The process of isostatic graphite manufacturing is a multi-stage procedure that transforms raw materials like coke and pitch into high-performance graphite with uniform properties. The key steps include coke production, pulverizing, kneading, isostatic molding, carbonizing, pitch impregnation, graphitizing, and post-processing stages like machining and purification. Isostatic molding, a critical step, involves applying high pressure uniformly to powdered carbon in a flexible mold to achieve a symmetrical and dense structure. The resulting graphite exhibits exceptional thermal and chemical resistance, high electrical and thermal conductivity, and ease of machining, making it suitable for demanding applications in industries like semiconductors, aerospace, and metallurgy.
Key Points Explained:
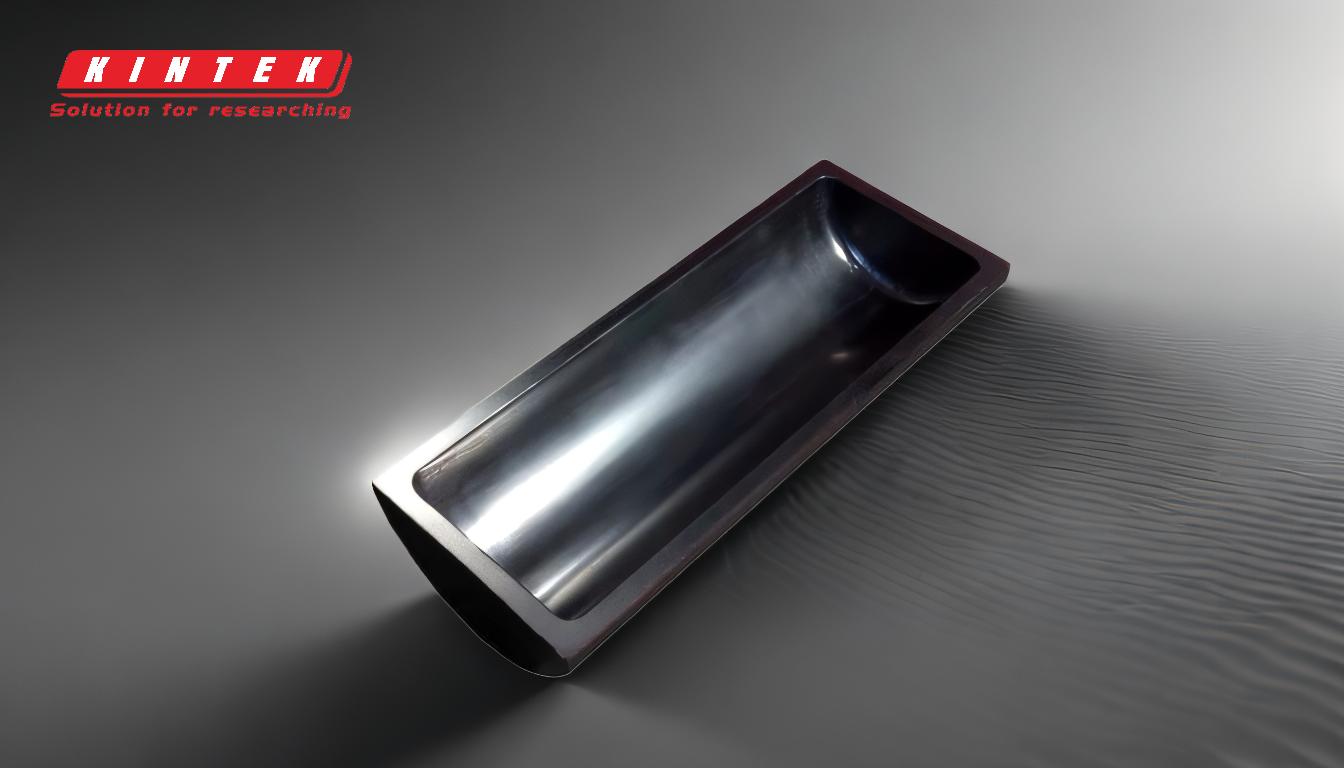
-
Raw Material Preparation:
- The process begins with the production of coke, a carbon-rich material derived from coal or petroleum. This coke is then pulverized into fine particles.
- Pitch, a binding agent, is mixed with the pulverized coke to form a homogeneous mixture. This step ensures the carbon particles are evenly distributed and bound together.
-
Isostatic Molding:
- The mixture is loaded into a flexible mold, which is then sealed to prevent leakage.
- High pressure, typically over 150 MPa, is applied uniformly via a liquid medium in a pressure vessel. This isostatic molding process ensures the grains are symmetrically arranged and evenly distributed, resulting in a dense and uniform structure.
- After pressing, the compacted powder body is removed from the mold, ready for further processing.
-
Carbonizing:
- The molded body is heated in an oxygen-free environment to temperatures around 800-1000 °C. This step removes volatile components and converts the pitch into a solid carbon matrix, strengthening the structure.
-
Pitch Impregnation:
- To further enhance density and mechanical properties, the carbonized body is impregnated with pitch. This step fills any remaining pores and improves the material's uniformity.
-
Graphitizing:
- The impregnated body is heat-treated at extremely high temperatures (2500-2800 °C) in a graphitizing furnace. This process transforms the amorphous carbon into crystalline graphite, imparting superior thermal and electrical conductivity.
-
Post-Processing:
- Inspection: The graphite blocks are inspected for defects and uniformity.
- Machining: The material is easily machined into precise shapes and sizes, making it versatile for various applications.
- Purification: High-purity graphite is achieved by removing impurities, often reducing them to levels below 5 ppm.
- Surface Treatment: Additional treatments may be applied to enhance surface properties or prepare the graphite for specific uses.
-
Properties of Isostatic Graphite:
- High Thermal and Chemical Resistance: Suitable for extreme environments.
- Excellent Thermal Shock Resistance: Can withstand rapid temperature changes without cracking.
- High Electrical and Thermal Conductivity: Ideal for applications requiring efficient heat and electricity transfer.
- Increasing Strength with Temperature: Performs well under high-temperature conditions.
- Ease of Machining: Allows for precise fabrication of complex components.
-
Applications:
- Isostatic graphite is widely used in industries such as semiconductors, aerospace, metallurgy, and energy due to its exceptional properties and versatility.
The manufacturing process of isostatic graphite is a sophisticated and meticulously controlled procedure, ensuring the final product meets the stringent requirements of advanced industrial applications.
Summary Table:
Step | Description |
---|---|
Raw Material Prep | Coke production, pulverizing, and mixing with pitch for a homogeneous mixture. |
Isostatic Molding | High-pressure molding in a flexible mold for a dense, uniform structure. |
Carbonizing | Heating to 800-1000 °C to remove volatiles and strengthen the carbon matrix. |
Pitch Impregnation | Impregnating with pitch to enhance density and uniformity. |
Graphitizing | Heat-treating at 2500-2800 °C to transform carbon into crystalline graphite. |
Post-Processing | Inspection, machining, purification, and surface treatment for final use. |
Key Properties | High thermal/chemical resistance, excellent conductivity, and ease of machining. |
Applications | Semiconductors, aerospace, metallurgy, and energy industries. |
Discover how isostatic graphite can elevate your industrial applications—contact us today for expert guidance!