties.
- Sputtering: While both use ion bombardment, ion plating typically offers higher deposition rates and better adhesion.
-
Process Control and Optimization:
- Plasma Generation: The quality of the plasma significantly affects the deposition process. Parameters such as gas pressure, ion energy, and substrate bias must be carefully controlled.
- Substrate Preparation: Proper cleaning and surface treatment of the substrate are crucial for achieving good adhesion and film quality.
- Monitoring and Feedback: Real-time monitoring of the deposition process helps in optimizing parameters and ensuring consistent film properties.
In summary, ion plating is a versatile and efficient PVD technique that offers numerous advantages over traditional methods. Its ability to deposit high-quality films at lower temperatures and higher rates makes it suitable for a wide range of industrial applications. The process involves careful control of vaporization, ionization, and ion bombardment to achieve the desired film properties.
Summary Table:
Aspect | Details |
---|---|
Process | Physical Vapor Deposition (PVD) using ion bombardment |
Key Features | Lower temperature deposition, higher rates, enhanced film properties |
Vaporization Methods | Evaporation, sputtering, arc erosion, chemical vapor precursor decomposition |
Applications | Aerospace, automotive, electronics, medical devices |
Advantages | Improved adhesion, composition, surface coverage, versatility |
Unlock the potential of ion plating for your industry—contact our experts today to learn more!